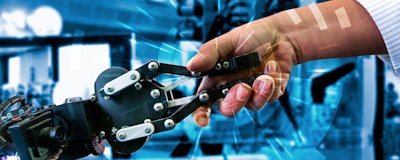
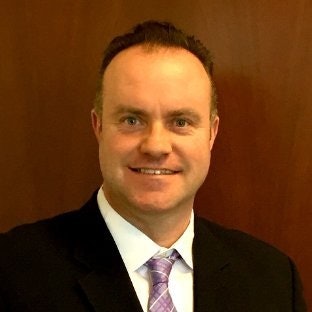
In a short amount of time, Industry 4.0 has gone from buzzword to reality. Manufacturers are embracing new technologies that reshape operations by digitizing processes across the value chain. New data and insights derived from sensors, advanced supply chain systems and mobile devices, channeled through IoT and cloud platforms will make companies far more profitable and deliver greater value to end users. And, there is no single area that this digital transformation will affect more than quality.
The digital transformation associated with Industry 4.0 seeks to put the customer first by leveraging data, autonomous feedback, predictive analytics, and AI to continuously improve the quality, safety and efficacy of products and services companies offer. But before companies can leverage these technologies to propel them into this new era of manufacturing, they must establish a framework that allows them to transition without a significant disruption in daily operations. With that in mind, here are five tips for companies looking to leverage Industry 4.0 technologies.
Tip #1: Consider Your Data Foundation
It is imperative that all aspects of master data are as complete and concise and ‘clean’ as possible. The source of that master data is also critical. Many organizations deploy systems and assume they can optimize their master data thereafter and this invariably turns out to be problematic. Many companies are building data lakes to support their Industry 4.0 initiatives but run the risk of simply filling their lake with muddied water.
Tip #2: Assess Current Needs and Set Goals
Many companies make the mistake of thinking that simply implementing Industry 4.0 technologies is all that is required to achieve success. To take advantage of disruptive technology, quality leaders should begin with a complete assessment of current state and the desired outcomes. By identifying potential roadblocks and opportunities, companies can strategically plan Industry 4.0 investments which will subsequently lead to better results. For example, manufacturers need to address whether the infrastructure systems currently in place are ready to support the path toward Industry 4.0 and its subsequent benefits.
Tip #3: Try Before You Buy
The level of hype that surrounds new and innovative technology can overwhelm even the most seasoned executives, causing many to jump too soon at every tool that promises the world. In today’s crowded market, coupled with the emergence of Industry 4.0, it’s important to test all products and solutions before committing, especially those with expensive price tags. Manufacturers need to keep in mind that it’s not the hype that’s important but the tangible solution it will provide. The key to this is identifying an area of the value chain that can deliver tangible value and targeting a pilot or proof of concept there.
Tip #4: Find and Retain the Right Talent
As new technologies are adopted within an organization, this will require finding and training the right talent to operate and manage these tools. From advanced robotics and sophisticated sensors to 3D printing, manufacturers will need to ensure that teams develop the right skill sets to succeed. So, it’s vital that companies attract and retain the best digital talent. Recruiters, for example, should looks beyond certificates and degrees. Instead, there should be a focus on key capabilities that are aligned with each company’s goals and future.
Additionally, selecting change agents to lead the digital transformation within a company will help make this process easier. Digital transitions, no matter how big or small, can impact a company’s ecosystem. Digital transformation is about strategy and culture as much as it is technology. Having a dedicated person or group to guide this process will alleviate any resistance to change and help problem solve potential challenges.
Tip #5: Plan for a flexible future
Along with short term goals, quality leaders should also consider how Industry 4.0 will impact and change the long-term future of a company. Creating a long-term road map and setting predefined targets will help quality leaders track business transformation and monitor for areas of improvement as new technologies are implemented and deployed.
Even with a plan in place, goals and visions for the future should not be written in stone. Quality leaders often walk a tightrope that flails precariously as companies launch into unexpected initiatives that can suddenly, and drastically change a company’s path. Just think of all the unknowns that come with launching new products, acquiring new companies, or partnering with unproven suppliers. Staying ahead of the competition during Industry 4.0 will require the flexibility to course correct and pivot.
Although Industry 4.0 is disrupting quality management and manufacturing as we know it, quality leaders should not be threatened. With well planned investments and a clear understanding of desired outcomes, they can seize on new opportunities that make their companies more profitable and consumers safer and more satisfied.
Stephen McCarthy is VP of Digital Innovation at Sparta Systems.