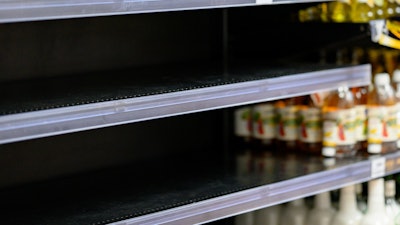
Over the past two years, the manufacturing industry has been hit by a succession of unforeseen circumstances, starting with COVID, moving through global shortages, and now being impacted by Russia’s invasion of Ukraine. Each of these has shaped the world of logistics, impairing the easy movement of supplies across the world.
The recent and continual tendency to disrupt the global supply chain has had huge consequences for the manufacturing industry, with its ability to process and produce being stunted over recent years. Toward the beginning of 2020, when the first major impacts of the pandemic were seen, production in leading countries plummeted, reaching almost ten-year lows.
Even with relative recovery from this low, the manufacturing industry as a whole is still struggling, with demand still exceeding production speed. Equally, there is still a fairly major materials shortage, putting further pressure on global manufacturing production lines.
How the Current Environment is Putting Pressure on Manufacturers
When creating an optimum build within the world of manufacturing, there are several different necessities that need to line up to give factories the best possible output. Some of these factors are controllable by the manufacturers themselves, while some come from relying on global supply chains.
Typically, there are four factors that contribute to an efficient manufacturing industry:
- Available resources
- Available demand
- Worker surplus
- Stable supply chain
Let’s break down how each of these comes into play and is currently being challenged.
Available Resources
At its core, the manufacturing industry is about transformation. The industry itself works as it converts raw materials into something else. Whether it be focusing on the production of electronics or the creation of food products, manufacturing takes available resources and transforms them into a working part, component, or whole, which can then be exported and sold.
To reach this final product and the main target of production, the manufacturing industry must have a plethora of available resources to use. When this is not the case, the industry simply cannot produce at scale, harming its output and further creating delays in the supply chain as a whole. With the range of global events currently occurring, the availability of resources is relatively low. In fact, when looking at raw materials like lumber, the availability has reached an all-time low as the supply chain has been consistently frustrated over the past 18 months.
Without available resources, manufacturing cannot create, derailing its high production and creating further problems down the line.
Available Demand
During the peak of the COVID-19 pandemic, consumers were actually flocking to stores and attempting to stock up on products. Due to this, there was a surge in demand, with the manufacturing industry seeing a high in May of 2021 that marked the highest level since July 2008. While this was the case during this particular moment of the pandemic, the sentiment has not continued, with current demand now actually falling.
In July of 2022, with major players around the world seeing inflation rates exceed anything that was previously forecast, the demand is currently plummeting. Even with this, the manufacturing input costs of obtaining all of the necessary resources are increasing.
These two figures, when put into conversation, mean that the manufacturing industry is spending more money to be able to make the same amount, or even less, of product that they normally do. Currently, with inflation continuing to rise, this means that the manufacturing industry is taking heavy losses, with this perfect storm of unforeseen consequences having a serious impact on the speed, cost, and profit of production.
Worker Surplus
A core part of the manufacturing industry is employing trained individuals that can operate the complex machinery and systems that producing entails. Alongside the economic impacts of COVID and recent wartime events, there have also been major social impacts. One of these was the mass movement away from work, with workers around the globe wanting remote working situations.
After the first wage of COVID, and then the second, third, and fourth, worker shortages spiked, with people quitting their jobs within the manufacturing industry to look for a safer industry with less person-person contact.
Alongside this, the Great Resignation, where more people understand the true value of their labor and gravitate away from industries that try to underpay them, has also led to major problems within manufacturing.
Without a surplus of workers, with many major manufacturing companies still not wanting to raise wages to keep their workers, there has been a shift in how effective this industry can be. As material shortages and staff shortages increase, this industry simply cannot function as it once did, further feeding into the downward spiral that manufacturing is experiencing.
Stable Supply Chain
In June of 2021, The White House released a thorough report on the current impacts of the pandemic on the global supply chain, focusing on how COVID-19 had disrupted specific industries. Out of all industries measured, the one that was impacted the most was manufacturing, with nearly 60 percent of all suppliers suffering delays.
These delays are a culmination of the lack of the above three factors, with manufacturing plants simply not being able to produce at the rate they once did. Whether that be from a lack of staff or a lack of resources, or the inability to replace specific parts of a broken machine, these factors all lead to a knock-on effect within the manufacturing industry as a whole.
The disruption of the supply chain cuts to the core of everything that manufacturing needs - fluid logistics on a global scale. Without a stable supply chain, the manufacturing industry simply cannot produce, export, ship, or engage in any part of the vital logistical element of their businesses.
With this in mind, it’s no wonder that prices have soared in recent months, with global shortages further leading to businesses having a harder time operating.
