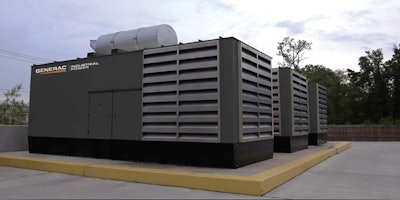
white paper
Medium Voltage
On-Site Generation
Overview
by
Mike Kirchner, Technical
Support Manager
at Generac Power Systems
INTRODUCTION
It seems that just about everyone is looking for more power. As our dependency on electricity continues
to grow, so does the need to design larger back-up generation systems.
The transition from low voltage to medium voltage on-site generation is influenced by a mix of
economic and system design considerations including: cabling distance, bus capacity, fault current
capacity, switchgear cost, genset cost, and utility interconnection and integration configurations.
Our goal is to help build a common level of understanding around components and system design
considerations that readers can build upon when working with medium voltage projects.
2WHAT CONSTITUTES MEDIUM VOLTAGE
Depending on your perspective and what standards are being
referenced, the definitions of low, medium and high voltage can vary
significantly. NEC definitions and perspectives are different from ANSI/
IEEE.
• NEC (systems)
o 0-49 - Low Distribution is covered by 250.20(A)
o 50-1000 - Medium Distribution is covered by
250.20(B)
o 1000-4160 - High Distribution and 4160 & up
o Transmissions are covered by 250.20(C)
• ANSI/IEEE (1kV - 35 kV)
• IEEE Std 1623-2004 (1 kV - 35 kV)
• NECA/NEMA 600-2003
o Medium voltage cables rated from 601 volts
to 69,000 volts AC
From a practical standpoint of power distribution, low voltage is
considered ≤ 600 volts, placing medium voltage greater than 600
volts. One of the more common electric machine voltages tends to be
4160 volts. This voltage starts becoming very prevalent in industrial
environments when motor horsepower starts exceeding five hundred. It
is not uncommon to find medium voltage motors ranging from 2400 to
6900 volts. Some of the classical definitions of medium voltage extend
to 35 or even 69 kV. This operational range of the category makes
sense from a utility / transformer perspective but not necessarily from
an onsite generator perspective.
It is common for alternator manufacturers to reference alternators in
the 5 kV class (2400, 4160, 6900) as medium voltage and alternators
in the 15 kV (12.47, 13.2 and 13.8 kV) class as high voltage – though
from the broader sense they both are in the medium voltage category.
WHEN TO CONSIDER MEDIUM VOLTAGE
There are a number of factors to consider when determining whether to
transition from low voltage to medium voltage:
• Bus capacity
• Fault current
• Physical location of loads
• Cost
• Redundancy
Bus Capacity
Standard bus configurations typically extend to 6,000 amps. Larger
busses can be specially engineered though the costs tend to spiral.
Fortunately, on-site generation can extend this bus capacity by double
ending – bringing generator capacity in from each end and placing the
distribution feeder breakers in the middle. This functionally increases this
bus limit to 12,000 amps.
Fault Current
The other limit that tends to appear around the same point is the fault
current rating of the paralleling and distribution gear. Once the system fault
current exceeds 100 kA, the costs to move to 150 or 200 kA breakers and
gear may be economically limiting. Assuming an alternator subtransient
reactance of 12%, the 100 kA limit occurs at the same 12,000 amps as
the bus limit.
• 65 kA, 100 kA
• Rated Amps / x”d = Isc
• 12,000 / .12 = 100,000 amps
For 480 volt equipment, these limits are converging at 8,000 kW. This
tends to be the strong transition point to move to medium voltage or split
the low voltage generator bus into two separate systems.
