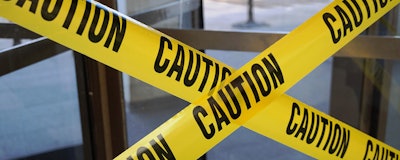
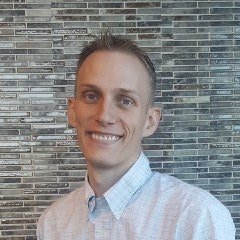
Crisis management, particularly in the manufacturing sector, can make the difference between an extended and costly disruption and a quick resumption of operations. The worst-case scenario, of course, is absolute failure and this has consequences that are far-reaching, such as affecting the financial well-being of stakeholders and the loss of livelihood for one’s hard-working employees.
Crises can come in several guises; natural disasters, cyberattacks, power outages, and criminal acts, to name just a few.
Crisis management has arguably been the biggest bane for manufacturers in the recent past. From the increase in cyberattacks to natural disasters such as 2011 earthquakes that led to the nuclear meltdown at the Fukushima Daiichi plant, the manufacturing sector has had its share of both natural and man-made disasters.
While nobody likes to think this can happen to their plant, the only way to minimize the negative effects in case of these emergency situations is to have a plan of action. In this article, we will try to give you some examples of what to expect and how to formulate that plan.
Illustrative Examples
Let’s begin by highlighting a memorable crisis for illustrative purposes.
A few years back, the earthquake and subsequent flooding in Japan led to huge issues with availability of supply for the worldwide automotive industry. The consequences were wide-ranging and included under-utilization of plants, longer waits on delivery of necessary parts, significant cancellation of already ordered components, and so on.
Similarly, during the Thailand tsunami disaster, many manufacturers were forced to shut down production or severely throttle output due to critical parts being in such short supply.
Is Your Company Prepared?
When a crisis strikes, it can really test the mettle of employees and the leadership skills of your management. If the immediate decisions made are hasty and without the adequate and correct information informing said decisions, more problems can ensue.
On the other hand, waiting for an extended period in the hope of obtaining all the data possible can leave your organization paralyzed as no decisions or actions are being taken. As you can imagine, this too can create additional challenges and prolong the crisis.
It is therefore crucial that a company has a detailed plan in place to lessen any potential disorder and confusion that come hand-in-hand with emergency situations.
Words of Advice to Help You Manage Emergency Situations
Have a Plan
Again, having a plan in place to address a crisis is obviously crucial. The plan should be in written form and have clear objectives, such as how to protect company workers and methods for keeping lines of communication open.
Among other things, a good recovery plan should have a multi-faceted list of specific actions to be taken in the event of some unexpected event or catastrophe.
On top of everything mentioned, it is also not a bad idea to have a different plan ready for different type of emergencies. For example, a crisis that happened because of a cyber-attack will require a vastly different approach from the aftermath of a hurricane hitting your facility.
Be Flexible
Don’t hold firm to first impressions of how to handle the crisis at hand. Over days and weeks, the makeup of a crisis will surely change. What may have been off the table one day can become super important the next.
If you acquire new information that supports a change in the original plan, don’t be afraid to amend it to address these new circumstances. While having a detailed plan is highly recommended, adjusting your actions to your specific situation is just as important.
Communicate With the Public
If a crisis can potentially impact workers or the general public in a negative manner, be prepared for the possibility of the media getting involved. Ensure that you have a competent and well-spoken person assigned to represent the company so as to deliver a consistent and clear message to the world at large.
It is also important to keep a line open to your customers and suppliers. Rather than having them hear about it all second hand from the aforementioned media, get ahead of it by providing pertinent information to them on a consistent and timely basis. Keep them all regularly updated throughout the crisis event.
Keep Employees Informed
Don’t keep your workers in the dark. Employees should be informed and up-to-date on events to help ensure that the business continues to operate as best as possible. This can also cut off at the pass any rumors that might lead to erroneous and damaging gossip shared with friends and family or put out on social media.
The Role of Maintenance in Disaster Recovery
Damage to your equipment and huge logistical issues that present themselves after every disaster will put your business continuity planning to the test. To get your facility up and running as soon as possible and without significantly breaking your disaster recovery budget (if you have one), you will need a well-organized maintenance manager.
Coordinating a big maintenance team is a challenge in itself. Luckily, having access to tools like computerized maintenance management system can help maintenance managers to stay in control of all work that is being done at any moment.
In crisis situations, the ability to quickly assign work orders, communicate potential problems, switch and reassign priority tasks, track what has been done and what still needs to be taken care of, is a necessity and not a luxury.
Conclusion
While a crisis certainly brings extreme challenges that can endanger the well-being of your organization, an effective crisis management strategy can do more than just lessen the pressure and the impact of whatever damage may result. It can even allow for a company to come out of the whole experience stronger than ever before.
Having a solid recovery plan in place is the key to survival of your business.
Bryan Christiansen is the founder and CEO at Limble CMMS.