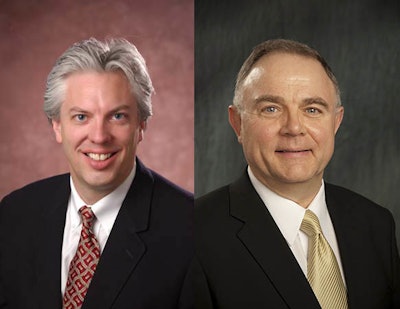
Around the globe, intelligent and pervasive industrial automation has been catapulted in recent years to a top national or regional priority. Known by different names, e.g., “Advanced Manufacturing”, “Smart Manufacturing”, “Industry 4.0” or “Factories of the Future” to highlight a few, these initiatives all bear the same characteristics, i.e., transforming the manufacturing process from a patchwork of isolated silos to a nimble and seamless whole fully integrated with the downstream and upstream production environment.
There is, in fact, a close link between modern manufacturing and the advent of the Internet of Things.
The European Union as a Benchmark
The Factories of the Future (FoF) multi-annual roadmap for the years 2014-2020 under Horizon 2020, the European Union (EU) Framework Program for Research and Innovation, sets a vision that echoes similar projects worldwide. In particular, it “outlines routes towards high added value manufacturing technologies for the factories of the future, which will be clean, highly performing, environmental friendly and socially sustainable.” The EU FoF roadmap sums it up clearly: the factory of the future will be lean, agile and totally integrated.
However, this evolution will not take place in a vacuum. Thanks to the timely convergence of technological, regulatory and societal trends, the communications space is progressively absorbing a new class of denizens, i.e., “things” of all forms and purposes, which are central to what is now being dubbed the “Internet of Things or IoT”.
The Internet of Things as a Catalyst and Purpose
The Internet of Things, following the definition of the International Telecommunication Union, is “a global infrastructure for the information society, enabling advanced services by interconnecting (physical and virtual) things based on, existing and evolving, interoperable information and communication technologies.” It is in the process of being brought to life by many enabling technologies (sensors and actuators, [wireless and wired] networks, [high performance] computing, energy harvesting and storage, encryption [cybersecurity], modeling & simulation, software analytics, etc.). The IoT-related technologies will be accelerating the arrival of the Factory of the Future.
These technologies, when combined together into a system, are best described as “Cyber-Physical Systems (CPS)”. According to the US National Science Foundation (NSF), “Cyber-physical systems (CPS) are engineered systems that are built from, and depend upon, the seamless integration of computational algorithms and physical components. Advances in CPS will enable capability, adaptability, scalability, resiliency, safety, security, and usability that will far exceed the simple embedded systems of today.”
Fraunhofer, Europe’s largest application-oriented research organization, made the connection between the “factory of the future”, CPS and IoT while exhibiting their “factory of the future” concept at the last Hannover Messe in April 2014: “The industry needs new solutions for cost-efficient production processes that also preserve resources. The "Integrated Industry" sector has, thus, been in the focus of many research activities at Fraunhofer for some time. Cyber-physical systems link the virtual world to objects of the real world. This creates the "Internet of things" where real products and production processes are linked to the Internet. This accelerates processes and helps to better utilize resources.”
Therefore, the Internet of Things will be at the same time a catalyst as well as a goal of the industrial automation currently underway.
Critical Facets of the Factories of the Future
Future factories will be shaped by the Internet of Things. As this evolution unfolds, several critical features and challenges will emerge such as the ones presented below, which do not necessarily make up an exhaustive list:
Lesser importance of location
Thanks to the immersion of IoT technologies, some functions that are integral to manufacturing need no longer to be co-located while some can be controlled and monitored from faraway places. This is the case for example with additive manufacturing or 3D printing, as it is often called, which allows decoupling of design and prototyping.
Non-vanishing impact of the human factor
Paradoxically, increased automation requires additional manpower, modifying the nature of the demand for labor, e.g., growing requirements for information technology proficiency.
Need for new business models
With the rise of platforms and overwhelming software content (see “That thing looks like hardware, but it’s software now - Building great software on time is at the heart of more and more "hardware" projects, “ by Jim Stogdill at O’Reilly Radar – March 25, 2014), manufacturers will increasingly partner with other suppliers that have a different set of skills and expertise, calling for a rejuvenation of their business model (from a one-time hardware sale to ongoing service as a result of two converging trends, i.e., product “servitization” and software-as-a service.)
Environment-friendly mandates for production and products
IoT technologies will provide the tools to optimize the energy consumption and limit the emission of pollutants. Also, tracking solutions embedded in newly manufactured products, relying on Location-Based Services (LBS), will help lessen the damaging consequences on the environment of e-waste.
Role of standards and international collaboration
IoT Standards should facilitate industrial automation. There are many initiatives (too many to list here), in the IoT standardization arena currently underway. Of special interest to the manufacturing industry given the crucial role of timing and synchronization, in June 2014, the U.S. National Science Foundation (NSF) announced its support of a CPS-centered research project (“RoseLine”), which is “to develop new clocking technologies, synchronization protocols, operating system methods, as well as control and sensing algorithms.” The NSF press release indicates that this research activity is “to improve the accuracy, efficiency, robustness and security with which computers maintain knowledge of time and synchronize it with other networked devices in the emerging "Internet of Things" (June 13, 2014).”