Physical Location
When an application has loads that are physically located far apart, the
cost of the low voltage cabling becomes a significant constraint. For
Double Ended Bus
Medium Voltage Switchgear with PT & CPT Compartments
Diagram Complements of Pioneer Power Solutions
3campus environment projects with an incoming medium voltage utility
service, it is often desirable to consider moving to a medium voltage
“power plant” configuration. In this configuration, the entire campus
can be backed up with a single medium voltage transfer pair. With this
approach, a medium voltage power plant can provide redundant parallel
generation capacity to all the step down transformers on the campus
This approach needs to be compared and contrasted with tying in
multiple generators around the campus on the low voltage sides of the
transformers. Historically, this approach was more common when the
low voltage loads didn’t require the reliability of redundant generation.
This approach also provides more choice in which loads would
receive back-up power and which would be excluded. With various
manufacturers offering integrated paralleling generator options, the low
voltage tie-in approach is being considered on more mission critical
applications. Pods of low voltage, paralleled generators also offer the
advantage of providing protection from a failure of the utility step down
transformers.
Costs
Cost is another key factor in the decision to transition to medium
voltage. Within the market, transitioning a 480 V, 2 MW generator into
a 15 kV unit will likely add $100,000 to the overall costs, while making
the same transition to 4160 V will only add $40,000.
These added genset costs need to be compared to the cost of installing
a pad mounted transformer at each generator. At 4160 V, the medium
voltage alternator configuration is fairly common because the costs are
similar. At 15 kV, many system designers will look at implementing a
step up transformer configuration to achieve some cost savings.
Also when implementing medium voltage solutions, it is not uncommon
for utility services to be 23 kV. This voltage will require on-site generators
to be transformed -- the highest nominal alternator voltage typically is
13.8 kV. When looking at transformer based solutions, considering 600
V generators may offer some cost savings by reducing ampacity on the
low voltage side.
Another area of significant cost is the medium voltage metal clad
switchgear (ANSI/IEEE C37.20.2) necessary for paralleling medium
voltage generators or creating transfer pairs with the serving utility.
This equipment with its associated vacuum breakers, protective relays
and instrument transformers typically costs $50,000 to $60,000 per
section while a typical section only contains a single breaker. When
comparing to low voltage solutions, transfer and paralleling equipment
is generally twice the cost.
Redundancy
The options mentioned above do provide cost-effective alternatives to
medium voltage applications; however, they do not provide redundancy
for a failed transformer. As a result, these approaches may not provide
the best solution, since many organizations and companies consider the
generator system to be mission critical and that factor tends to override
the potential cost savings.
MEDIUM VOLTAGE ALTERNATORS
While medium voltage alternators are conceptually the same as
low voltage alternators, they differ in the construction relative to the
alternator’s armature (main stator). In low voltage alternators, the main
stator is typically a random wound machine. This construction uses
standard electric machine, insulated copper windings. The construction
is called random wound because the wires within the stators slots and on
the end turns can randomly lay next to another wire that is many turns
further down in the phase coil. This isn’t an issue because the insulation
is easily rated for the maximum voltage potential.
In medium voltage alternators, many more coil turns are used in the main
stator which keeps increasing the voltage with each turn. The resulting
voltage potential would be greater than an individual wire’s insulation
could withstand if randomly wound. For this reason, the construction is
converted to form coil.
The round wire is now replaced
with square wire and the wire
is precision wrapped to allow
the wire to only touch the coil
turn above and below it. This
controls the voltage potential
between turns. The coil is then
wrapped with special varnish
Switchgear
Medium Voltage Form Coil Alternator
Picture Complements of Marathon Electric
4compatible insulating tape to insulate the high potential coil winding
from the ground potential of the stator core.
As a rule of thumb, one wrap of tape is needed for each 1000 volts.
That is part of the reason why the 15 kV class alternators cost so much
more than 5 kV models. The entire stator assembly is varnished using
a vacuum pressure impregnation (VPI) process. This process removes
the air entrained in the insulating tape and then pressurizes the varnish
into the tape. This varnish process is a must for form coil construction
but offers few advantages when applied to low voltage random wound
alternators that don’t utilize insulating tape.
Medium voltage (5 kV and 15 kV class) alternators are typically only
available in certain kW ranges. Alternators in the 5 kV class are
available as small as 500 kW but are typically implemented ≥ 1000 kW.
