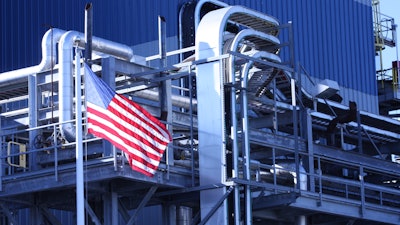
As far back as the 1980s, there was a great deal of public handwringing over a development that became known as the “hollowing out” of America’s economy. This meant that the country’s manufacturing sector was deteriorating because companies were opting to shift their production to low-wage factories overseas, leaving the nation without robust production capabilities while posing a threat to full employment.
That phenomenon was not unique to the United States. Japan and other developed countries also followed a similar shift of production to emerging countries where labor costs were a fraction of what was being paid at home. After reaching a peak of more than 19 million manufacturing jobs in 1979, the number of factory positions in the U.S. had declined to 12 million by 2013.
By the end of last year, it was 12.8 million. Most of those new jobs came from organic growth of facilities already based in the U.S., but some of them represented positions which were repatriated from overseas.
A New Normal
Much changed over this time. Productivity increased as did the use of computers and automation technologies. The new jobs that were created were different than the ones that were vacated. No longer is there a direct correlation between the number of workers and output.
In 1949, for example, 30 percent of America’s civilian workers outside of agriculture were in manufacturing; today that percentage stands at just 8.5 percent. This is about as low as it’s ever been, but the value of their output, in constant dollars, is far greater.
In farming, it is even more dramatic. During the 18th century, more than 90 percent of America’s residents were subsistence farmers. Today, farm workers represent less than three percent of the population, and their output is vastly greater.
There are several explanations. One is that the skill levels of workers in practically every industry are much higher today. Factory worker tools and workstations are far more advanced, frequently involving digital devices and novel software that were unknown to previous generations of workers. As a result, advanced manufacturing jobs typically require a different kind of employee – one with a college degree and superior technical skills.
Another explanation is that the mix of industries looking for labor keeps evolving. South Carolina is often held up as a poster child for that sort of change. In 1990, 40 percent of the state’s workers were employed in textile and apparel plants. Today, twice as many South Carolinians work in plants building cars, planes, and other transportation vehicles than work in textiles.
Although keeping an advanced manufacturing facility running smoothly requires skilled personnel, they are often difficult to recruit. But even with appropriate staffing in place, there is another important benefit to using robots, automation, and “smart” technologies – they have provided an ideal foundation to launch what is now referred to as the Fourth Industrial Revolution, or “Industry 4.0.”
With such a higher investment in technologies and the resulting performance improvements that have resulted, the cost of payroll in a manufacturing enterprise now represents a much smaller share of total production costs. Today, a highly automated, advanced manufacturing plant in the U.S. can be just as cost effective as those operating in other parts of the world. Not only that, if the products it manufactures are for domestic consumption, the cost of tariffs, transportation, and distribution will be lower as well.
The Coronavirus and a New Era of Nationalism
Fast forward to the first part of 2020, and a new set of conditions has further amplified a transition that had been building for years – the emergence of COVID-19. This virus has greatly impacted how to manage a global supply chain.
The resulting economic downturn then amplified the already increasing levels of nationalism that have been building across the globe. Not only has the U.S. been leading this charge, but many other countries have been quick to participate. One might argue that Brexit was driven in large part by the growing distrust of multinational financial, trade, and defense organizations.
The resurgence of nationalism has led to a spate of new policies, laws, and regulations designed to discourage companies from investing overseas and favor domestic industries. As a result, some major U.S. companies, including Apple, IBM, Ford, Sprint, and Lockheed Martin, have announced that they will be investing more in American facilities, and in some cases moving production back home from overseas.
Today might be the start of a boom in manufacturing in the U.S. This might even lead to new levels of prosperity once the coronavirus threat has been contained. Fortunately, new technologies are available to accelerate this anticipated reinvestment in U.S. manufacturing.
Based on what manufacturing software providers are seeing, such as iBASEt, investment in digital transformation has never been stronger. A strong digital footprint across all operations provides the necessary access to all the data involved in the production of every new product. With a digital representation – from cradle to grave – of how goods are manufactured, there is a significant potential for sustained quality improvement and cost reductions for many years to come.
This is good news for manufacturers. Smarter factors with intelligently trained workers can provide the necessary volume of goods and services to bring back manufacturing jobs to the U.S. – an outcome few thought possible just 20 years ago.
The efficiencies made possible by investing in new technologies should continue to grow with the further refinements and implementations of artificial intelligence (AI), digital platforms and ecosystems, as well as new digital products and services that transform production and operations on the shop floor. These advancements lay the foundation for further transformations in which US companies can shoulder a bigger piece of global production output without sacrificing efficiency, cost or quality.
Naveen Poonian is the CEO if iBASEt.