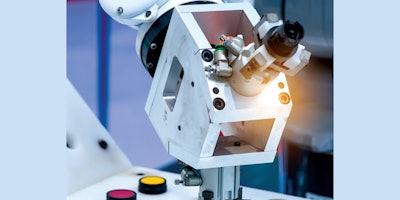
UPS
This white paper will tackle the challenges
that come with adopting smarter operations,
while also outlining some early steps
to get started.
Why Industrial Manufacturers
Can’t Afford Not To Invest
In Big Data
Industry 4.0
2 Industry 4.0: The Investment In Big Data
Introduction
The advent of the Fourth Industrial Revolution (also known as
Industry 4.0) brought with it the next phase in the digitization of the
manufacturing sector. However, many industrial manufacturers found
themselves unprepared for the disruption it caused to their traditional
business models. Many believed Industry 4.0 to be little more than a
buzzword or catch phrase; at best, it signified something that could be
as opposed to a force already taking root in the globalized marketplace.
The wake-up call came as industrial manufacturers began to
realize the power and potential of Big Data, and that implementing
data-driven solutions — or choosing not to — could dramatically
improve overall agility, flexibility and remove unseen vulnerabilities.
“The first hints of the power of Industry 4.0 could be seen in the
increased automation of various industrial processes in fully digital
factories,” says Srivats Ramaswami, the Chief Technology Officer
at 42Q1 . “The factories were implemented by companies who
integrated software platforms that link all aspects of manufacturing,
from initial product design to factory layout and manufacturing
process optimization to customer feedback after delivery. This
integration ties together each aspect of the manufacturing process.”
Perhaps even more appealing than seamless operations was
the opportunity to cut costs. For instance, a 2015 study from the
McKinsey Global Institute2 found that manufacturers could see a 25
percent reduction in maintenance costs and a 50 percent reduction
in unplanned outages by using Internet of Things (IoT) enabled
machines to monitor performance.
The Four Manufacturing Revolutions
1970s 1990s
2000s present
The lean revolution
takes a firm hold.
The rise of automation
greets the new
millennium.
Industry 4.0 shockwaves
drive the marketplace to
invest in smarter operations.
Outsourcing begins
to surge throughout
the industry.
— Jack Levis,
Senior Director of
UPS Process Management
“ Whether you’re a small or
large company, leveraging
the data you already have
into meaningful insights
puts you that much further
ahead of the game.”
3 Industry 4.0: The Investment In Big Data
Although a source of business disruption, the emergence
of Industry 4.0 and the onset of technological advancements
offers manufacturers the opportunity to rethink their long-term
operational strategies. To remain relevant and competitive, industrial
manufacturers must consider investing in and implementing smarter,
data-driven solutions to keep their enterprises agile and efficient.
What’s At Stake For Manufacturers
To respond strategically, industrial manufacturers should first have a
clear idea of what is at stake.
“The key theme of Industry 4.0 is a shift from mass production to
mass customization,” says Manu Tayal, a General Manager at Happiest
Minds Technologies 3. “The goal is that customers will have better
experience with customization and products will turn into platform.”
Ramaswami4, on the other hand, refers to Industry 4.0 as “as
the interaction of the real and virtual worlds.” “Powered by the
convergence of low-cost storage, ubiquitous sensors, powerful
artificial intelligence and analytics, the effect on the manufacturing
industry is huge,” he says. “These software systems do more than
trade data. They eliminate much of the human intervention that goes
with managing them. This next generation of automation, utilizing
big data, analytics and artificial intelligence, is one of the most
important drivers behind digital manufacturing and Industry 4.0.”
But, although critically important, the seamless connectivity and
automation now possible by integrating smarter operations is what
industrial manufacturers simultaneously find both enticing and
intimidating. What’s Holding Manufacturers Back
“For many manufacturers, change equals risk,” says Ramaswami.
“Disrupting their supply chain or factory lines can cost millions, with
untold damage to a brand and a company’s reputation. Given this,
many are understandably reluctant to embrace far-reaching changes
to industrial infrastructures and processes.”
Indeed, evidence of this reluctance to evolve and invest in smarter
operations is abundant.
For example, a recent survey of over 300 global manufacturing
executives5 identified gaps between where manufacturers know
they need to be and what actions they are taking now. For instance,
95 percent of respondents said they “expect more processes with
suppliers to be automated” within five years, however a mere five
percent said they were “very satisfied” with their progress.