Alternators in the 15 kV class aren’t typically available below 1000 kW
with the standard implementation ≥ 2000 kW.
Both classes usually come standard with winding resistive thermal
devices (RTDs). RTDs provide a method of monitoring the alternator and
protecting it against heating effects due to restricted air flow, phase
imbalance or harmonics. However, RTDs operate too slowly to be used
to provide short circuit protection.
Bearing RTDs are also typically implemented on 15 kV class machines
to allow pre-emptive shutdown. Due to the target market and physical
size of the insulation, 15 kV alternators are typically implemented in
large frames (1000 mm stator laminations). This larger frame causes the
alternators rotor weight to become too heavy for the engine’s rear bearing.
As a result, many 15 kV alternators are implemented in a two bearing
closed coupled configuration. The second bearing carries the rotor weight
and the closed coupling creates easy alignment to the engine flywheel
housing.
Medium voltage alternators are configured for bus bar cabling with the
switching and protection located within the metal clad switchgear. The
genset will include potential transformers (PTs) that step down the main
output voltage to typically 120 volts for instrumentation and control. The
genset needs this PT input for the voltage regulator control of the alternator
voltage and over/under voltage protection within the genset controller.
PROTECTION SYSTEMS
The generator will also include current transformers (CTs) for monitoring
and for overcurrent protection. The CTs are also used to calculate kW,
KVAR, and kVA. This information is used for monitoring, protection,
and control in the case of on-generator synchronizing and load share
functionality.
Current transformers are also often utilized on the neutral side of the
alternator phase coils to provide a zone of protection – differential (87)
protection – which is implemented by a protective relay located in the
switchgear.
This function monitors the current flow between two CTs located at
different points within a current path. If the current isn’t the same, the
path has faulted. This is typically implemented from the high side of the
vacuum breaker in the gear to the low side of the alternator resulting in an
Medium Voltage Form Coil Alternator
Picture Complements of Marathon Electric
Medium Voltage Protection and Neutral Grounding Resistor
Diagram Complements of Pioneer Power Solutions
5extremely high level of protection for all equipment between the two CTs.
Medium voltage systems are configured for 3 wire operation (no line to
neutral loads). As a result, it is common to use low resistance grounding
and then monitor for ground faults with a CT at the resistive bond. This
grounding method is typical for 15 kV systems and also used on some 5
kV systems. The grounding resistor is typically sized to limit ground fault
current in the 100 to 400 amp range. The resistor is sized by dividing
the line to neutral voltage by the desired maximum ground fault current.
The protective relaying is commonly set at 10% of the maximum ground
fault current. This is done to protect the grounding resistor against the
maximum continuous non-tripped ground fault. It is common to set the
protective relaying to trip in 10 to 30 seconds.
For 5 kV systems, it is possible to use high resistance grounding when the
ground fault current is limited to 8 amps. Above this level it is likely that
the fault will escalate into a line to line fault. Systems operating in the 15
kV class typically have considerably higher capacitive charging currents
which cause the ground fault currents to easily exceed the 8 amps. For
this reason, high resistance grounding is not recommended.
Protective relaying is a significant part of medium voltage systems. Since
the vacuum breakers don’t utilize integrated over-current trip units, over-
current protection is implemented via multi-function protective relay
Given the capabilities of today’s multi-function protective relays, it only
makes sense to incorporate various functions: differential (87), synch
check (25), overcurrent (50/51), over/under voltage (27 /47), over/under
frequency 81OU, and ground fault (51N). For applications that utilize a low
voltage generator coupled to a step-up transformer, it may be desirable to
incorporate transformer differential protection (87T) to protect the entire
zone between the high side of the vacuum breaker to the low side of the
low voltage generator. This function tends to be fairly specialized and may
require an additional protective relay. For detailed design information on
grounding and protection, consult the IEEE color book series.
