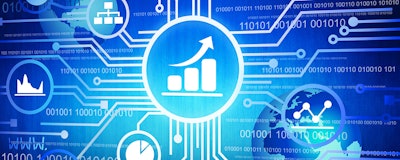
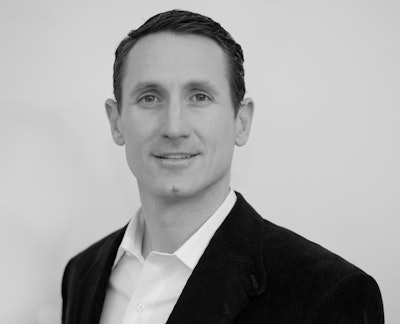
There has been an explosion of data in the manufacturing industry.
However, vast amounts of data can lead to a practical challenge: how do we systematically organize, analyze, and utilize data to improve energy efficiency, equipment performance and business operations?
Best-in-class manufacturing companies are already succeeding in managing data, mining it for useful insights and utilizing it to transform their businesses. Here are three straightforward ways real-time data analytics can boost your plant’s processes, production and revenue.
1. Increase Energy Efficiency
Each year, the U.S. industrial sector leads all economic sectors in energy consumption.
And despite the fact that U.S. manufacturers account for a significant portion of total national energy consumption, energy use in the U.S. is down per unit of gross manufacturing output. On whole, that means manufacturers are using less energy — not just because of decreased output, but because of smarter energy management over the past decade.
This trend is certainly heading in the right direction, but manufacturers still possess many opportunities to improve energy efficiency and reduce consumption. A recent McKinsey report found that most manufacturers have achieved a mere one-sixth of their energy savings because they are not pursuing a holistic or systematic energy strategy. The same report also found that manufacturers can reduce their energy use by 10 percent with small investments and up to 35 percent with larger investments.
Data analytics technology offers one simple and cost-effective solution for improving energy efficiency. Real-time data analytics can help plant managers understand their facility’s energy consumption, monitor usage for excess or untimely consumption, prioritize specific energy efficiency retrofits, promote behavioral changes among employees, set informed and achievable energy savings targets and, most importantly, reduce overall energy costs.
2. Improve Equipment Performance
Real-time data analytics don’t just help manufacturers save energy — data can also help them understand their overall equipment performance with device-level technology.
Take Panoramic Power, for example. The company — which now analyzes 5 billion data points per month — offers wireless electricity monitoring for large end-users. Their wireless sensors clip directly onto circuit wires and capture real-time device level data and process the data in an analytics platform. On a basic level, the technology — which is estimated to save large companies up to 12 percent with energy and operational insights — allows operators to see how they can make their facility more energy efficient, how their equipment is functioning, and how they can improve their overall business operations.
And there are an increasing number of case studies that showcase how this type of data technology can help operators understand their equipment performance. Recently, a manager of a 200+ megawatt coal-fired cogeneration plant in the U.S. Northeast was exploring ways to reduce their plant’s energy consumption. The plant manager began with a small pilot project of Panoramic Power’s device level monitoring solution on electric heat tracing panels in the CO2 facility as the test platform.
By December, the CO2 facility was taken offline due to a contaminant. In that time, extreme cold struck the region for several days. After the media was changed and the plant was ready to come back online, it was discovered that a condensate line from the main power plant froze, delaying the start-up for several days and requiring many hours working in frigid conditions to thaw out the line.
With real-time access to heat trace data, the technicians were able to identify the reason the line froze was because extremely cold temperatures and insufficient pipe insulation, thereby saving the plant critical time and additional expenditures.
3. Boost Business Operations
Beyond energy consumption and equipment performance, access to real-time data insights can help manufacturers systematically improve their overall business operations.
From a process perspective, data analytics can help managers strategically plan maintenance activities and enable a more efficient use of staff resources. It can also help them track scheduled and unscheduled maintenance activities while improving inventory control.
With maintenance, data analytics provide a clear opportunity to ensure the desired outcome of maintenance or retrofit activities and to prioritize those activities based on true business value.
Finally, it gives plant managers granular visibility into operational insights that are specific to an industry, market and building type. It allows for the augmentation of security, process monitoring, working hours and employee behavior control with energy data.
Real-time data analytics are already transforming the manufacturing industry. By beginning to harness the power of data, manufacturers can increase their energy efficiency, improve equipment performance and fundamentally transform their business operations.
Bill Kenworthy is Director of Business Development for Direct Energy.