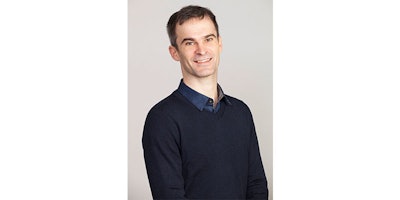
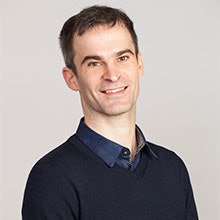
Big data analytics, IoT and cloud computing are all familiar buzzwords, and sooner than you think, each of these technologies will begin playing a significant role in reshaping the way you operate your manufacturing processes. These technologies are all under the Industry 4.0 umbrella.
According to Gartner, Industry 4.0 is a framework for addressing the digitalization of complex value chains and the efficient collaboration of businesses, IoT, technology providers and consumers. Industry 4.0 extends beyond the digitization of physical assets with the vision of a digitally enabled industrial economy integrating business processes and data across multiple supply chains and value chain participants.
Data analytics, IoT and the cloud are platform technologies for the fourth industrial revolution, providing manufacturers a path to smarter practices. In turn, these smarter processes deliver the necessary intelligence and visibility food manufacturers need to optimize operational efficiency.
Intelligence When the Stakes are High
Industry 4.0 ultimately equips food manufacturers with the right information, at the right time, to the right people. Peer-to-peer wireless connections mean more data can be captured without the overhead of having to wire in sensors and disrupt the manufacturing operation, leading to a higher degree of connectivity between the automation level and the manufacturing execution system (MES). All areas of the shop floor can be included, even areas that may have been deemed less important or too difficult to get connectivity, and that means higher visibility at little additional cost — a clear line of sight into the entire production floor.
For process and discrete manufacturers in the food and beverage arena, this fast and seamless exchange of information is a game-changer. Take a scenario where there is no room for error, like a food contamination recall. A factory that has digitized its manufacturing processes and is operating at an Industry 4.0-level can track and trace products in real-time, removing them from shelves quickly and minimizing risks to consumers.
Integrating your MES with other business systems is key to true digital transformation and efficiency on the factory floor. Food and beverage manufacturers can achieve a more holistic view by taking advantage of an integrated suite including Enterprise Resource Planning (ERP) and Enterprise Asset Management (EAM). ERP dictates, MES executes and EAM ensures reliability and uptime. Manufacturers seeking to improve their production performance using the technologies available today — particularly IoT and access to machine data — should seek comprehensive solutions that provide:
- Production planning and scheduling, and materials management (ERP functionality)
- Maintenance reliability and operational insight into maintenance activities, so that potential disruptions to production can be avoided (EAM functionality)
- Machine intelligence and analysis of data to drive continuous improvement (MES functionality)
With these systems connected, you can access critical business information in real-time and start to paint a clearer picture of your manufacturing operations.
Smart Manufacturing Still Has Roadblocks to Overcome
While most food manufacturers realize the need and potential for adopting Industry 4.0 practices and technologies, the difference between wanting to change and making the change are vast. A McKinsey survey indicated only 48 percent of manufacturers considered themselves ready for Industry 4.0.
The greatest barrier to adoption, especially for food manufacturers, is the perceived cost and time migrating from legacy systems and digitizing paper-based manual processes would take. Many food manufacturers still do not have reliable, real-time manufacturing metrics, let alone track and trace capabilities.
However, in the long run, status quo technologies can cost these manufacturers more than investing and implementing advanced technology. The rise of Industry 4.0 stems from the growing demands placed on manufacturers to become more agile and accountable to their customers.
Accessing information quickly and with little disruption through Industry 4.0 technologies, enables manufacturers to drive improvement and compliance, and better meet their organizations’ targets.
And adoption truly pays. According to a Forbes report on Price Waterhouse Cooper’s Industry 4.0: Building the Digital Enterprise study, 35 percent of companies adopting Industry 4.0 expect revenue gains of more than 20 percent over the next five years.
Looking Ahead
If manufacturers use Industry 4.0 to its full potential, they will be able to enhance collaboration outside their plants and involve the wider supply chain — from raw material suppliers right through to distribution centers — to streamline operations.
Ultimately, food manufacturing is on the precipice of change and as the gravitation toward data, automation and other facets of Industry 4.0 grow, it will become imperative that manufacturers adapt and embrace the innovation.
James Wood is Director of Factory MES & Activplant Product Lines for Aptean