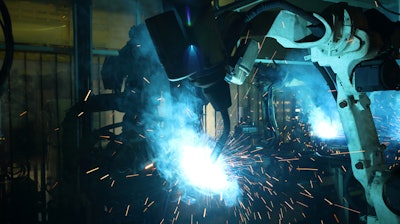
There is a digital revolution underway in manufacturing. Around the world, factories are betting on the potential of Industry 4.0 and the Industrial Internet of Things to unlock a new wave of productivity, profitability and growth.
When companies think about their digital strategies, it is easy to get caught up in the complexity. Factory managers worry that, to capture the benefits of Industry 4.0, they will have to rip out their existing infrastructure and start again from scratch. Or they think that they will need to add layers of additional hardware and software to handle communications and data analysis, with all the development, testing and maintenance overhead that implies.
There’s plenty of evidence that big industry 4.0 projects can deliver significant benefits. But there’s another way to think about digitalization in the factory environment.
Industry 4.0 also makes it cheaper and easier for companies to introduce new, digitally enabled approaches from the ground up, improving the performance and flexibility of the machines they already use and automating a wider range of tasks. In fact, “front-line” applications of new digital approaches are likely to be one of the fastest growing areas of industrial technology in the coming years, with the global market for factory automation products forecast to grow at an annual rate of nine percent over the next five years.1
Beyond the Basic Benefits
More, and better automation provides a compelling combination of benefits for manufacturers.
First, it addresses their immediate short-term goals: reducing operating and labor costs while improving productivity, quality and safety. That means many automation solutions, especially simpler, smaller scale applications, start paying for themselves straight away, and it can continue to capture additional value over the long term, connecting and integrating its automation systems into wider industry 4.0 networks and applications.
One of the most common building blocks of manufacturing automation is the requirement for linear motion. Linear actuators are used in countless industrial applications to transport, locate and position products, components and tools. The traditional way to achieve linear motion in the factory environment is with a fluid power solution. Companies have long relied on pneumatic systems for high-speed, low load applications, or turned to hydraulics where the must generate high forces.
As we move into the industry 4.0 world, however, many manufacturers and machine designers are finding that electromechanical actuators provide a better fit for both their current and future automation needs. Electromechanical actuators replace the hydraulic or pneumatic cylinder with a ball or roller screw mechanism, powered by an electric motor. They are available in a wide range of standard designs, and in modular formats that allow power, speed and precision to be tailored for almost any conceivable application.
As automation tasks become more demanding, the advantages of electromechanical actuation become even clearer. In fluid power systems, precise control of the speed and position of the actuator can be difficult or impossible to achieve, especially when a task requires significant variation of those parameters. Electromechanical actuators have a direct mechanical link between the motor and the screw that provides complete controllability of the system, with high levels of repeatability, down to the micron level as well as higher stiffness. Moreover, it is very easy to precisely change the speed along the motion cycle.
And because adjusting the speed, acceleration or positioning of an electromechanical actuator can all be achieved in software, automation systems using the technology are easy to fine tune, allowing users to continually adapt and improve their processes. That kind of flexibility is essential in many Industry 4.0 applications, from data-driven continuous improvement activities to mass-customization in manufacturing.
The electromechanical approach to linear motion can also deliver significant total cost of ownership benefits over the full lifecycle of an automation system. While actuators contain high-precision components, the critical parts are well protected from damage and contamination, leading to a long, and predictable, working life. When an actuator does need to be replaced, the swap is a quick and simple job that doesn’t require a lengthy system shutdown or specialist expertise. Electromechanical systems are extremely efficient too. An electromechanical actuator transforms 80 percent of the power it consumes into useful work, That’s around twice the efficiency of a hydraulic system, and more than four times better than a typical compressed air installation.
New digital technologies are upgrading the intelligence, responsiveness and flexibility of manufacturing processes. But the manufacturing world is physical as well as digital; the next generation of production machines will need muscles to match their brainpower. When it comes to linear motion applications, electromechanical actuators are proving to be the smartest choice.
Ewellix is a global manufacturer of linear motion and actuation solutions used in industrial automation, medical applications, mobile machinery and distribution.