All medium voltage systems require medium voltage metal clad switchgear
(ANSI/IEEE C37.20.2) to tie everything together. A typical medium voltage
metal clad switchgear lineup will utilize medium voltage vacuum breakers
along with the associated protective relaying. It will contain potential
transformers (PTs) for stepping down the medium voltage to typically 120
VAC for monitoring and protection. It will also typically contain control
power transforms (CPTs) for powering the recharging motor within the
vacuum breakers. Together the PTs and CPTs consume the entire upper
section above the vacuum breaker.
One strategy to compress the switchgear line-up and reduce cost is to
switch the generators breakers to DC close and recharge functionality and
use the PTs located on the generators for sensing. This will free up the
upper section for another generator breaker. This approach functionally
combines two side by side sections into a single dual breaker stacked
configuration.
Finally, it is fairly common for metal clad switchgear line-ups to incorporate
lightning arrestors and surge capacitors for large generator systems,
especially when incorporating 15 kV alternators. The use of these items
on the utility source depends on the system topology.
LIGHTNING/SURGE ARRESTORS
AND SURGE CAPACITORS
Lightning/surge arrestors limit the severity of a voltage surge to prevent
damage of insulation of MV motors, generators and transformers. In its
simplest form, it could be a spark gap. A typical surge arrestor features
silicon carbide (SiC) discs in series with a small spark gap. When the
voltage becomes too high, the spark gap will flash over and the SiC discs
will conduct.
The best protection solution is to use surge arresters together with the
surge capacitors. Surge capacitors pick-up where lightning arrestors leave
off and manage daily surges and transients. They are always connected to
the system and limit the rate the voltage and rise to a few amps. They are
typically paired with surge arrestors.
CABLING
Medium voltage cable is specialized as the insulation system must
maintain its dielectric strength and provide multiple layers of protection.
This cabling also uses stress cones which:
• Transitions voltage potential from wire to insulation
• Keeps the insulation from breaking down
LOW VOLTAGE / MEDIUM VOLTAGE
COMBO APPLICATIONS
To help reduce costs, some designs might benefit from a combination
low voltage / high voltage strategy. Instead of using medium voltage
alternators and paralleling with medium voltage gear, it may be possible to
configure a system in which the paralleling occurs on the low voltage side
of step-up transformers. This configuration could be implemented with
single or multiple transformer configurations.
6An effective alternative choice for a medium voltage application below
2 MW is to implement on-generator low voltage paralleling functionality
terminating at the low voltage side of a step-up transformer.
For medium voltage applications below 6-8 MW, using multiple step-up
transformers with the medium voltage sides terminated together at the
gear also creates on effective alternative. In this second configuration, the
generators see gen-bus voltage on the low voltage side of the transformer
allowing for on-generator low voltage paralleling.
SAFETY REMINDER
Be sure any technician that works on a medium voltage system is qualified
to do so. Accessing the medium voltage bus can be dangerous and thus
requires very specialized equipment and knowledge. While there is always
tremendous pressure to complete projects within tight timeframes, it’s far
more important to be sure everyone is safe.
SUMMARY
Medium voltage applications can be found in data centers, pulp and paper,
plastics and petrochemical industries, heavy manufacturing, and campus
environments where loads are physically located far apart. Medium voltage
often provides an excellent alternative to overcome low voltage constraints
such as cabling costs, fault current and bus ampacity limitations.
DISCLAIMER
This information is provided as a service and does not constitute
recommendations regarding products for specific applications and should
not be relied on as such.
For more information about the material contained in this white paper,
or to learn more about the full line of Generac Industrial and Commercial
Generators, contact Generac at 1-888-GENERAC (1-888-436-3722) or
visit us at Generac.com to find your local dealer.
7NOTES
80L1018 Printed in USA Rev. A 11/2014
©2014 Generac Power Systems, Inc. All rights reserved.
Generac Power Systems, Inc.
S45 W29290 Hwy. 59
Waukesha, WI 53189
1-888-GENERAC (1-888-436-3722)
generac.com
NOTES