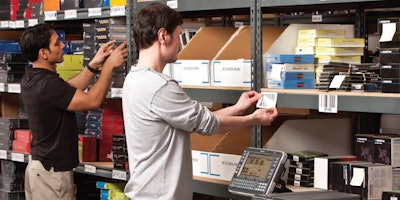
Raco Industries
How to Error-Proof the
Labeling Process
Labeling errors are a costly problem. At face value, incorrectly printing a roll of thermal transfer
labels equals about $10 to $20 in wasted media plus the cost of the ribbon, wear on the printhead,
and the labor used to print — and reprint — the labels.
But labeling errors can cost your business more than just the sticker price of printing supplies and
additional labor. Not meeting the requirements of compliance labeling regulations can result in
fines and penalties, and labeling errors that play a role in accidents or product recalls can put a
company in the media spotlight, causing damage to a company’s reputation that can be difficult to
overcome. A $10 to $20 roll of incorrectly printed labels can suddenly mean a loss of thousands of
dollars for your company.
A business also could incur penalties for labeling errors from enterprise and industry customers.
The auto industry, for example, levies fines and quality demerits for labeling noncompliance.
And if labeling errors result in returns, downtime, product recalls, or unnecessary costs for your
customers, they will suspend you from bidding on new business and may even find a new supplier
or manufacturer.
Fortunately, there are steps you can take to minimize — and even eliminate — errors through using
the right tools and implementing the right label printing processes.
How to Error-Proof the Labeling Process
2
For many manufacturing and supply chain applications, having the right label printing tools starts
with rugged printer hardware. Rugged devices are designed and constructed to withstand harsh
industrial environments — like the wash down areas of a produce grower’s operation or the floor of
a manufacturing plant. These types of applications require a printer that is built to resist damage
from water, dirt, dust, and chemicals and to keep performing regardless of temperature extremes or
shocks from drops or tumbles.
It’s also important to select a printer that can be used
where it’s needed, rather than one that’s tethered
to a workstation in a back room, which requires
unnecessary, time-consuming steps between
where labels are printed and where they are
used — and creates an opportunity for the
wrong labels to be picked up and applied.
Rugged printers with small footprints
may be the solution for areas with limited
counter or workspace, and mobile printers
enable employees to print labels anywhere
they are working throughout the facility, on
the dock, or even in the field.
Smart printers that use machine-to-machine
(M2M) technology are a fool-proof way to
eliminate labeling errors. Smart printers can be
integrated directly into a manufacturing line or other
process: Using onboard TWPLC Printer or TWSmart Pack
software, smart printers receive digital input from devices such
as scales, portable or fixed scanners, RFID readers, or manufacturing equipment. Smart printers
provide a way to automate label printing and offer users the added benefit of eliminating a PC from
the process — which also eliminates the need for OS upgrades and patches, PC maintenance,
misuse by employees, and the risk of hacking. Although smart printers don’t require a PC, they still
have the ability to exchange data with PC databases through wired or wireless connectivity. And
because the printers can all be programmed with identical functionality, they are interchangeable,
which avoids downtime or reprogramming if a printer needs to be repaired or replaced.
The Right Tools for the Job
3
4
There are a wide variety of applications for smart printers in a number of industries, such as:
• Connecting to a scale to create labels based on package weight or to error-proof a container
filling operation
• Using a barcode reader to create labels for supplies or a patient’s belongings during a
hospital procedure
• Communicating with an RFID reader to create labels for restocking returned merchandise in
a retail store
Regardless of the application, smart printers deliver consistent, accurate, high-quality labels that
rival or exceed those produced by traditional printing solutions.
The right tools for an error-proof printing job also include the right printing supplies and media,
which is an especially vital issue for operations that require the use of different media and supplies
for different product or packaging labels. Using the wrong label media can result in labels that are
easily damaged and barcodes that are unreadable, and not using the right supplies could mean
inks are incompatible with label materials, diminishing quality or label durability. To make sure your
employees are using the right label media and supplies, stock them in clearly labeled locations
close to the printing processes where they are needed so they aren’t mistakenly used in the wrong
processes. Color coding can help differentiate different types of labels.
