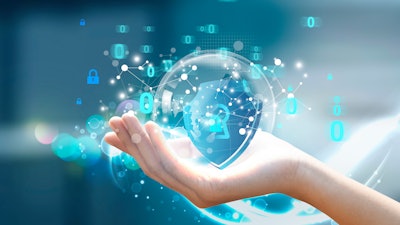
Industrial environments are embracing digital transformation at unprecedented speed. Manufacturing plants, processing facilities, and critical infrastructure organizations are rapidly connecting legacy equipment to modern cloud platforms, integrating machines and sensors into vast Industrial IoT (IIoT) ecosystems. While this integration promises massive gains in efficiency and productivity, it simultaneously opens new and concerning cybersecurity vulnerabilities, particularly at the industrial edge.
Traditionally, factories and industrial sites operated largely as isolated, self-contained entities. Cybersecurity considerations were minimal because industrial machines, controllers, and supervisory systems remained disconnected from external networks. Today, however, the rapid convergence of operational technology (OT) and IT networks has fundamentally altered this security landscape.
A Changing Cybersecurity Landscape
Equipment originally designed decades ago is now finding itself directly or indirectly connected to cloud environments, analytics tools, and external networks. But these legacy systems, often running protocols such as Modbus or OPC Classic, were never intended to face the relentless cybersecurity threats seen today. They frequently lack basic security measures such as encryption, strong authentication, secure firmware update capabilities, or even password protection.
Consequently, industrial systems have become attractive targets. Cybercriminals recognize that breaching an industrial network can halt production, disrupt supply chains, or worse, cause physical damage to facilities or pose safety threats to workers. Indeed, recent reports show a sharp increase in cyber incidents specifically targeting the manufacturing and critical infrastructure sectors. Ransomware attacks alone have surged, causing production stoppages and operational chaos for industrial operators around the world.
One reason these vulnerabilities persist is the historical approach industrial companies have taken toward cybersecurity, often adding it as an afterthought rather than embedding it from the ground up. Historically, industrial firms frequently deployed "bolt-on" security solutions, piecemeal approaches retrofitted onto existing legacy equipment.
While superficially appealing because of initial lower cost or perceived simplicity, these solutions fall short. Retrofitted security rarely addresses fundamental issues like secure device identification, encryption at every level, and continuous threat monitoring. Often, it leaves dangerous gaps between OT and IT systems, creating opportunities for cyber intrusions.
Moreover, industrial organizations often continue running outdated equipment due to high replacement costs, causing reliance on legacy systems that lack even basic security protocols. Even minor vulnerabilities at the edge can lead to catastrophic results when exploited by sophisticated threat actors.
Rethinking Industrial Cybersecurity: Key Strategies
Industrial companies need a new, proactive approach based on three core principles: secure-by-design systems, collaborative standards, and smarter use of technology.
- Security-by-Design, Not Security-by-Afterthought. Rather than retroactively patching security onto legacy equipment, forward-looking organizations must adopt security-by-design principles. This approach involves comprehensive threat modeling, embedding cybersecurity into equipment from initial design through deployment and lifecycle maintenance. When new equipment or upgrades are planned, businesses must prioritize built-in security capabilities, including secure boot, authentication, encryption, and robust firmware management. Equipment providers and industrial users must shift mindsets from reactive to proactive, prioritizing cybersecurity at every stage of development.
- Collaborative Industry Standards and Open Platforms. Another critical component of an effective cybersecurity strategy involves the adoption of open industry standards. Proprietary, vendor-specific solutions may appear secure initially, but they typically lock companies into outdated security architectures and slow responses to emerging threats. By contrast, open standards developed by collaborative industry groups provide a robust, continuously evolving framework for cybersecurity. For instance, widely recognized standards such as IEC 62443 and open-source initiatives like EdgeX Foundry enable organizations to rapidly respond to vulnerabilities, implement effective patches, and share best practices across industry sectors. Industry-wide collaboration enhances overall security, benefiting all participants and reducing vulnerabilities across entire sectors.
- Leveraging AI and Automation for Cybersecurity. Finally, managing the sheer complexity of industrial edge environments requires advanced capabilities beyond manual oversight. Here, artificial intelligence (AI) and machine learning (ML) technologies play a pivotal role. AI-driven cybersecurity solutions can proactively analyze data streams from countless connected industrial sensors and devices in real time, establishing "normal" behavioral baselines. By continuously monitoring and analyzing this data, AI systems quickly detect unusual patterns or anomalies that human operators might overlook, allowing organizations to rapidly respond to potential threats. This automation not only boosts response times and reduces operational risks but also significantly lessens the burden on human security analysts, who can then focus their efforts on strategic threat prevention and mitigation rather than continuous manual monitoring.
Securing the industrial edge demands more than just isolated security solutions. It requires a holistic, integrated approach driven by clear leadership, proactive strategy, and innovative technology. Industrial companies should start by assessing their existing cybersecurity infrastructure, paying particular attention to legacy systems and OT-to-IT integrations. A detailed cybersecurity audit will identify vulnerabilities that demand immediate attention.
Next, organizations must begin embedding security considerations directly into their operational strategies, procurement policies, and technology roadmaps. This proactive stance means evaluating equipment suppliers based on their commitment to secure-by-design principles, interoperability with open industry standards, and readiness for ongoing updates and support.
Finally, integrating AI-driven security solutions into industrial monitoring processes will greatly enhance the organization’s ability to detect and respond to threats swiftly, effectively, and reliably.
The Path Forward
The industrial edge represents immense opportunity, but only if the risks are managed properly. Companies cannot afford to neglect cybersecurity any longer. A shift in thinking from reactive patches to proactive, designed-in security is essential.
By adopting secure-by-design philosophies, engaging actively in collaborative standards communities, and harnessing the power of AI-driven technologies, industrial operators can confidently embrace digital transformation without leaving themselves dangerously exposed. The industrial edge is here to stay, but managing its cybersecurity effectively demands a fresh approach, and the time to act is now.
Andrew Foster is Product Director at IOTech, with over 20 years of experience developing IoT and Distributed Real-time and Embedded (DRE) software products.