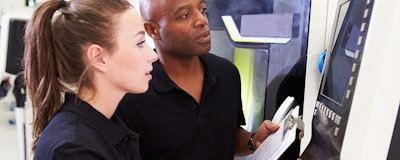
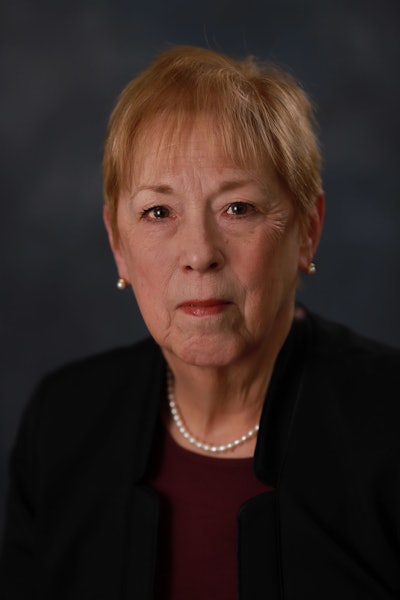
When operations are overhauled at a factory or warehouse, or a company starts to deploy new types of technology or equipment, jobs are almost always lost. The goal itself may be to reduce workforce costs—or it may be to improve quality, speed or to align with other companies in the supply chain. If the goal is upgrading and improving, will the existing workforce be capable of keeping up with the pace of change—or will some workers need to be replaced by individuals with better skills? Even in the case of significant workforce reductions, does that mean the entire workforce has to go? Or can some workers be retrained to be valuable contributors in the newly re-configured operation or other parts of the organization?
Whatever the case may be, it’s better to keep some employees. With a recent warning from the Deloitte Institute that 2.4 million manufacturing jobs could go unfilled between now and 2028 because of the nation’s skills gap—plus an additional 2.69 million jobs to be vacated by retirees and another 1.96 million openings due to industry growth—companies need to invest more resources into ongoing training for their existing employees, rather than trying to replace them from an already scarce pool of talent.
Robotics may reduce the need for assembly line workers, but the manufacturing process still needs people to maintain and troubleshoot that equipment and inspect the products for quality assurance. Workers on the assembly line, whose previous duties included reading technical drawings and instructions and calibrating machinery, can now be trained for other essential job duties such as those performed by instrument technicians/machine operators, CAD draftsmen, CNC operators, and quality control inspectors.
Of course, to keep up with demand, companies will also need to hire from the outside. But it’s better if they start by filling positions with the workers they currently have, who are already familiar with the company’s inner workings and have the potential to move up the ladder and take on more responsibility as department supervisors and plant operators. Implementing training initiatives builds stronger employees who are also invested in improving their workplace and allows for continual evolution, rather than jarring transitions.
One way manufacturing companies are creating training programs is by forming partnerships with educational institutions. Whether such programs succeed or fail largely depends on their structure, instructor background and the educational partner’s approach to the relationship. When searching for an effective program, there are several markers companies should be on the lookout for during this process.
Strong educational partners understand specific industries and individual businesses and will develop programs with the support of industry advisory committees. At the Community College of Allegheny County, we have found this model invaluable. In creating a forum for industry leaders to share information and analysis, we have been able to help companies identify trends and pinpoint their exact workforce needs. To develop on-point curricula, companies and educators must work together.
Astute partners will also have maintained long-term relationships with other companies training workers for specific jobs. They treat the companies that contract with them like clients—learning the business inside and out and listening carefully to the challenges described by executives before developing a customized curriculum. For example, while a conversation may begin with a focus on technical skills, it may eventually uncover a gap among employees in soft skills, such as writing, communication or teamwork. Employees who possess soft skills are in a better position to fill middle and upper management positions down the line, making them more valuable to the company.
The educator’s training facilities are another crucial consideration when choosing a program. Trainings cannot be conducted in classrooms alone. Students need sophisticated, state-of-the-art labs that replicate the types of issues they will face every day on the job and where they can learn to resolve complex technical problems.
One skill set that is particularly valuable in today’s advanced manufacturing workplace involves mechatronics. Mechatronics technicians, whose ability to install, maintain, modify and repair high-tech robotic systems, programmable logic controllers and other automated equipment, are highly sought after. Manufacturing companies may want to consider educational partners that are capable of training employees in this discipline.
Finally, it is essential that both employers and educational partners are committed to giving and accepting continual feedback on their training programs and adjusting the program and any aspect of the curriculum when workplace conditions or requirements demand it.
The time to prepare for future talent shortages is now. With an already small talent pool from which to recruit and hire—an issue that will only worsen with time as millions of manufacturing jobs are projected to go unfilled—manufacturing companies need to help their existing workforce employees adapt, not let them go. When given access to continual training, incumbent workers have proven adept at seamlessly integrating new technologies and other industrial innovations into their places of work, which in turn has enabled the companies they work for to adapt to emerging trends in the global marketplace without missing a beat.
Theresa M. Bryant is vice president of workforce development at the Community College of Allegheny County.