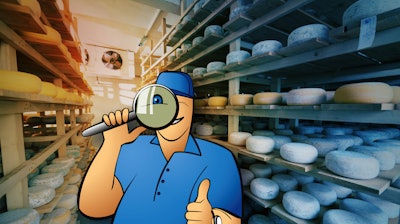
Traceability involves tracking every item and action in the supply chain to ensure there is a verifiable trail for everything. This sets an essential foundation for functions ranging from inventory and supply chain management to regulatory compliance.
In the case of compliance, traceability is a crucial prerequisite for operating in certain highly regulated markets, such as food and agriculture. In these markets, national, regional and international governing bodies impose stringent requirements that manufacturers need to adhere to in order to conduct business, with traceability often taking the top spot on the list.
As products may pass through the hands of dozens of people and intermediaries from their journey from raw materials to finished goods, things sometimes inevitably go wrong. Traceability enables companies to pinpoint where things went wrong if they discover quality or efficiency-related issues, and organize targeted product callbacks for the affected items.
Essential Traceability Functions for Food Manufacturers
- Lot and batch tracking: Tracking raw materials and products by unique identifiers such as lot or batch numbers is foundational for traceability and inventory management. Tracking by these unique identification number allows logging information on all processes, movements and operations an item or batch has passed.
- Shop floor control and internal reporting: Manufacturing processes and routing steps need to be logged, recording who performed the operation and when, allowing issues to be traced if necessary. Modern manufacturing ERP systems include per-worker production planning and tracking interfaces to enable this feature.
- Labeling and barcodes: Although manufacturing companies are increasingly turning to fully digital tracking systems, inventory items still need physical identifiers. Labeling and barcode systems help link physical products to digital records, improving inventory organization and traceability.
- Expiry tracking and FEFO: Product expiration has a great impact on the supply chain and tracking expiry dates ensures the timely processing of goods and identifying responsible parties if items go to waste. FEFO or First-Expired-First-Out inventory method ensures that the items that expire first are consumed first.
- Quality inspections and control: Regardless of the efficiency of the adopted inventory management or tracking system, employee training rates, or the level of organization of the shopfloor, mistakes still happen. Routine quality inspections is therefore the surest way to guarantee product quality. These should be logged and integrated into the traceability system to ensure consistent product safety.
Food Traceability Best Practices
Finally, let us take a look at 5 food traceability best practices that, when properly implemented, will help ensure your food manufacturing company stays compliant.
Rigorous employee training: While operating a work center might be relatively simple, all employees active in the food manufacturing process should also be fully trained on QA, product safety and traceability practices. Being well-versed in traceability requirements ensures that critical procedures do not go overlooked.
Transparent communication: No matter the tracking systems and technologies in place to meet regulations, company policy on transparency and open communication can play a big role in displaying an image of trustworthiness to vendors and consumers. Promote clear, open communication with suppliers and consumers to build trust and improve traceability.
Human-readable information: Meeting traceability requirements inevitably complicates the manufacturing process due to added steps in the workflow. Identifying and taking appropriate action on faulty items needs to be swift and accurate. Ensure traceability information is easily understandable to streamline processes and quickly address issues.
Prepare for callbacks and RMAs: When a faulty batch is identified that has already left your facility or problems arise with a product, it is the responsibility of the producer to handle the situation. And it pays off to be prepared. Have plans in place for product recalls or other disruptions to minimize damage to reputation and operations.
Use dedicated food traceability software: Manual tracking methods are inadequate for modern traceability needs. Dedicated traceability software or ERP solutions with integrated traceability functions are more efficient and cost-effective.
For example, MRPeasy is a flexible and affordable manufacturing ERP system that boasts full end-to-end traceability including automated reporting, a barcode system, version and quality control, RMA functionality and comprehensive serial number and lot tracking functions.
Learn more about MRPeasy by visiting https://www.mrpeasy.com/