The right tools for labeling processes can’t produce accurate labels without the right processes
in place. Some processes have built-in vulnerability to user error — whether it’s the chance an
employee could click the wrong label in a drop down menu, let an error in data slip through, misuse
color, or mislabel parts (e.g., left-hand vs. right-hand, similar, or sequenced items).
Adopting an on-demand printing process can help reduce labeling errors. With on-demand printing,
you print labels as they are needed, unlike traditional batch printing which creates the opportunity
for an employee to grab the wrong stack of labels that were printed in advance. Furthermore, when
using on-demand printing with technology such as PLC’s or auto ID solutions, the label is printed
automatically from digital input to a smart printer — and human error is completely eliminated.
On-demand printing ensures the right label for the right part/container every time. If there is an error
in data or design, or if the wrong media is loaded into the printer, it’s easier to correct the error —
and you only need to replace one label rather than a whole batch.
It’s also important to include quality assurance/control in your labeling process to ensure label
accuracy and compliance before items and packages are delivered to customers or placed on the
sales floor.
When compliance with regulations or customer standards is at stake, adding QC to each step
of the labeling process from design, printing, to application can help ensure you are meeting
requirements such as:
• Unique Identification (UID) for government contracts
• Globally Harmonized System of Classification and Labeling Chemicals (GHS)
• FDA labeling
• Country of origin food labeling
• Produce Traceability Initiative standards
• GSI 128 barcode specifications
• Automotive Industry Action Group (AIAG)
• Health Industry Business Communication Council
The Right Processes
5
Accept the Reality of Human Error
As long as there is the opportunity for an employee to make a mistake, one will probably happen
eventually. For this reason, solutions that are simple, intuitive, and easy to learn are the most error-
proof. Using a smart printer that receives data directly from equipment on a manufacturing line or
from devices such as an RFID reader or barcode scanner removes many of the opportunities for
human error from the labeling process. Smart printers also make it easier to train new employees
and help even the most experienced workers do their jobs more accurately and productively.
Training is another factor in minimizing labeling errors. Review the training program employees
undergo before operating label printing processes to ensure they are sufficiently briefed on how
to accurately and efficiently print and apply labels. Training should also include education on the
importance of the job these employees are performing and the responsibility they have to help
the company stay in compliance with regulatory and industry standards, as well as to their role in
providing top-notch customer service.
6
Take a critical look at the process currently used in your operation, and assess the risk of error. If
you find risk, eliminate it with these three key steps:
1. Make sure you use rugged equipment best suited to your operation, as well as ensuring
employees always use the right supplies and materials.
2. Implement on-demand printing processes to print the right label for the right item at the
right time
3. Deploy technology, such as smart printing, that removes the element of human error from
the process.
Keys to Error-Proofing
About Smart Printing Solutions from RACO Industries
A Smart Printing solution from RACO improves accuracy by eliminating mislabeling caused by
human error on even the most commonly mislabeled parts. Serialized label data can be stored in a
database, which provides an audit trail and streamlines recalls and warranty claims. Smart Printers
are as flexible and versatile as a PC without the “baggage” of a PC. It’s why Smart Printers are
best suited for Label Error Proofing applications. RACO Industries is an industry-leading integrator
of business solutions across barcoding, card, and GPS applications. From device configuration
to network provisioning, equipment staging, kit delivery, solution implementation, and ongoing
support, we make sure the solution addresses your business’ unique needs.
The measures you take to error-proof your labeling processes will have
return on investment (ROI) in cost savings and minimizing waste, but also through regulatory
compliance that solidifies your reputation for quality products and exceptional
service that your customers depend on.
About Honeywell
Honeywell Safety and Productivity Solutions (www.honeywellaidc.com) provides comprehensive
solutions that enhance workplace safety and incident response, improve enterprise performance
and enable greater product design innovation. Customers rely on Honeywell’s connected solutions
to provide real-time safety intelligence, increase worker productivity and enrich operational
intelligence with data-driven insights.
RACO Industries
5480 Creek Road, Cincinnati, Ohio 45242
(513) 984-2101 • 1-800-446-1991 • www.racoindustries.com