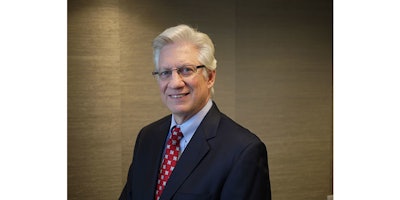
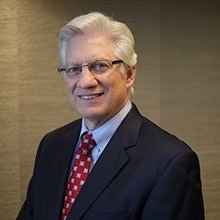
The goal of the Food Safety Modernization Act (FSMA) is to keep our food supply safe by preventing contamination instead of responding to it, by acting proactively rather than reactively. The result should be fewer foodborne illnesses, as well as stronger consumer confidence in the food they eat and the companies that supply it.
For large companies, the compliance deadlines for the rules on Preventive Controls for Human Food and on Sanitary Transportation have passed, and we now look forward to how inspections for those facilities will be conducted. Small businesses, with 500 or fewer employees, have additional time, depending on the rule. For example, there is no special compliance period for the Foreign Supplier Verification rule; all importers must comply with this rule by April 31, 2017. Regardless of size, all companies must be compliant within five years of the date of the final rule.
During this critical time period, as we wait for the results of the first inspections, it is imperative for small businesses to continue to move forward with their plans for compliance. It may take more resources and skills than are currently available, and additional efforts may be necessary to meet federal regulations. The following tactics may help as you navigate the road to FSMA compliance.
Communicate with Your Internal & External Partners
Organizations must have a comprehensive view of their business as they formulate their FSMA plans, both from inside and outside the company. Create a compliance team with a holistic view; FSMA regulations require involvement from a number of departments, including quality control, shipping, legal, procurement and IT. Each of these departments will be involved in the development, implementation and execution of the company’s food safety plan.
- Begin with a thorough assessment of your organization to determine current strengths and weaknesses.
- Examine what compliance activities are performed and how.
- Standardize documentation processes so that the necessary records can be produced within the prescribed timeframe.
- Perform audits as a means to identify the gaps and allow for improvement before a problem occurs.
External partners will be a critical link in the chain of FSMA compliance. Knowing your suppliers will be a crucial step in a company’s Hazard Analysis and Risk-Based Preventive Controls (HARPC) plan. The questions asked when sourcing a new supplier may have to shift from cost of ingredients to willingness to comply with regulations. The FDA expects manufacturers to be able to validate that they have pre-approved their suppliers and that they monitor for ongoing supplier compliance. Companies should categorize their suppliers based on risk factor and require more from higher-risk suppliers to prove their products and facilities are compliant. Confidence in the quality of suppliers will not only improve the company’s confidence in the quality of the final product, but will also help improve supply chain transparency.
Communicate with Your Employees
Compliance and food safety should be part of the company’s culture. Set the standard and apply it from the Executive Suite to the shop floor. Managers need to communicate relevant FSMA information on a regular basis and ensure those standards are understood. Training needs to move beyond attending sessions and focus on what has been learned from those sessions. The company will need to ensure that all employees who manufacture, process, pack or hold food are qualified to perform their duties. Successful compliance will demand long-term learning and ongoing awareness as these rules will certainly evolve. Companies should anticipate changes and adapt as needed.
FSMA also requires that “qualified” individuals prepare and oversee the company food safety plan; small companies may not have such a person currently on staff, and in the short term may have to bring in consultants to meet compliance dates. The Food Safety Preventive Controls Alliance (FSPCA) is developing a core curriculum and training material designed specifically to help small and mid-size companies comply with FSMA. Working alongside external experts to gain their insight and suggestions for improvements is another way to develop your knowledge base. Long Term, organizations should develop internal expertise, which can serve you well as you know your products, your processes and your facilities best. Sharing best practices and lessons learned with industry peer groups is another way to benchmark progress.
Invest in Software
A number of FSMA requirements benefit from the implementation of software. Smaller companies have the potential to adopt new technology more quickly than larger firms, as they tend to be less complex and have the longer grace period to comply with certain rules. Software will be indispensable in providing accurate records, as well as improving controls throughout the manufacturing process. Look for a user-friendly interface, capability to integrate with existing systems and the ability to provide alerts when conditions are out of tolerance. Scalability will be an important factor to consider, as you will want a software solution that can grow alongside your business. Not only can technology streamline current processes, reduce overheads and support compliance regulations, it could also put the company in a better position to improve relationships with customers and suppliers, and allow for possible expansion.
Conclusion
Compliance cannot be achieved overnight. The organization must strive for continuous improvement, creating a living food safety system that demonstrates where you currently stand, what processes and procedures are in place, and what you are doing to ensure those policies are followed. By communicating your strategy and investing in your infrastructure, you will be well prepared when your compliance deadline arrives.
Jack Payne is Vice President of Product Management & Solutions Consulting at Aptean