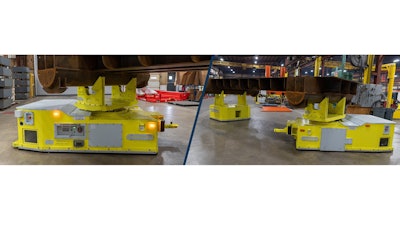
An agricultural manufacturer has partnered with Align Production Systems to implement an Automated Guided Vehicle (AGV) system, improving the assembly process for their latest tractor model. This partnership marks a significant step forward in heavy industry automation and highlights that even the heaviest manufacturing processes can be automated.
The agricultural manufacturer faced a significant challenge: moving a 28-foot tractor chassis weighing 110,000 pounds through various assembly stages. Traditionally, such tasks require extensive manual labor and time.
The solution was a wheeled transporter with Automated Guided Vehicle capability, with self-charging functions. This system enables the tractor to move easily through the assembly line before the AGV returns to the beginning of the line on its own.
The design included:
- Dual Component AGV System: The design features a tugger unit and a non-powered bogie unit, providing the necessary support and maneuverability to transport the long heavy tractor through the assembly line.
- Column Lifts and End of Line Lift: These lifts position the tractor for placement on the AGV at the beginning and end of the assembly line.
- Safety and Automation: Equipped with advanced safety scanners, the AGV system ensures a reliable and secure operation, focusing on worker safety.
A key factor in this project's success was the use of state-of-the-art simulation software for precise path planning. This technology enabled the mapping out of the AGV's route within the assembly plant, providing smooth navigation through all areas of their facility. The detailed input and planning from the agricultural manufacturer were crucial in developing a solution that perfectly met their needs.
The implementation of the AGV system at the agricultural manufacturer's site has already shown promising results, with full production set to begin soon. The system's automation capabilities are expected to improve efficiency, reducing both time and labor costs.
Read the Full Case Study