The Perfect Storm
Due to the lack of a stable supply chain, the worker crisis, the lack of resources, and a plummeting demand, it’s no surprise to see that manufacturing companies around the globe have started to downgrade their future revenue predictions. Even the International Monetary Fund has decreased the predicted growth beyond 2023 to -3.3%, demonstrating how these economic and environmental conditions really are impacting everyone.
This is seen all over the world when dealing with manufacturing, with the VDMA (a German manufacturing company responsible for huge parts of their manufacturing industry) decreasing its forecasted growth from 7% to 4%. Equally, the whole of China’s manufacturing industry - a huge global player - has had significant issues with rising costs, bottlenecks, and the rationing of electricity.
In fact, the cost of raw materials in China rose to 63.5 from 61.3 just a month before back in 2020, representing a huge increase in the general cost to produce items within this industry. This cry is heard around the world, with countries everywhere from The Americas and Asia to Europe and beyond seeing a growing set of problems within the manufacturing industry.
The Current Issue with Financing
In 2022, some of the leading countries when it comes to global manufacturing have suffered huge economic downturns, with the increasing inflation in each country leading to further issues for businesses. Alongside the rising price of raw materials, the increase in inflation has also led to financing issues for businesses.
When a business wants to borrow money, as is the case with many major manufacturers during this difficult time, they often turn directly to banks for financing. Rising inflation dramatically impacts the ability of businesses to find effective financing, as businesses get a much worse deal than they would have with more stable rates.
Considering that the United States of America is currently facing the worst inflation in nearly 40 years, it’s no wonder that many doors of opportunity are rapidly shutting when it comes to bank financing.
The manufacturing industry has specific loans, with businesses that work within this industry being able to borrow capital to fund any major purchases, like machinery that would fuel growth. Typically, equipment loans are up to seven years, but this is currently being called into question with rising interest rates.
Due to the rapid shift in global economic circumstances, many companies that were once offering loans directly to players within the world of manufacturing are now no longer operational. There are only very few services that are still actively offering loans to this industry, meaning its much harder for new and developing businesses to continue to grow without this monetary support.
With no option for banks and a limited number of manufacturing-specific options, people don’t know where to turn.
The International Economy Outlook and Its Oncoming Recession
To add fuel to the fire, the word ‘recession’ has been thrown around a lot over previous months. Technically, a recession is the name for a period of time over which a country experiences two-quarters of negative growth. On July 28th, the United States will announce their second-quarter figures, with many banks and major economic-based newspapers already predicting a second negative quarter.
A recession is very bad news for the manufacturing industry, and this is one of the core fields that is always impacted the most by the economic and social conditions of a recession. During recession periods, there is typically a decline in the GDP of the given country, resulting in a loss of business for both small and large companies. Equally, there are typically huge layoffs to cover the higher cost of spending.
While manufacturing won’t be impacted quite as badly as something like retailers, this is still one of the industries that is most directly affected by a recession. Typically, manufacturers will face too much inventory without enough demand, a loss of workers, and a stagnant supply chain which will only further the disasters already happening to this industry.
With a recession, the manufacturing industry will see a snowball effect of all the previous negative impacts of COVID and the war in Ukraine. Over the next 6 months, we’ll see huge swings in this industry. As manufacturing loses money and stalls production, every other industry is equally impacted, with the products that suddenly aren’t being produced creating a huge deceleration in everything from retail to construction.
How to Cut Back and Prepare For a Hard Environment
The only silver lining to the oncoming recession if you’re working within the manufacturing industry is the fact that the manufacturing industry is also one of the fastest to recover. As so many other industries rely on manufacturing, it is often the central focus, with many other industries and governments turning to bolster their return to high-production capacities.
That said, if you’re working in the manufacturing industry and are looking for a few ways to prepare for the oncoming disasters, then we’d suggest:
- Make Capital Investments Early. Increasing productivity in your manufacturing plant is one of the most effective ways of keeping production high during difficult periods. To do this, you should aim to find a manufacturing financier that will help you to get the equipment you need ahead of time.
- Increase Cash Flow. Manufacturing companies that have more available cash are able to mobilize toward growth. By creating as much available cash as possible leading up to a recession, a manufacturing company has more flexibility in their approach.
- Stockpile. While stockpiling is fairly unheard of in manufacturing, with the Just in Time approach being incredibly common, we implore you to obtain a few critical spare parts to your operations. With a slower supply chain, it’s always better to have core spare parts that will help your machines to stay healthy during long periods without access to replacements.
By combining these three approaches, you’ll be much better suited to prevent your manufacturing business from suffering the worst of the recession.
While the world is not favorable for production right now, this is certainly not the first difficult period and won’t be the last. The more prepared your business is, the more likely you’ll be to sail through the recession and any other future circumstances that may arrive. If the past two years have taught us anything, it’s that we now live in a world where unprecedented circumstances in the manufacturing industry aren’t an uncommon event anymore - preparation is now more vital than ever.