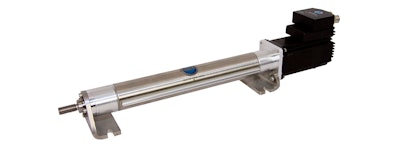
Pneumatic or electric? It’s not a new question. The merits of each have long been subject to discussion, but a fair amount of confusion continues to exist about which makes more sense for what.
For example, are you considering replacing a compressor and 200 pneumatic cylinders with electric actuators because you think you’ll save on compressor costs? Or, perhaps you are thinking about building a new machine with pneumatics because 30 electric actuators are far too expensive. Make the wrong decision in either case and you could waste tens of thousands of dollars a year.
Evaluating And Comparing Competing Technologies
The technologies underlying pneumatic and electric actuators are so different that one cannot be a drop-in replacement for the other. Considered separately, each has inherent advantages and disadvantages that must be considered in relation to performance, component costs, system costs and productivity gains.
Pneumatic Actuators
Pneumatic actuators deliver high force and speed at low unit cost in a small footprint. In fact, pneumatic cylinders provide more force and speed per unit size than any other technology, except hydraulic.
Other important characteristics of pneumatic actuators: force and speed are independent of each other and can be easily adjusted. The typical pneumatic application employs over-sized cylinders, because pneumatic cylinders are inexpensive, making a step up to the next largest diameter feasible and practical.
Pneumatics are most economical when the scale of deployment matches the capacity of the compressor. Small compressors are efficient and economical when they are employed to power a small number of pneumatic devices. Large compressors are efficient and economical when powering a large number of pneumatic devices. It is important to take this seemingly obvious point seriously. Make the wrong calculation and you will be facing unused compressor capacity, which can be very expensive.
Another important facet of pneumatics: pneumatic component costs are low, but maintenance and operating costs can be high. When cylinders need to be replaced, when air lines must be installed and maintained, and especially when paying for electricity to run the compressor, expenditures add up. According to the Department of Energy, about 25 percent of the cost of compressed air is due to maintenance, equipment and installation, while more than 75 percent is due directly to the cost of electricity.
To determine or anticipate the operating cost per pneumatic device deployed in a facility, you must consider compressor load. To reiterate — typically, compressor efficiency is lower when the compressor is partially loaded. Furthermore, if during the work week the compressors are left powered on at no load, a substantial amount of electricity is wasted. Waste is increased by inadequate maintenance (air leaks) and non-essential use of the compressor. These problems are not unusual because of the popularity of over-sized compressors and cylinders.
It can be a real eye-opener to look at the operating cost per pneumatic device employed in a facility, especially if you have not made cost calculations for quite a while and if the scale of your operations has shrunk. If there are 500 pneumatic devices using a compressor, your cost per device may average $100 per year. But, if there are only 50 devices using a compressor, your cost per device will be ten times greater, or $1,000 per year.
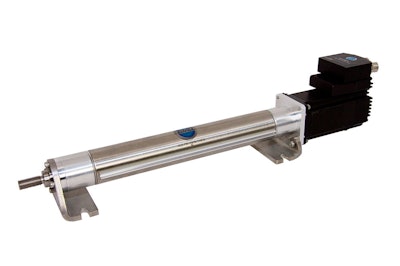
Electric Actuators
Electric actuators, in contrast to pneumatics, provide precise control and positioning. They help adapt machines to flexible processes and have low operating costs. They are most economical when deployed in a moderate scale in processes in which their performance advantages can be beneficial and when the electronics are separate from the actuator.
Electric actuators consist of a ball, acme or roller screw, connected via a coupler to an electric motor. As the screw turns, it moves a piston, which is connected to the rod or carriage that moves the load. Performance varies depending on the materials used.
Commonly used motors are steppers and servos. Step motors are an economical choice for accurate positioning at lower speeds. However, steppers can lose synchronization with the controller when employed open loop without an encoder, or if they are undersized for the application at hand. Servos by definition are closed loop and provide superior performance at high speeds, albeit at a higher cost.
Speed and thrust are related in the physics of an electric actuator. Speed is surrendered for thrust and thrust is surrendered for speed. This is an important distinction from pneumatic actuators. For a given electric actuator, more thrust will be available at low speeds and less thrust at high speeds. This characteristic is more pronounced with step motors and less with servos. For this reason, accurate sizing in an application is critical. Increasing thrust at the same speed requires different designs using different components and materials. An increase in thrust and speed requires larger and more powerful components and materials, which increase costs. Understanding and evaluating loading in the application under real conditions ensures specification of the right actuator while minimizing expense. Not understanding application loading leaves the engineer vulnerable to poor performance and high costs.
Component Costs Vs. Operating Costs
Components of an electric actuator include the mechanical actuator that translates motor rotation to linear speed and thrust, the motor, an electronic driver or amplifier to power the motor and a controller to control motion.
Operating costs of electric actuators are largely due to motor power draw. Controllers’ and drivers’ low voltage circuitry consume far less power. While component costs of electric actuators are high, operating costs are low. Those high component costs often deter the use of electric actuators, but the savings that can be realized in operating costs compared to pneumatics are not adequately considered and in some instances are ignored.
For example, manual changeovers (adapting a production line to a different product) can be expensive in terms of both lost production and man-hours required to implement the change. Over the course of a year:
- If changeovers are required once a week and each changeover requires two people for four hours at $50 per hour, man-hour costs amount to $20,800 per year.
- If products are produced at the rate of one per minute and the value of each product is $10, lost production costs amount to $124,800.
- The total annual cost of changeovers amounts to $145,600.
Electric actuators can substantially reduce changeover costs. The annual cost savings must be considered as part of the implementation decision.
When replacement cost, operating cost and process efficiency are considered, electric actuators’ annual costs are comparable to pneumatics’ costs. It helps when the scale of deployment is moderate and when motion system components can be replaced separately as they wear rather than replacing an entire integrated actuator motion control system.
The initial cost of actuators is only one small consideration in a list of issues for intelligent and cost-efficient automation implementation. The high cost of electric components can be misleading, but so can high compressor operating costs. Neither tells the whole story. Pneumatic operating costs can be controlled by sizing the compressor to fit the scale of pneumatic device deployment. Electric actuator costs can be minimized by accurate sizing, buying motion control components separately, and making a selection for applications where their use improves process efficiency. Pneumatic actuators have advantages in cost, size, thrust and speed, but electrics have advantages in accuracy, flexibility and control, making machinery and processes more efficient. An upfront estimated assessment of an application can prevent oversights and produce considerable cost savings in the long run while also ensuring that equipment matches the tasks at hand.
Gil Guajardo is a product manager for Bimba.
This article was originally published in IMPO's September digital edition.
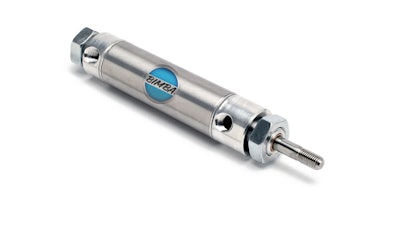