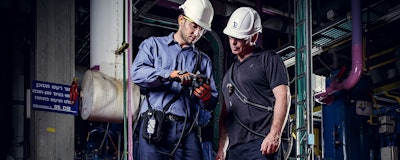

With the convergence of the Internet of Things (IoT) and comprehensive Predictive Maintenance (PdM) technologies, industrial plants and facilities can gain unprecedented insight into the health of critical machines — if the system is set up with the right data and metrics. With so many moving parts, that doesn’t necessarily come easily however.
Preventive maintenance alone leaves facilities vulnerable because it is based on scheduled best guesses of when a machine might need service. Despite best efforts, Original Equipment Manufacturers (OEMs) cannot fully replicate the systems and load under which their equipment operates in the field.
Predictive Maintenance Grows Up
Traditional thinking puts maintenance on a schedule, planning for wear and tear on a basis learned from other machines and past failures. This preventive maintenance mindset was the best practice for many years, but preventive maintenance does not account for the unexpected, for example a faulty part or technician error. Hiring maintenance crews and training them to care for facilities based on past performance are the best the paradigm can offer. Add to this the fact that the expense does not always pay off. Additionally, alert fatigue and false alarms can further degrade response times to real emergencies.
Modern PdM uses the same principle — learning from past uses — but it does it in real time with monitors that track vibrations and ultrasonic emissions that even the most skilled technician could not pick up. While PdM has been around for several years, it previously required a sizeable budget putting it out of reach for many companies.
Advances in PdM technologies, driven by reductions in cloud computing prices have changed this dynamic. Affordable and accurate mechanisms can now track the health of almost any equipment with moving parts. With new PdM technologies, sensors listen in ways that technicians can't. The health of machines and their many parts are now available on a technician’s mobile device.
Facts Versus Potential
Knowing about a machine’s current condition is inherently valuable. Parts and equipment can sometimes last much longer than scheduled and making use of their full lifespan saves money. Parts can also wear much faster than expected — making efficient use of a company’s working capital is the responsibility of any facility manager. CFOs would prefer that a facility manager order critical spares just-in-time as opposed to having them laying around.
Any post-mortem of equipment failure aims to prevent similar incidents in the future. It always comes down to having better data and knowing what that data means. Continuous monitoring through sensors placed on machines picks up exactly what is going on inside. This new PdM paradigm provides technicians with the most accurate facts possible rather than relying on the potential wear and tear addressed by preventive maintenance. Simply put, accurate repairs are made from holistic data.
Plug and Play, Almost
Applying PdM in facilities today requires little more than maintenance crews hooking up sensors to machinery. Connected through the Internet, these sensors relay data on ultrasonic emissions and vibrations to servers that analyze in real time and provide feedback right on a technician's mobile device. All the training and advanced skills once required are now condensed into a sensor, an Internet connection and a mobile device.
The facts gathered by this new wave of PdM sensors don't just get looked at by the technicians and assessed for that one machine. Machine data gets analyzed with advanced algorithms and compared to other machines to accurately judge the equipment's health. Better yet, the computers that do the analysis learn from every job so that each readings actually further advances the knowledge database of the whole system.
Not All PdM is Created Equal
Knowledge is power and advanced analysis of that knowledge is more powerful. Stepping away from a reliance on preventive maintenance alone and incorporating PdM allows facilities to ensure uptime and plan ahead for repairs thus shifting the nature of the conversation about comprehensive PdM in industrial plants and facilities.
Saar Yoskovitz is CEO and Co-Founder of Augury.