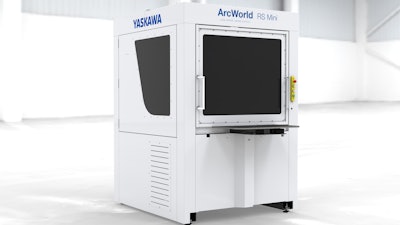
At IMTS 2022, Yaskawa Motoman (Booth #236601, North Building, Level 3) will display its smart robotic solutions designed to help manufacturers optimize supply chain flow and solve workforce shortages.
The robot demonstrations include:
Collaborative Welding Workcell
Designed for optimizing small- to medium-sized part production for medium volume fabrication, this flexible solution comes pre-engineered with arc flash protection and fume mitigation, and it features the IP67-rated HC10DTP collaborative robot for use in harsh welding environments.
Ideal for supplementing manual welding or for rolling up to large heavy workpieces, this six-axis cobot with hand-guided teaching, also includes Power and Force Limiting (PFL) technology that enables operation with or in close proximity to human workers.
The existence of PFL enables safe operation at collaborative speed or the shift to full speed in industrial mode as production needs change. An integrated weld package using a Miller Auto-Continuum 350 is shown, but it is compatible with all major brands. This demonstration also highlights Yaskawaโs intuitive Universal Weldcom Interface (UWI) pendant application that helps users gain easy control of any weld process or parameter.
Compact Welding Workcell
Ideal for replacing or supplementing manual welding of small parts, the compact and flexible ArcWorld RS optimizes floorspace utilization in tight working environments. Requiring only 2.3 square meters (25 sq ft) of floorspace, this model features a manually indexed rotating station (RS) that offers two fixture tables with 100 kg payload capacity per side. This facilitates quick changeover, allowing parts to be safely loaded and unloaded while the opposite station part is welded. Parts up to 425 x 700 x 990 mm can be processed.
This workcell includes the six-axis AR900 arc welding robot with YRC1000 controller, UWI pendant application and an integrated weld package with a Lincoln Electric Power Wave R450 power source. The ArcWorld RS uses safety-interlocked side panels for easy programming and equipment access, and it is enclosed with sheet metal and light-reducing polycarbonate for arc and spatter protection. A Functional Safety Unit (FSU), a built-in extraction hood and a four-button operator panel with E-stop is also included.
High-Volume Welding Workcell
Built to optimize medium- to large-sized part production, the pre-engineered ArcWorld 6200 (AW6200) arc welding workcell features two streamlined six-axis AR1440 arc welding robots with expanded wrist range for improved application flexibility. The sealed-drive, AC servo-driven RM2-1275 Ferris-wheel positioner utilizes the MotoMount fixture mounting system that enables the positioner to be lagged directly to the floor and eliminates the need for precision alignment or machined bases.
Multiple robot control with coordinated motion between devices is highlighted using a single teach pendant. The AW6200 includes an integrated welding package (Miller power supply option shown), as well as the Universal Weldcom Interface that enables full utilization of power supply capabilities. Shipped on a common base with integrated cable management for easy setup, this workcell also features enhanced safeguarding, including an FSU.
Dual-station Welding Workcell
Ideal for scaling-up production for small- to medium-sized part welding, the ArcWorld 52S is a space-saving arc welding workcell for busy fab shop settings. Featuring a dual-station configuration with automated roll-up doors, the AW52S is ideal for loading/unloading a part on one side while the robot welds on the other, increasing product throughput.
The slim-arm AR1440 arc welding robot with YRC1000 controller optimizes torch access to reduce cycle time. The controller and the robot power supply (Miller option shown) come on a sub-base that can be pulled out for servicing access, as needed.
Each workstation contains a 775 mm tabletop with a 685 mm depth and utilizes a servo-driven MHT185 positioner to turn parts while welding, eliminating sweep time. An integrated FSU ensures robot operation happens in areas clear of operator presence. This workcell also features the UWI pendant application and a Wandelbots TracePen, a no-code teaching solution for easy robot programming.
Painting Workcell
Highlighting the ability to create smooth, consistent finishes for small- to medium-sized parts with efficiency, this workcell features the compact MPX1950 painting robot. Factory Mutual approved for use in Class I, Div. 1 hazardous environments, this small footprint slim-arm model allows for minimum installation space and its reduced interference envelope enables painting of workpieces closer to the robot. The hollow inline wrist has a 7-kg payload capacity and is ideal for mounting various spray guns and small bells. The MPX1950 is featured with a Keyence SZ-V-series safety laser scanner for innovative workcell safeguarding.
Mixed-Process Workcell
Featured in an assembly-type demonstration, the four-axis SG650 SCARA robot and the six-axis GP7 multi-purpose robot are ideal for assembly and sortation, as well as multi-process systems requiring pick-and-place capability. The SG650 offers a 650 mm radial reach, 210 mm long U-axis stroke and a 6 kg payload capacity. It is controlled by the compact YRC1000micro controller that has a small footprint (425 W x 125 H x 280 D mm), and it can be installed in either a vertical or horizontal position, as well as within a 19-inch rack.
The compact and efficient GP7 offers 972 mm horizontal reach, 1,693 mm vertical reach and 7 kg payload capacity. Both models can easily be integrated with feature-rich vision functionality, such as MotoSightโข 2D.
Offline Pallet Pattern Generation
Enabling fast deployment of complex palletizing systems, PalletSolver is an easy-to-use PC-based software solution. PalletSolver allows users to quickly generate ideal pallet patterns offline for virtually any mix of SKUs. An online component optimizes execution of pattern files and robot operation. Single and complex multi-line palletizing is easily handled. Two high-speed GP7 robots will demonstrate the capabilities PalletSolver has to offer for end-of-line production processes.
3D Vision for Bin Picking
Featuring a GP7 robot working alongside the extremely compact MotoMini robot, this workcell features MotoSight 3D BinPick โ the next generation of vision technology for picking applications. The system uses a single 3D camera with integrated lighting to quickly and easily recognize then pick parts that are randomly placed in bins. 3D CAD matching provides simplified, accurate part registration, enabling even complicated parts to be identified.
Collaborative Machine Tending
Utilizing PFL technology to protect users from potentially harmful contact situations, the six-axis HC10DTP collaborative robot reduces the need for hard safety fencing and expertly facilitates machine tending high-volume production environments. Easily integrated with existing automation or machinery, this demo highlights the use of Speed and Separation Monitoring, where additional sensing devices (i.e., laser scanners and light curtains) for safety zone monitoring are used.
Hands-On Programming Experience
This demonstration features three HC10DTP collaborative robots with hand guiding and highlights easy robot programming for fast deployment or deployment on demand. The easy-to-use touchscreen Smart Pendant โ using software version 2.1 with a built-in Classic Interface function โ will also be featured. Ideal for novice robot programmers, the innovative Smart Pendant utilizes patented Smart Frame technology that determines the operatorโs orientation relative to the robot. This makes the robot user the frame of reference and eliminates the use of conventional coordinate (X, Y, Z) frames for easy command of robot movement.
For more information, visit https://www.motoman.com/en-us.