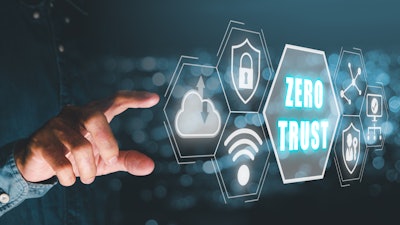
The concept of smart manufacturing, which integrates advanced technologies such as Internet of Things (IoT) sensors, big data analytics, artificial intelligence, robotics, and machine learning, has its roots at least as far back as 2006, when it was coined at a National Science Foundation workshop on cyberinfrastructure.
Building upon that foundation, today’s advanced manufacturing ecosystems seem to be outpacing Moore’s law, driving incredible developments in industrial IoT, AI, cloud computing, and, in turn, productivity, engineering and design.
However, as more elements within manufacturing processes come online and rely on other systems to work effectively, this connectivity comes with greater risks. In particular, the integration of digital technologies and reliance on interconnected systems expands the attack surface, which can lead to work stoppages and shutdowns and even pose physical threats to workers if critical controls are compromised. At the same time, slight deviations or configuration changes can alter production parameters, leading to product defects and potentially costly recalls.
Therefore, investments in smart manufacturing must be matched by an equal focus on cybersecurity strategies capable of mitigating these emerging risks. One powerful and agile method—implementing a Zero Trust strategy—has already proven itself to be able to provide the protection that smart manufacturing ecosystems require without impeding the operational efficiency and innovation these technologies bring.
Here’s what your organization needs to know to realize the operational benefits of smart manufacturing, thanks to the agility of Zero Trust.
The Benefits of Smart Manufacturing
The benefits of smart manufacturing are clear, offering businesses a wide range of advantages, including:
- Enhanced Operational Visibility. At the heart of smart manufacturing lies the ability to achieve enhanced visibility into the inner workings of processes and, in turn, the operational metrics that quantify progress. By seamlessly integrating advanced sensors along an assembly line and within individual machines—combined with machine learning algorithms and sophisticated analytics—manufacturers can monitor their operations in real time. This level of insight enables proactive decision-making, facilitates continuous improvement, and helps with further optimization of production processes.
- Predictive Maintenance Capabilities. One of the most compelling benefits of smart manufacturing is its predictive maintenance capabilities. By leveraging big data analytics, manufacturers can forecast equipment failures long before they occur. This predictive ability allows for more timely and precise maintenance, helping minimize downtime and extend the operational life of machinery. Such predictive capabilities reduce maintenance costs and contribute to a safer working environment by preventing unexpected breakdowns.
- Cost Reductions. Similarly, adopting smart manufacturing technologies can lead to significant cost savings. With more streamlined processes, improved yield, reduced waste, and optimized resource allocation, businesses can focus more funding on strategic investments.
The Cybersecurity Risks of Smart Manufacturing
Despite these benefits, the transition to smart manufacturing does not come without challenges. Enhanced operational visibility requires sensor data to be aggregated at a single point where intelligence can be applied, predictive maintenance requires vendors to have remote access to the machines on the factory floor, and cost reduction efforts eliminate waste but can also make operations more fragile and sensitive to disruptions.
Additionally, the integration of digital technologies broadens the attack surface, exposing manufacturing environments to an array of new cyber threats, including:
- Increased cybersecurity vulnerabilities. Malicious actors can exploit vulnerabilities within connected devices and systems, leading to potential work stoppages, shutdowns, and even physical threats to workers if critical controls are compromised. The interconnected nature of smart manufacturing ecosystems only amplifies these risks, making it difficult for security teams to stay ahead of new vulnerabilities.
- Potential for product defects and recalls. Cyber intrusions could also lead to the modification of production parameters, which could lead to product defects, system weaknesses or physical harm.
Smart manufacturing relies on real-time, reliable, and secure communications between varied systems, often across multiple networks and interfaces.
These digital environments are a prime example of where a Zero Trust security model could deliver. Zero Trust, which operates on the principle that no entity—inside or outside the network—is trusted by default, inspects and verifies every network request, regardless of whether it originated in the operational network. This level of introspection and verification keeps smart manufacturing systems—both individually and as an interconnected network—secure.
Despite the sophistication of the technology to implement it, making the shift to Zero Trust doesn’t have to be complicated. Here are four key steps to kick-start your Zero Trust journey:
- Start with Identity. The foundation of Zero Trust lies in establishing a strong identity management framework. Manufacturers should ensure that every device, application, and user attempting to access the network is authenticated and authorized. For some, this can mean implementing a commercial identity and access management system, such as Active Directory (AD). Others who already have these foundations should critically evaluate which assets need special protection and identify which user roles and other machines need to access these assets.
- Define your Segmentation Strategy. Protecting critical assets requires segmentation to isolate them against threats that may exist in the network. This segmentation is what prevents a compromise from turning into downtime and losses. Consider micro-segmentation tools, which can help you implement segmentation without triggering a “rip and replace” network redesign.
- Define Appropriate Access Methods. A completely segmented asset is a useless asset. To remain productive, users and other servers still need access. This is where the right technology can bring your Zero Trust strategy to life. Look for tools that can provide access controls with packet-level granularity right in front of critical assets. These tools should be able to differentiate packets originating from authorized and trusted users, devices, and applications, filtering out all others to allow operations to continue even if the network is compromised. Companies should also consider leveraging architectural concepts like a Zero Trust DMZ, which can provide a layer of protection against cyberattacks by terminating access in a jump host protected by Zero Trust.
- Adopt a Phased Approach. Implementing Zero Trust is a journey rather than a destination. It’s also not a race. Therefore, we suggest organizations start with pilot projects to test and refine their approach before scaling up across all manufacturing processes and sites. This phased adoption allows for the identification and mitigation of potential challenges early in the process, ensuring a smoother transition to a Zero Trust security posture as the roll-out scales up.
Bringing It All Together
As smart manufacturing continues to revolutionize industrial operations, these businesses can no longer overlook the cybersecurity implications of these advanced, interconnected technologies that are the lifeblood of their brand. By embracing Zero Trust principles of continuous but seamless authentication, manufacturers can enjoy the benefits of digital transformation while fortifying their networks against emerging cyber threats.
This balanced approach gives businesses the ability to continue to grow, evolve, and be innovative without compromising the security and integrity of operations. Through careful planning, strategic implementation, and ongoing vigilance, businesses can navigate the complexities of smart manufacturing with the help of Zero Trust, safeguarding their assets and maintaining a competitive edge in today’s global marketplace.
Dr. Jaushin Lee is the founder and CEO of Zentera Systems.