Beyond interoperability and application, standards will be needed at the product level. This is not lost on many product-focused groups such as IPC (a.k.a. “the Association Connecting the Electronics Industries”, a not-for-profit trade association and standards-developing organization, which represents all facets of the electronics industry, including design, printed board manufacturing, electronics assembly and test).
For instance, the program of the IPC TechSummit in October 28-29, 2014 makes room for the Internet of Things. In particular, one of the keynote sessions will examine “the packaging building blocks and emerging technologies required to enable the Internet of Things,” while another one will review key market and industry structural changes that are reshaping the supply chain such as “the emerging "Internet of Things", [which] will also drive significant volumes of low-cost wireless modules and sensors that adapt technologies spawned initially within the mobile and automotive sectors.”
Regarding the need for international cooperation in this area, let’s note a recent initiative (i.e., the Coalition for the Advancement of MicroElectronic Systems Technology (CAMEST)), which is dedicated to the identification and dissemination of the critical technology application knowledge needed for the further development of the electronics industry. This new group identifies gaps in design, manufacturing, test and reliability across all aspects of electronic component assembly and subsystem manufacturing from semiconductor to final assembly. It is an independent organization aimed at fostering collaboration among the global electronics industry, academia, and government. It arose from the efforts of JISSO North America (JNAC), which serves as a forum for members to share information. The Japanese term jisso, for which there is no English word, is not an abbreviation; it evokes the idea of total solutions.
The Pivotal Role of Manufacturing in the Realization of the Internet of Things
In his recent book on IoT architecture, Rethinking the Internet of Things, Francis daCosta summarizes well the impact of IoT technologies on factories: “With the increasing automation of the factory floor, the autonomous or semiautonomous lower–level control and feedback loops made possible through distributed intelligence within the Internet of Things may allow for higher production and better use of human resources. If integrator functions can handle lower-level adjustments and controls of operating machinery, human eyes and minds may be freed for longer-term analysis and optimization, based on exception and historical data collected at a higher level. (p. 135).” What Siemens calls “Totally Integrated Automation or TIA” represents, for all intents and purposes, the ultimate outcome of the IoT insertion in the manufacturing process.
However, factories of the future will not only be molded by IoT technologies but also become an essential building block of the Internet of Things.
Smart Manufacturing is but one facet of the intricate relationship between IoT and the production process. GTMI Executive Director Dr. Ben Wang succinctly and compellingly underscores this fundamental two-way connection: “Smart Manufacturing and Manufacturing Smart are two symbiotic emerging trends that are central to both the radical transformation of the entire manufacturing industry and the development of the Internet of Things.”
Indeed, manufacturing will be expected in a not-too-distant future to incorporate “intelligence readiness” in all products as society will progressively be relying on an IoT-supported infrastructure. This is true both in the Business-to-Consumer (B2C) and Business-to-Business (B2B) markets. In this regard, it's worth noting that Internet of Things technologies are one of the Physical Internet (Pi, π) key pillars. The Physical Internet is a groundbreaking, comprehensive logistics system that aims at optimizing the way physical objects are transported, handled, stored, realized, supplied and used throughout the world. As Dr. Benoit Montreuil who has conceived and developed this innovative concept explains: “the Physical Internet is to exploit as best as possible the Internet of Things to enable the ubiquitous connectivity of its π-containers and π-systems.”
“Manufacturing Smart” is a non-trivial challenge since building the Internet of Things straddles a wide range of disciplines. Adrian McEwen and Hakim Cassimally in their must-read guide on Designing the Internet of Things eloquently make this very point: “The Internet of Things is, or should be, the “Internet of Beautiful Things”, and every object, as well as being a crafted, designed, and engineered object, is, or could be, the work of an artist also. Of course, it is a rare Renaissance individual who covers all these disciplines with the fluency and ease that are conducive to creating a truly successful product (p. 19).” As a result, priority will have to be given to the education and training of the future and current industrial workforce that support and effectively foster the IoT-led manufacturing transformation.
About the authors
Andrew Dugenske is the Director of the Factory Information Systems (FIS) Laboratory at the Georgia Institute of Technology (“Georgia Tech”) Manufacturing Institute (GTMI). He is also founder and C.E.O. of Factory Right LLC, a software company that provides information technology solutions to manufacturing enterprises and was co-founder and president of Great Technological Collaborations Inc. He is a member of the National Electronics Manufacturing Initiative (NEMI) FIS working and implementation groups, the NEMI road mapping team, several IPC technical committees, the JISSO International Council and the joint NEMI-IPC CAMX standardization committees.
Alain Louchez is the Managing Director of the Center for the Development and Application of Internet of Things Technologies (CDAIT) at Georgia Tech. He chaired the Telecommunication Union (ITU) conference, on “Internet of Things: Trends and challenges in standardization” held in Geneva at the ITU headquarters in Geneva, Switzerland, on February 18, 2014, and will be chairing the IoT standards session at the Second Annual Internet of Things Global Summit to be held in in Washington, DC, USA, on October 27-28, 2014.