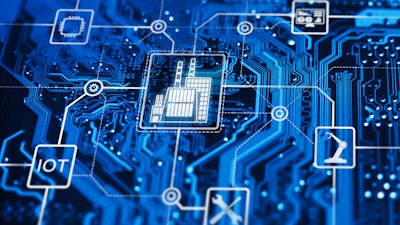
Industrial IT has seen many changes over the past decade, with IT/OT convergence, Industry 4.0, and increased digitization all shaping the way the production floor connects and interacts with IT. And while we’ve already seen a lot of transformation in the industrial sphere, it’s also clear that it’s not stopping any time soon: By 2025, the IIoT market will be worth $110.6 billion, and this will only further drive the digitization trends we’ve seen so far.
These trends over the next half a decade or so will pose new demands and challenges for the IT that supports industrial infrastructures. The OT environment increasingly needs to interface and connect with previously segregated networks. New data is being delivered by IIoT devices that needs to be processed, stored and analyzed. All of this means that IT in production environments will need to be scalable and flexible enough to support the new processes and functionality making their way into the infrastructure.
Here are the trends over the next few years that will play a significant role in how industrial IT will need to be adapted.
IT and OT Convergence
IT and OT convergence remains the biggest driving force for transformation in industrial IT. Previously modularized machines are now connected, and IoT sensors are delivering data about all aspects of production. It’s becoming clear that a siloed approach, as was the case previously, is no longer useful.
There are now far more interfaces and touchpoints between several different areas in manufacturing than previously, and this brings its own challenges. How can technicians and system administrators ensure that the interfaces are functioning? Is information flowing from the production floor to the data centers or the cloud as it should? And what is the best way to get an accurate overview of the entire picture?
These are all questions that professionals in industrial IT will need to ask themselves in the coming years.
Cybersecurity
According to many reports, the pandemic has led to a massive uptake in cyberattacks. Daniel Newman, writing on Forbes, claims that just in January to April of 2020, there was a 238 percent increase in attacks on banks and a 600 percent increase in attacks on cloud servers. This helps to highlight how the exponential growth of cyberattacks will continue to drive the trend of cybersecurity in all verticals, and that includes manufacturing.
While cybersecurity is nothing new to IT in industrial environments, digitization in manufacturing has brought about its own unique challenges. The IIoT sensors, devices, and implementations bring about security risks that have already been well documented. Meanwhile, OT components need to be “opened up” to connect with new systems and devices, and this provides a whole other set of security risks. The issue is compounded by the fact that standard security concepts and tools that were developed for IT do not necessarily work for OT.
With all this said: it is possible to connect the OT world, but a sound cybersecurity strategy is required, and the supporting IT will need to be adapted to meet the new demands of OT security and to secure IIoT components and devices.
The Industrial Wdge
Considering how important data coming from the production floor and IIoT devices is, industrial edge gateways (or smart gateways) have begun to play a pivotal role in manufacturing environments. Here is a description, taken from an article I wrote about this recently:
“These devices can be connected to various elements on the factory floor, and they are responsible for aggregating data and sending them to various end points. This means that they are the gateways – as the name suggests – to accessing important data about the production process.” Integrating these devices into the current infrastructure will continue to be a central theme for many companies in their move toward Industry 4.0.
Not only that, but ensuring that these gateways are connected, available, and running as they should be will be part of the task of monitoring the overall infrastructure.
Standardization of Protocols
With the interconnectedness of IoT sensors and devices with OT and other touchpoints, there is a need for a common “language” to ensure the components of different technologies communicate. The OPC UA standard is rising as a widely-adopted option – and this trend is expected to continue in the coming years. But whichever standard a manufacturer adopts, there will be a need to implement it and integrate it into the existing infrastructure.
Flexible Cloud
The trend toward multi-cloud architecture will continue, where services from multiple clouds are combined into one solution. Another trend is the usage of hybrid scenarios, where edge devices, on-premises hardware, and cloud services are combined into an integrated solution. It will be important for manufacturers to identify their requirements, and to design or select the best cloud solution based on their specific use-cases.
Processing and Analyzing Data
The nature of the IIoT means that there is data being generated by sensors, devices, and connected machinery. This data can be extremely useful in identifying trends, getting insights into the production process, and for making decisions.
Just as an example: gathering information about a machine’s operation using sensors can give you clues about when it will need to be maintained. This lets technicians perform predictive maintenance instead of maintaining the machine wholesale based on the calendar date, and thus saving unnecessary costs. However, that data needs to be collected, the insights it generates must be understood, and where necessary, alarms must be sent out when factors indicate that the machine needs servicing – when certain values exceed defined thresholds, for example.
The challenge is to identify what data is delivered and figure out how to use it. This understanding will also inform how the IIoT is implemented and is thus a crucial part of the puzzle.
With all the innovations and changes happening, the key is having the ability to adapt IT quickly and for it to scale accordingly as new requirements continue to shape manufacturing.