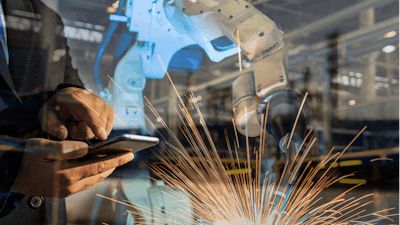
When the manufacturing industry began to embrace digital technology a decade ago, it adopted a new identity — smart manufacturing or Industry 4.0. Applying cloud, automation, analytics, machine learning and big data to production operations created a connected ecosystem for manufacturing and supply chain management, and became a high-growth market. At the start of 2020, the sector was on track to grow into a market worth more than $300 billion in the coming five years.
Then the pandemic hit. By spring, millions of workers had lost their jobs. Some plants closed temporarily or slowed production so workers could spread out to maintain a safe distance from one another. Investment in smart manufacturing fell too, by 16 percent between March and April alone. Some researchers predicted that such a pull-back would dampen investment through 2025.
But the conversations we’ve had with C-suite manufacturing executives and service providers suggest investment in smart manufacturing will intensify. By 2025, it could be worth more than $400 billion. It’s no wonder.
Smart manufacturing technologies streamline operations, make supply chains more resilient and enable better customer experience and the potential for data-driven top-line growth. As manufacturers realize they must balance a laser focus on cost take-out with critical investment in digital technology, who can argue with reducing costs, speeding up order and delivery times, and improving the quality of products, while enhancing worker safety?
Some businesses had already begun a digital transformation before COVID-19 impacted the manufacturing and delivery process for every conceivable product.
The automotive industry, for example, has already adopted new business models to tackle strategic imperatives such as connected and electric vehicles and automated and shared solutions. The pandemic gave companies even more reason to reassess their digital strategy, accelerate the move to cloud and be less dependent on specific locations, thereby making their operations more resilient.
As a result, manufacturing supply chains have become increasingly complex and integrated. Demand has surged for more effective equipment and increased manufacturing yield. Enterprises are now using applied analytics to anticipate and mitigate the disruption in operations within and across plants and the supply chain.
Tools of the New Age Trade
The use of digital twins is on the rise. These digital representations of the physical manufacturing process create simulation models to optimize the product lifecycle.
Augmented reality and virtual reality technology are popping up in a number of use cases, particularly for equipment maintenance and plant employee training. Finally, 4G, LTE and 5G networks are being set up to accommodate the low latency communications needed for machine-to-machine communications and edge computing within plants.
The three technologies seeing the highest rate of adoption are cybersecurity, cloud and the Internet of Things.
On the use-case side, condition-based monitoring, over-the-air software updates, and remote and smart service are the top adopters, with predictive maintenance not far behind. Even with such high interest and activity, the adoption rate is only about 25 percent. That portends significant investment going forward and a stronger recovery post-COVID. The growth rate could layer on an additional 30 percent in smart manufacturing investment over what we had originally expected by 2025.
As economies reopen, the demand for manufactured goods will remain strong as companies work to fill back orders for products like cars and appliances. After months of stay-at-home orders during which businesses figured out how to operate without physically going into the plant, companies are shifting toward more cloud-based computing, automation and big-data analytics. They’re also moving supply chains closer to home and looking for alternative sources for raw materials and components.
Cybersecurity is becoming a greater concern. We’ve already seen many incidents of hackers trying to get into manufacturing technology, such as the malware attack that shut down a pure-play semiconductor company, and the white-hat hackers that took control of an entire network of wind turbines at a U.S. wind farm with a cellular module for remote access to programmable automation controllers.
The number of IoT devices could grow anywhere from three to 10 times the number existing today. And every device presents an exposure opportunity for hackers. At the same time, multinational manufacturers must stay current with country-specific regulatory and compliance requirements.
Manufacturers are responding to consumer demand for more connected products — connected cars, tractors, washing machines – pretty much anything that can have intelligence built into it. Companies are using analytics to understand that demand, and to shift from selling products to selling services that are personalized to customer preferences.
Smart manufacturing allows for more flexible, customized production set-ups, in many cases leveraging additive manufacturing solutions to deliver personalized products and improve the customer experience. At the core of these capabilities are the digital platforms and backbone: things like 5G network technology, things around the Internet of Things, cloud-based applications and systems, and automation and artificial intelligence, which will form the underpinnings of analytics used to optimize manufacturing operations.
Internal organizational functions are also becoming connected, with operations technology (OT) and IT in particular converging and becoming more connected than ever. IT is no longer exclusive to the CIO function, and is joining product development and operations in becoming product aligned. There is massive potential for consolidation between engineering and production, leading to improved speed and agility and new ecosystem engagement models.
What does all this mean?
One thing is clear: service providers should take note. Manufacturing companies will require partners that can help them implement and rapidly scale up smart manufacturing technology to reap the benefits. The more providers can help enterprises get the most from their current cost structures to fund this new digital investment, the greater the providers’ value-add.
David Lewis is a partner at ISG, a global technology research and advisory firm.