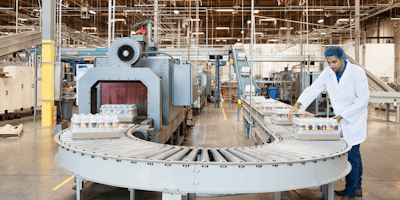
CASE STUDY
F&B PLANT IMPROVES COMMUNICATION TO
BOOST OVERALL EQUIPMENT EFFECTIVENESS
(855) 462-5630
PerformanceSolutionsbyMilliken.com
920 Milliken Rd
Spartanburg, SC 29303
The plant runs four distinct lines, each
dedicated to a different type of snack. But
as is common within F&B plants, one type
of snack is produced in a variety of flavors,
adding substantial complexity. A line
must accommodate different toppings
— salt, sesame seeds, spices, etc. — each
of which requires cleaning of machines
and periodic full sanitation (government
regulations). Some ingredients demand
even more care during changeovers.
For example, a pretzel line includes a
peanut-butter coating, which, due to nut
allergens, requires a “clean-lab” operation
to ensure that peanut particles do not
escape the machine’s operation area.
Performance Solutions was tasked
with improving overall efficiency and
throughput of snack lines (i.e., higher
output without more equipment or
labor). As is common with a Performance
Solutions engagement, a “model” line
was selected to trial and perfect best
practices — the pillars of the Milliken
Performance System (MPS) — in order to
dramatically improve its performance.
This line then serves as a model for the
rest of the facility.
On this U-shaped model line, different
flavor components empty onto the base
product (e.g., pretzels) along a conveyor
line; the conveyor shakes the product to
evenly distribute ingredients. Once flavors
are applied, the product enters a hopper
system, in which the snack is bagged,
weighed, sealed, and then transferred
to a packaging operation where bags
are boxed. A significant problem on the
line was underfilling of bags, often due
to misalignment. Misaligned bags create
spillage and rework (more product
needed to be added) and/or the line
would be stopped to correct alignment,
limiting output. At the start of the
Performance Solutions engagement,
the baseline performance for the model
line was 44.6 percent overall equipment
effectiveness (OEE), a measure that
combines throughput and efficiency.
PERFORMANCE-IMPROVEMENT OPPORTUNITY
In the initial assessment of the plant,
Rush identified communication as a
major issue. The plant ran four 12-hour
shifts, and frontline associates on one
shift never saw colleagues on other shifts.
Problems or improvement opportunities
identified on one shift were never relayed
to other shifts; it was as if four separate
teams ran their own operations on the
same equipment. All communication and
decision-making power was controlled by
a small management staff — limiting the
engagement and problem-solving ability
of frontline workers.
“One of the things we did during
implementation,” says Rush, “was to
install a visual management system
with communication boards, so you
could walk from area to area and quickly
see how machines were running. We
also developed a shift-handoff meeting
WORKING WITH PERFORMANCE SOLUTIONS PRACTITIONERS
Most food and beverage (F&B) plants run a diverse mix of
products based on changing consumer tastes. This can
create quality and machine problems, even for plants with
standardized processes and well-trained managers, operators,
and maintenance staff. Performance Solutions by Milliken offers
F&B companies and their plants the means to cope with change
while improving performance.
CLIENT
A global, multibillion-dollar F&B company invited
Performance Solutions to improve dozens of its
facilities. Mark Rush, a Performance Solutions
practitioner, helped to implement the Milliken
Performance System (MPS) at a 200-employee plant
that produces a wide array of snacks.
F&B PLANT IMPROVES COMMUNICATION TO
BOOST OVERALL EQUIPMENT EFFECTIVENESS
Changes to line processes and improved
communication rapidly translated in
greater stability for the model snack line.
In just over a year, OEE improved from
44.6 percent to 90.9 percent. Explains
Rush: “Because the plant’s efficiency
improved so much, management was
able to reassign an employee whose
entire job had been to ensure that there
were bags under every filling function.
POWERFUL IMPROVEMENTS
owned by the operators themselves. The
meetings brought incoming operators
up to speed on what occurred during the
previous shift, and helped in scheduling
production over the next shift.” These
changes kept all shifts focused on the
MPS planned maintenance pillar and
daily team maintenance pillar; the latter
assigns frontline staff to routine activities,
such as cleaning and monitoring
equipment for problems and minor stops.
Communication also focused frontline
employees on “centerlines” of criteria
related to line efficiency (i.e., the “sweet
spot” for optimum performance).
These included guidelines for machine
tolerances (e.g., duration of operation)
and factors that can impact product
quality and consistency (e.g., quality and
texture of incoming ingredients, humidity
in the plant). The communication boards
informed operators of variations from a
centerline.
“Once the line was operating within the
centerlines and confirmed with visual
controls,” says Rush, “any variation would
trigger problem solving and root-cause
analysis to determine why it occurred.”
Variations could result from operator
decisions (e.g., a need to accelerate
line speed based on management or
customer request); machine problems
(e.g., missing bags); or ingredient issues
(e.g., a new ingredient slowing operations
in an unexpected manner). This focus
on centerlines significantly reduced
the amount of contamination due to
overfilled product bags, as workers fine-
tuned the filling process and also applied
shielding to minimize product falling to
the floor (therefore becoming unusable,
and requiring cleanup).
At the end of Rush’s two-year
involvement with this plant, MPS
was sustained in the model area, and
replication underway for 50 percent
of the facility’s A-ranked lines and
equipment. Once those areas are
transformed, changes are then applied
by plant staff to the remainder of the
A-ranked lines and equipment. The
presence and role of Performance
Solution practitioners decreases as
replication spreads.
FUTURE SUCCESS
Phil McIntyre / Managing Director,
Business Development & Marketing
Performance Solutions by Milliken
(864) 503-1359
[email protected]
Mark Rush / Practitioner
Performance Solutions by Milliken
(864) 646-4721
[email protected]
KEY CONTACTS
PUT PERFORMANCE SOLUTIONS TO WORK FOR YOU
Performance Solutions by Milliken® works side by side with companies interested in strengthening and improving their
operations. The strategic approach that made Milliken one of the safest, most efficient manufacturers in the world is
the backbone of the consulting and educational services that Performance Solutions offers worldwide. Performance
Solutions by Milliken practitioners are serving over 350 operations, in 23 countries, and covering a wide variety of
industries.
Visit www.PerformanceSolutionsByMilliken.com to learn more about Performance Solutions’ consulting and
education services.