The survey also found that only 23 percent of respondents
currently analyze and use data from their extended supply chains
for decision making, but that they expect that number to jump to 68
percent in five years.
Additionally, Deloitte’s 2016 Business Confidence Report6 also
revealed inconsistencies among C-suite leaders when it comes to
prioritizing and investing in innovation. The study found that the
strategy most C-suite executives are implementing centered on the
same, traditional business investments they had made for years,
rather than those directly leading to innovation.
...the seamless connectivity
and automation now
possible is what industrial
manufacturers simultaneously
find both enticing and
intimidating.
4 Industry 4.0: The Investment In Big Data
Research conducted by UPS and IDC and published in the 2016
“The Rise of Smart Operations: Reaching New Levels of Operational
Excellence” report7 also noted the “relative immaturity” of
companies “in their efforts to transform their operating models.”
Furthermore, according to the report, “The [study’s] results indicate
that the gap is widening between the companies that are aggressively
embracing smart operations principles and those that are falling
further behind.”
This gap in acknowledging the new possibilities offered by smarter,
data-driven operations coupled with a reluctance to invest leaves
industrial manufacturers vulnerable to outside competition. Moreover,
if manufacturers are both slow to respond and uncertain of how to
respond, they also risk their supply chain becoming antiquated.
Sean Riley, the global industry director of Software AG’s supply
chain and logistics, agrees. “The traditional manufacturers still have
a wait-and-see approach, which will unfortunately leave an opening
for the more inventive companies to grab market share,” Riley says8.
“It’s my belief that every manufacturer is going to be IoT-enabled in
some way, shape or form within three to five years, simply because of
the competitive differentiation that IoT as part of a larger architecture
provides.”
Start by Creating a Data-Driven Strategy
For industrial manufacturers looking to take control of their supply
chains, the good news is that, according to Ramaswami, “there are no
hard and fast rules to Industry 4.0.9” Even better, there is a lot of help
to be found along the path toward digital adoption and integration.
But first, and perhaps most importantly, companies must articulate
a strategy for transforming their current model to achieve the level
of operational performance needed to remain competitive and drive
business growth.
Senior Director of UPS Process Management Jack Levis says that
the first step is getting your company’s data in order. “Understand
the data you use to run your business, and gather all the data that
you can and start analyzing it,” Levis says. “Whether you’re a small or
large company, leveraging the data you already have into meaningful
insights puts you that much further ahead of the game.”
“Take a look at the status quo, examine the deficiencies that you’ve
come to accept day to day and use these as drivers for change,” Riley
says. “You need to focus on what falls in with your current strategy
right away, with the understanding of where you want to be in three
to five years as a company.”
Build Flexibility Into
Your Implementation Plan
“After a company has determined an objective, they need to plan
out how to make that happen, which can be ridiculously complex,”
Riley says. “The plan needs to include ways to be scalable and flexible,
as well as determine the amount of data captured and analyzed.
Manufacturers should also take a long hard look at how to inherently
build-in flexibility from the get-go.”
—“The Rise of Smart Operations”
“... the gap is widening
between the companies that
are aggressively embracing
smart operations principles
and those that are falling
further behind.”
5 Industry 4.0: The Investment In Big Data
According to Riley, this process can take years depending on a
company’s specific plan and desired outcomes — which is why he
also emphasized the critical role that external service providers or
transportation-provider’s play in the adoption process. “When you
have an outsourced service arm, you can offer new opportunities to
customers and gain another level of control,” Riley says. “All told, it’s
really a structural change in how that manufacturer is going to do
business.”
Levis also suggests that manufacturers should address their
fundamental needs early on to better prepare themselves. “It would be
unusual for midsize companies to already have on staff all the expertise
they will need to manage and make sense of their data,” Levis says.
“Outside expertise can be invaluable for basic steps such as auditing the
data sources you have, and how to access and store that data.”
Take These Steps Now
for an Immediate Impact
Although adopting smarter operations is a long-term process,
there are immediate solutions manufacturers can utilize today that
can help manufacturers gain more operational visibility to boost
efficiency, security and flexibility.
Third party services offer the advantage of providing both
immediate and experienced support for manufacturers looking to
transform their existing operations model.
For example, manufacturers looking to increase efficiency
and reduce the risk of error should look into the benefits of
automated shipping. High-value and time-critical shipments can
expose manufacturers to risks and, potentially, lead to a poor
experience with a valued customer. However, with solutions like
UPS Worldship® for high-volume shipping and multiple modes,
manufacturers can track every shipment to provide timely delivery,
compliance and reduce the probability of costly errors or losses.
