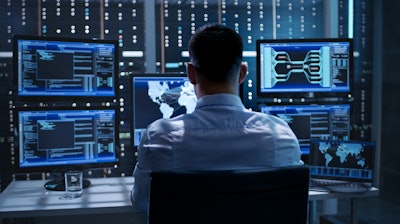
Manufacturing has seen huge changes in the last few years. And with the move towards Industry 5.0, here are some of the top digital trends to consider:
- The Internet Of Things Will Become More Prevalent. More control over manufacturing automation enables you to make the whole manufacturing process safer, quicker, and more cost effective. Monitoring equipment from wherever you are offers a key safety benefit.
- Workplace safety. Obviously workplace safety has always been important, but in light of the pandemic it has taken on even more significance. 'Now there's more to do to keep your staff safe, such as sanitization, social distancing, and so on' says writer Annalise Harmon from Elite Assignment Help. "Employers are now using new technology to help facilitate these new measures."
- Changing To B2C. A lot of manufacturers are moving from a B2B model to a B2C model because new digital trends make it easier to work within this model. Potential advantages include a faster time-to-market timeline and better pricing control.
- Changes To ERP Systems. Enterprise Resource Planning systems have been around for a while, but there have been major changes to them thanks to the pandemic. 'You'll see other systems being overlaid onto existing ERPs, so they don't have to do everything' says journalist Chris Winstone from Revieweal. "These are referred to as Power Apps, and they can do everything from track employee safety to creating back-to-work systems."
- 3D Printing Makes Production Faster And Cheaper. In recent years 3D printing has been becoming more and more of a fixture in manufacturing. in addition to producing prototypes, it's also become a good method for tooling - improving speed and cost controls.
- Remote Servicing Is Possible Through VR And AR. Earlier we touched on how more work is being done remotely, in order to ensure staff safety. One way they've been doing this is through virtual reality and augmented reality. A manufacturer can send a customer a VR and AR enabled device that enables them to do some basic troubleshooting on their product. It can help you walk customers through the steps - making customer service safer and easier.
Emily Henry writes for Paper Fellows and Big Assignments, covering manufacturing trends. She also edits at Simple Grad.