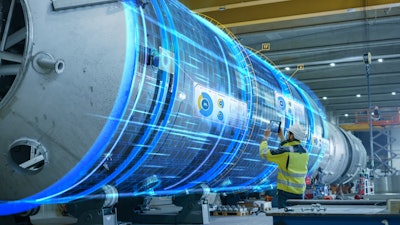
Maybe you've used Google Maps Live View to orient yourself in a new part of town; or noticed a "See It In Your Space" option when shopping for a new couch on mobile.
These features use the camera on your device to "see" what's in front of you. Then, the technology overlays virtual objects onto your display. The experience creates an augmented reality (AR) that blends the physical and digital worlds.
One of the best parts? AR technology is rapidly evolving beyond consumer applications – and there are already clear benefits for manufacturers. Here, I'll share three industrial AR use cases that show why this technology should be on every manufacturer's radar.
1. AR Enables Remote Inspections
For manufacturers, inspections are a necessary part of regulatory compliance. But inspectors have long queues and little support in a tight labor market. That means it can take a while to get an inspection on the calendar – not to mention the time it takes for an inspector to drive to your facility.
With the right technology, though, on-site workers can remotely consult inspectors without the need to wait for an in-person visit. Workers only need two things:
- A handheld (or hands-free) smart device: A smartphone, tablet or even industrial-grade smart glasses – as long as the device has an external camera and internet connectivity.
- AR-enabled visual support software: Allows workers to video call inspectors. Thanks to the worker's device camera, the inspector can see everything the worker sees. What's more, they can use AR to guide the worker through the inspection process by overlaying an inspection checklist on the worker's display and circling or screenshotting key areas as they appear onscreen.
After each AR-powered remote inspection, workers can pull call reports with the most important details, from time-stamped screenshots to onscreen annotations. The overall result: more efficient and flexible inspections that make it easy for manufacturers to stay compliant.
2. AR Reduces Equipment Downtime
Equipment downtime has always been costly for manufacturers. These days, though, the costs are steeper than ever. Last year, unplanned downtime cost manufacturers 50 percent more than in 2019-2020 – and totaled as much as $2 million per hour in some sectors.
Amid a surge in manufacturing investment and demand, manufacturers need every tool available to reduce unnecessary downtime. AR can help.
With AR-powered remote visual support software, workers can remotely connect with experienced technicians to help diagnose equipment problems and fast-track repairs. The process works a lot like remote inspections:
- A worker video calls a technician using their handheld or hands-free device.
- The technician guides the worker through step-by-step troubleshooting.
- With AR, the worker can view equipment specifications, 3D part models, and more as an overlay on their display.
This remote-guided support model can ensure repairs happen as soon as a machine goes down – versus waiting hours for a technician to arrive on site. Equipment gets back online faster, and manufacturers can continue producing at pace.
3. AR Powers Smart Inventory Management
Most manufacturers use an inventory management system to monitor inventory levels and streamline stocking and picking. But in large facilities, it can be tough for workers to find exactly where to store new inventory or pick an order for shipping.
AR connects workers with real-time inventory data to make inventory management simple—picture, for instance, a worker that needs to pick orders in a specific warehouse zone. With AR-powered smart glasses, they can see a navigational overlay pointing them toward the correct zone. And as they pick orders, they can receive on-display confirmation that each order is the correct type and quantity.
At scale, this technology can help manufacturers better manage inventory and boost operational efficiencies. That's huge for customers and the bottom line.
Augmented Reality Isn't Just Sci-Fi
AR might seem too futuristic – like something out of a sci-fi movie. But that's because most manufacturers haven't incorporated it into their operations.
The truth is that AR technology has clear practical applications, especially in the manufacturing industry. For manufacturers looking to stay ahead in this economy, AR solutions should be a key part of their tech stack.
Rama Sreenivasan is co-founder and CEO of Blitzz, a live, remote video support and inspection platform. Sreenivasan has led the company through its initial inception, launch, and subsequent growth to several million video support minutes per month. Major customers include BMW, Sealy, Fedex and Rogers Telecommunications.
Before founding Blitzz in 2017, Rama spent several years working as a scientist and educator. His biggest joy comes from helping others solve their problems, and he is passionate about finding effective ways to disseminate knowledge. Sreenivasan has a Ph.D. and MS in chemical engineering from the University of Maryland, College Park. He also did his postdoctoral research at MIT in Cambridge, Boston.