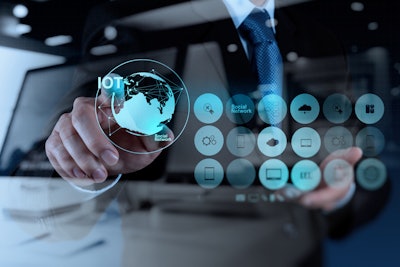
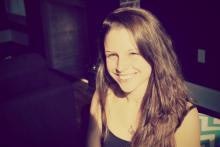
Efficiency has always been crucial for success in manufacturing and industry. That reality is why a growing number of entities have adopted smart technologies or are at least heavily considering doing so this year.
Automation, metrics-driven software suites and other high-tech solutions improve quality control while reducing worker fatigue — both advantages that tend to result in satisfied stakeholders. Several smart factory trends are particularly worth implementing in 2018.
1. Connected Devices for Safer Work Behaviors
Analysts believe the Internet of Things (IoT) shows substantial potential in the industrial sector. Wi-Fi-enabled sensors on shop floors could aid in inventory management by providing information that supports loss prevention strategies.
Furthermore, some workers are even wearing IoT devices to stay safer in dangerous environments. North Star BlueScope Steel — a company that makes materials for builders in North America, New Zealand and Australia — partnered with IBM to investigate IoT devices that measure risk. The wearables embed into employees’ helmets and wristbands and then transmit data to supervisors when safety procedures are not being followed or workers are engaged in activities that could compromise their well-being.
Statistics published in the 2016 Liberty Mutual Workplace Safety Index indicate job-related accidents cost United States-based businesses almost $62 billion per year. Factory managers who invest in IoT devices to prevent accidents are doing something practical to support their bottom lines while reducing risk. If those initiatives go well, they could easily use IoT technology for other industrial applications, too.
2. Predictive Maintenance Measures
An unexpected breakdown can become immensely costly for a usually efficient factory. Even delays of a few minutes can cost tens of thousands of dollars as the seconds tick on. Things become increasingly complicated for global companies that have factories all over the world.
However, many of them have invested in predictive maintenance to reduce unforeseen issues that could otherwise hinder production levels. Although the applications vary by client need, the approach typically involves using sensors on parts prone to breakage. Also, analytics suites give operations managers real-time statistics about performance and potential issues.
TVH — a Belgian company that manufacturers forklifts and aerial work platforms — services over 25,000 customers in 172 countries. It knew that problems with its industrial fleet could negatively affect its reputation and drive up costs. So, TVH began using IoT sensors to predict future faults before they happen. In addition to detecting problems, the technology locates the nearest service technician and maps out the best route for the person to reach the malfunctioning equipment.
TVH reports that predictive maintenance measures have allowed them to save up to 30 percent on maintenance costs. Also, their machines have higher percentages of total uptime.
3. Automation of Repetitive Tasks
Analysts believe there is strong evidence facilities will continue to see an increase in automation this year. Companies that can prove they have the labor necessary to accept huge contracts should find it more achievable than expected to meet client needs and remain competitive. Automation is particularly valuable for repetitive tasks because it avoids worker strain and mistakes as well as lack of uniformity.
In most cases, automation is not replacing human effort — it is supplementing it. Dynamic Group, a company that specializes in precision molds and injection-molded components, was having difficulty staffing its injection molding production needs and turned to robots for automation assistance. The project was for a medical device with heat-sensitive parts, which meant the cycle times for each part had to be consistent to generate the proper results. To meet its needs, the company depended on collaborative robots for three different production capacities and ended up tripling its production capacity despite reducing the size of the human labor force.
4. Data Visualization
Sometimes, industry managers know their processes have bottlenecks but aren’t sure how to resolve them. However, there are other instances where prolonged inefficiencies go unnoticed and have dramatic effects on productivity.
The Shimadzu Corporation, which manufactures physics and chemistry instruments in Japan, discovered that production line issues were both difficult to spot and challenging to resolve. To ease those known burdens, the company used a platform that gives it graphical representations of production line processes, enabling leadership personnel to monitor progress and highlight limitations.
After a six-month period of using the state-of-the-art data visualization platform, representatives from The Shimadzu Corporation reported a 320-hour reduction in production hours plus a 15 percent productivity boost. Additionally, the company mentioned its perspective of overall operations was much richer than before, allowing analysis of multiple factory components instead of single elements.
Some factory owners and other manufacturing professionals understandably hesitate at the prospect of adopting new technologies. However, the case studies above provide an abundance of solid evidence that 2018 is a fantastic year to make good on an intention to implement smart technologies. Once companies begin adding technologies on a limited basis, they should find it easier to scale up when needs dictate and budgets allow.
Kayla Matthews is an independent technology writer at Productivity Bytes.