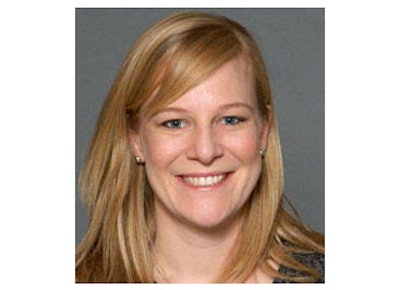
Continuous ink jet (CIJ) printers are commonly used to print codes on meat and poultry products because of their versatility. However, the low temperatures and high humidity typical of processing facilities in this industry can lead to printing problems if specialized CIJ inks are not selected and managed appropriately. Picking the wrong printer and ink can lead to a variety of issues, and risks include poor ink adhesion and low print quality, which can lead to costly downtime and a negative impact on the bottom line.
What Causes Coding Issues for Meat & Poultry Producers?
- Cold Temperatures. Temperatures in processing facilities are kept low to maintain the optimal shelf life of fresh meat products. Many inks could operate reasonably well over a broad range of temperatures. Since meat and poultry is among the coldest common operating environments, these temperatures are close to the bottom of or below the temperature specifications of many types of inks. Therefore, only some inks are specifically formulated to achieve the best adhesion, durability and printer performance in colder environments.
- Condensation. The meat and poultry production environment is humid. Products and packaging may also be exposed to temperature changes throughout the supply chain. For example, a cold product may be filled into a warmer package, or an open door may allow warm air into the cold manufacturing environment. This change in temperature combined with humidity in the air can cause condensation on the products before and after coding. Additionally, the washdown process may leave moisture on the equipment and surrounding production lines. Only certain ink formulations are specifically designed to penetrate the condensation to print clearly and adhere to the packaging — resisting the tendency for the ink to either transfer onto adjacent products or the production line conveyance systems. Water in the production environment can also act as a solvent, inadvertently removing ink codes before they have a chance to fully dry.
- Printer Calibration. Many meat and poultry producers store inks in a common store room for easier total inventory management. This storage room is typically much warmer than the production environment. This warmer ink has a thinner viscosity than the ink within the printer in the cold production environment. Printers are calibrated based on the viscosity of the ink when running in a cooler environment. When the warm ink is added to them, most printers automatically will adjust the viscosity of the ink to its calibrated target. While this occurs, the ink also will cool, naturally adjusting the viscosity of the ink. It may take some time for the ink to settle at the calibrated level since these two processes are happening simultaneously. Until the calibrated viscosity is reached, performance may be impacted and printed code quality diminished.
3 Key Considerations to Avoid Printing Problems
- Consider your ink. It is critical to select an ink that has been specifically formulated for your substrate and application. All inks are not created equal. What may seem like small changes to your production environment can significantly impact the type of ink that will work best for you. For example, an ink that may work well at 10 degrees Celsius may not work well at 5 degrees Celsius. If the product has water on it during the printing process, inks with specific condensation-penetrating formulations must be used. Therefore, in addition to other characteristics such as color and packaging material, you must have a detailed understanding of the environment to pick the ink that is best for you.
- Consider your printer. Some printers are designed to work in the difficult environment of the meat and poultry industry. These printers are adept at solving some of the ink issues associated with this environment. For example, they are able to quickly and automatically calibrate ink in these temperatures. The best printers store more than one cartridge of ink inside the core. When a warm ink or makeup cartridge is inserted into the printer, the warm fluid is slowly added in very small increments to the larger volume of ink in the core that has already cooled to the temperature of the environment. As a result, this process has a minimal effect on the viscosity of the ink in the printer, limiting printing problems.
- Consider your processes. It may be possible to alter your production processes for better ink performance. For example, the printer could be moved to a location on the line where condensation is less likely to form on the packaging, no longer requiring an ink that must penetrate condensation. Also, the location of the printer can be moved outside of the cold and humid environment to another location in the facility. Any move of printer location could impact your ink needs. For example, specialized inks for the tough environment may no longer be needed in this new, more temperate environment.
In addition, make sure to choose a vendor that has installation expertise and the widest selection of inks. Provide samples of all the materials you’ll be printing on, and have your vendor use their expertise to test one or more different inks to help select the best one for the application. Solutions are available to solve potential issues that may be encountered in cold and humid meat and poultry environments, but the key is finding the right one that’s comprehensive and customized for your needs.
About Videojet
Videojet Technologies is a world-leader in the product identification market, providing in-line printing, coding, and marking products, application specific fluids, and product life cycle services. Our goal is to partner with our customers in the consumer packaged goods, pharmaceutical, and industrial goods industries to improve their productivity, to protect and grow their brands, and to stay ahead of industry trends and regulations. With our customer application experts and technology leadership in continuous ink jet (CIJ), thermal ink jet (TIJ), laser marking, thermal transfer overprinting (TTO), case coding and labeling, and wide array printing, Videojet has more than 325,000 printers installed worldwide. Our customers rely on Videojet products to print on over ten billion products daily. Customer sales, application, service, and training support is provided by direct operations with over 3,000 team member in 26 countries worldwide. In addition, Videojet’s distribution network includes more than 400 distributors and OEMs, serving 135 countries.
©2014 Videojet Technologies Inc. All rights reserved. Videojet and Uptime Peace of Mind are registered trademarks of Videojet Technologies Inc.
For more food industry news and information, subscribe here and follow us on Twitter, Facebook or LinkedIn.