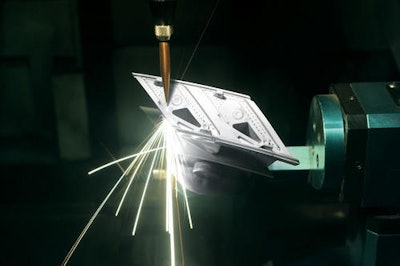
Leonardo da Vinci always seemed to be hungry for new ideas, but sometimes he may have been just hungry. Some 500 years ago, he designed a roasting jack that powered an automatic rotisserie. It used hot air rising from a fireplace to spin a horizontal vane placed in the chimney above it. The vane was attached to a vertical rod that turned the spit, and, presumably, his dinner.
The jack was one of the world’s first turbines and engineers have been using the same principle inside jet engines and power plants ever since. Since high heat can make turbines more efficient, the hot sections of modern turbines operate at temperatures above 2,500 degrees Fahrenheit, much higher than Leonardo’s design and near the melting point of steel.
For that reason, their blades, which are shaped like aircraft wings and machined to extreme accuracy, require very sophisticated ways of cooling. Engineers riddle the blades with a maze tiny channels and holes that bleed in enough cooling air to protect them. But making the holes in the right places without weakening the blades, which spin thousand of times per minute and must handle titanic pressures, is akin to magic.
Traditionally, companies have used lasers to make the tiny holes, heating the surface with the beam until the steel vaporizes. But that’s a delicate business. The metal can sputter and form molten microscopic gobbets that can spread through the air and stick to the finely machines metal surface.
Charlie Hu, an industrial manufacturing engineer at GE Power & Water, is exploring a different way. He is drilling cooling holes with a technology called Laser MicroJet developed by the Swiss company Synova.
The Laser MicroJet fires a laser beam inside a hair-thin jet of water, which acts like an optical fiber and guides the laser to the blade surface. The jet also helps cool down the surrounding material and flushes out machining debris. The technology could allow engineers to make more durable parts faster and design turbines that perform better.
Starting in 2011, it took Dr. Hu three years to adapt the method to turbines and take it out of the lab at GE Power & Water in Greenville, S.C. “We had to redesign the laser jet to the geometries we required,” says James Cuny, engineering executive at GE Power & Water. “Before this, the machine used for other applications was like a big barrel with a laser coming out of it. It was not very conducive to what we required.”
GE has already used the technology to make gas turbine blades. The company is now looking at applying it to other related businesses, such as aviation. “There is a lot of great development so far on this,” Cuny says.“Our engineers are excited about pushing the limits of the technology and bringing it to the market in the very near future.”
Dr. Hu’s mind is already on the next idea. Since the water jet can be also used to slice materials, GE and Synova are investing in a new technology that combines the advantages of both water and laser cutting in a single operation.
Leonardo invented his turbine while thinking about grilling. Hu’s ideas give GE a new cutting edge.
For more stories like this, visit GE Reports.