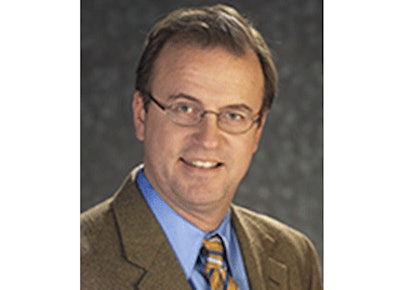
The main focus of the Food Safety and Modernization Act, which moves into its fourth year of practice this year, was to develop standards that food and beverage processors and suppliers can adhere to so, collectively, we can take steps to proactively prevent food contamination. FSMA was developed to improve upon the industry’s previous approach — responding to an outbreak of food borne illnesses after they had already occurred.
By establishing federal guidelines and setting-up safety parameters throughout the supply chain, at every touch-point, the industry can adhere to a common standard. It’s given us a more efficient way to eliminate potential problems before they reach the public, and, indeed, before they even enter the logistics stream. The retroactive measures enacted in the past did little more than respond to a problem that had already occurred. That resulted in potential harm to the public and product recalls costing the industry billions of dollars in lost sales, legal expenses, reduced consumer confidence and a drain on productivity.
Today, as in the past, standard operating procedures decree that anything moved into a food production area is moved on a pallet. I’ll repeat myself. Anything. Not some food, not a majority of a product. Anything. Pallets touch everything at every point along the way.
This can introduce significant risk if these pallets have not been specifically designed for sanitation, efficient use in a facility’s operations and adherence to FSMA. Consider, though, that captive, plastic pallets today do not introduce risk. Rather, these pallets are a manageable resource that can actually be used to eliminate risk.
Enter the reusable plastic pallet.
Food and beverage companies are implementing these pallets at an increasing rate. Reusable, hygienic plastic pallets are designed to be easily sanitized, non-porous and cleanly move and store food products within a facility, supporting overall sanitary conditions. That gives businesses a tremendous opportunity to make a difference — delivering a consumer-safe product quickly and efficiently to the marketplace, therefore increasing profitability, enhancing safety, increasing consumer confidence and saving those dollars that used to collect in loss margins.
Implementing Plastic Pallets for Success
Packaging equipment must meet a series of criteria to be considered sanitary and useful for a facility’s operational standards. This ensures repeatable performance and seamless interface with equipment day in and day out. Reusable plastic pallets have dimensionally consistent characteristics so your system runs efficiently and cleanly. Your packaging should:
1. Be cleanable
2. Be made of materials specific to the application requirements (ie FDA-approved, etc.)
3. Be accessible for inspection, cleaning and sanitizing
4. Contain no space for liquid collection
5. Have no hollow areas
6. Contain no niches
7. Be non-porous as to not absorb moisture or odor
8. Deliver sanitary operational performance
9. Support validated cleaning and sanitizing protocols
10. Have the ability to sort and separate. For allergen control, loads need to be stored separately. Packaging can be color coded to support allergen control procedures.
Keep this checklist of expectations in mind when introducing plastic pallets into your operations and supply chain. If you’re making a change to reusable plastic pallets, understand those basics. And, equipment and personnel should be trained to meet hygiene and sanitation standard operating procedures.
Next, consider how some of the latest innovations accommodate supply chains and facilities that need to regulate to FSMA requirements. It’s easier than ever to make the switch to reusables and the benefits go far beyond better accountability for contaminants.
What to look for
Pallet Design/Engineering
For pallets in the food and beverage industry, ease of cleaning is top of mind. It’s important the pallet manufacturer minimizes the surface area to be cleaned. Reusable plastic pallets used within the food supply chain should be designed with non-porous material that does not absorb moisture. One-piece designs with no crevices, cells, hollow area or cavities eliminate the potential for contaminants to collect, regardless of pallet orientation (upright, stacked, on floor, etc). An open deck pallet means flow-through cleaning and quick drying, to get the pallet back into your supply chain with little downtime.
Unlike wood pallets, plastic pallets are designed to be dimensionally consistent, free of sharp edges or protruding fasteners that can damage products, automation, the plant floor or personnel. They are also free of nails or staples and will not splinter or break, causing damage to machines and downtime in your facility. This ensures a safer product, clean workplace for floor workers and repeatable performance that keeps your facility functioning efficiently.
Material Innovations
Reusable plastic pallet designs also take into account many recent innovations in materials. Any food or beverage industry supply chain logistics team would be smart to consider how the latest advances serve their needs. Pallets should be manufactured with:
- FDA-approved material if in direct contact with food. FDA-approved material has 100 percent virgin content.
- Materials that do not readily absorb environmental contaminants like odors, bacteria, pesticides, etc.
- Materials that allow for high-temperature washing.
- Custom coloring and branding options to color code and segregate loads.
- Labels/hot stamping to identify pallets for lot numbers.
- Materials and design that can increase edge racking capacity
- Materials that can work in various temperatures (ie cold storage)
- Optional X-ray- and metal-detectable material for load inspections.
Cleaning
There are two categories of pallet cleaning today. Since every industry and plant requires a different level of cleanliness, it’s smart to look at all the options available and make a choice based on which best serves your needs for your supply chain.
Microbiological Cleaning, or Industrial Sterilization
- High-heat cleaning process where a minimum temperature of 165° F is sustained and sterile conditions are maintained in a designated cleanroom.
- After cleaning, pallets are wrapped or bagged and stored in the cleanroom. The process is fully documented.
- This process is most effective against a broad spectrum of impurities.
Examples include:
--Traditional pallet washers: Wash/rinse conveyor system.
--UV or steam cleaning
Non-Microbiological Cleaning:
- Cleaning process where no minimum temperature or designated cleanroom is required. Examples include:
--Spray/power washing: Spot cleaning.
--Manual cleaning: Hand washing.
--Air compressor: To clean dust and debris.
Today there is no current standardized cleaning process, but retailers, and food, beverage and pharma CPGs are looking for more standardization to preserve the integrity supply chain. When planning their cleaning processes, companies should ask:
- Do we need full sterilization or non-microbiological cleaning?
- Will cleaning be done in-house or out-sourced?
- How often must your pallets be cleaned?
- What kind of documentation is needed? (e.g. date stamping, etc.)
- What are the storage needs and practices (e.g. indoor versus outdoor)\
Evolving for long-term success
In order to be successful, reusable packaging must evolve as new needs arise. (ie new SKUs, new retailer requirements, etc.) Your plastic pallet provider should watch for trends impacting your business to ensure they are supporting your goals. As FSMA continues to be a focal point of change within the food and beverage industries, the ability for reusable plastic pallet manufacturers to drive evolution through customer-focused innovations is more important than ever.
Change in our industry, embracing methods that encourage sustainability; environmentally, financially and operationally – is inevitable. The leaders are the innovators who facilitate that change. Those are the ones you should seek to learn how a simple reusable plastic pallet can make a true impact on the safety of your supply chain and the sustainability of your business.