This system reduces labor, expense and time — a key service that
could strategically affect a manufacturer’s business process and give
them that real sense of control that might be missing.
Boost Visibility with Advanced Tracking
Within “The Rise of Smart Ops,” the authors note that “companies that
are less aggressive in their smart operations to date could look to take
advantage of the technology and process scale investments transportation
providers have made in an effort to close gaps more quickly.”
For industrial manufacturers, one such gap is inventory visibility
while in transit; increased visibility across shipments not only
enables manufacturers to be more proactive and meet hard
deadlines, but it also helps them better manage whether they have
too much or little inventory at any given time.
With UPS Quantum View® technology, for instance, manufacturers
can maintain “virtually real time” visibility that is multi-modal and
not limited to small packages. This service means that suppliers can
quickly relay any critical shipment changes to customers.
“ Third party services offer the
advantage of providing both
immediate and experienced
support for manufacturers
looking to transform their
existing operations model.”
6 Industry 4.0: The Investment In Big Data
Prioritize the Customer Experience
by Mitigating Risk
For manufacturers anywhere along their path toward adoption, it is
important to understand that data and increased visibility inherent
to smarter operations can also enhance risk management — an area
of focus which includes financial and insurance services.
By investing in a transportation provider, this means working to
resolve potential shipping issues before they happen. UPS Proactive
Response® service, for instance, is a sophisticated monitoring
engine that continuously observes critical shipments. If either the
monitoring engine or a logistics expert identifies an impending
risk, then UPS initiates service recovery procedures tailored to that
specific customer.
This helps not only diminish potential risks in shipping but also
works to improve the overall customer experience.
Don’t Risk Being Left Behind
For decades, manufacturers were in the business of order
fulfillment10 — one driven mainly by in-person relationships and
a strong handshake. For small to midsize manufacturers, this new
digital reality is a fundamental change to how they do business. Now,
manufacturers must also be service providers, which means asking
how they can add value to their customers and throughout their
entire supply chain.
To adapt to this new reality, industrial manufacturers must address
and remove operational vulnerabilities if they are to sustain long-
term business growth and remain relevant within the industry. And
the decision to adopt data-driven, high-tech operations in the wake
of Industry 4.0 is no small feat — nor is it a simple one.
However, industrial manufacturers can’t afford not to invest in a
Big Data solution. Despite any feelings of reluctance or uncertainty,
manufacturers must rethink their long-term strategies if they are to
remain relevant, profitable and meet the ever-evolving expectations
of their customer base. And by investing in a logistics provider,
such as UPS, industrial manufacturers can begin to immediately
reinvigorate their operations regardless of whatever stage they’re at
in the integration and adoption process.
Visit ups.com/manufacturing to learn more.
UPS is a global leader in logistics, offering a broad range of solutions including transporting packages and
freight; facilitating international trade, and deploying advanced technology to more efficiently manage the
world of business. Headquartered in Atlanta, UPS serves more than 220 countries and territories worldwide.
To learn how UPS helps industrial manufacturing and distribution companies, visit ups.com/manufacturing.
The information in this report was researched and
produced by Manufacturing.net in conjunction
with UPS. Statistical data was researched and
compiled by Advantage Business
Media in March 2017.
About UPS
About This Report
Sources
1 “ The Coming Game-Changer In Manufacturing Technology:
Industry 4.0,” Manufacturing Business Technology, September 2016.
2 “ The Internet of Things: Mapping the Value Behind the Hype,”
McKinsey Global Institute, June 2015.
3 “Industry 4.0 And IoT,” Manufacturing.net, February 2017.
4 “ The Coming Game-Changer In Manufacturing Technology:
Industry 4.0,” Manufacturing Business Technology, September 2016.
5 “ The Current and Future State of Digital Supply Chain
Transformation”, April 2016.
6 “ The Deloitte Business Confidence Report 2016,” Deloitte, May 2016.
7 “ The Rise of Smart Operations: Reaching New Levels of
Operational Excellence,” UPS & IDC, August 2016.
8 “ Crucial Concerns And Steps In IoT Adoption: Q&A with Software
AG’s Sean Riley,” Manufacturing.net, March 2016.
9 “ The Coming Game-Changer In Manufacturing Technology:
Industry 4.0,” Manufacturing Business Technology, September 2016.
10 “ What’s Holding US Manufacturing Back?” Global
Manufacturing, April 2017.