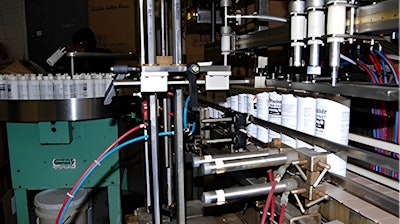
Bernard Laboratories is a family-owned contract manufacturing company from Cincinnati, Ohio that produces industrial chemical products such as lubricants and sealants. They either make the product from scratch, or receive a large batch of the product from the client and package it in retail containers.
Founded in 1948, its current owners are the 3rd generation to manage the operation, running a global company with 22 full-time employees.
When Covid hit, Bernard Labs had to find a way for some of the employees to work from home. Their on-premise legacy ERP system became an obstacle in this, with the company having to rely on emails to collaborate remotely.
MRPeasy
Piper started looking into the cloud MRP/ERP solutions by reading reviews on software selection sites. After shortlisting a couple of options and making use of their free trials, Piper felt comfortable moving forward with MRPeasy.
“What I like about MRPeasy is how easy it is,” she says. “It didn’t feel overwhelming and seemed easy enough to learn on my own and pass the knowledge on to our other staff members. And the affordability of the software played a role in the final choice as well.”
Implementation commenced in October 2020 with migrating data from the old ERP system to MRPeasy. After running the old system side by side with the new one for a few months, they finally switched off the legacy software in October 2021.
Although the new software is easy to use, it is not easy to implement changes in a business with employees that have worked in the company for decades and are deeply set in their ways. Instead of forcing the change on senior staff members, Bernard Laboratories decided to hire a new office administrator who became the primary user of the new software.
“As senior employees have retired and new ones have come in, resistance has become less of an issue,” Piper states.
Software Aids in Standardizing Documentation and ProcessesThe first priority during the implementation was purchasing. Previously, the two buyers created purchase orders manually. There was no PO standard nor was there any consistency in the purchasing process as a whole. The same applied for the quotes and invoices created by the sales department. MRPeasy brought about a quick standardization of those processes and documents.
“Now all of our orders and invoices look professional, which was not the case before,” Piper says.
Another module that the company is now using heavily is manufacturing order management. In addition, soon after implementing MRPeasy, Bernard Laboratories also adopted the accounting system QuickBooks, taking advantage of the native integration between the two systems.
“The QuickBooks integration is very important as it gives us confidence that the information flowing to finance is correct,” Piper says. “The combination acts as a system of checks and balances that we can trust.”
Administrative Overhead Reduced by Two SalariesPiper is happy with how everything is recorded and easily found in MRPeasy. In addition, the software collects, processes, and visualizes valuable data that can be used to make informed business decisions.
“You can’t achieve this level of efficiency with spreadsheets,” she says. “Everything is linked together so you can find the piece of data you’re looking for by using various criteria.”
With the new software, the company was also able to significantly reduce their administrative overhead. When three senior office employees retired, they backfilled with one. This was a large saving for a company their size.
“We have definitely grown thanks to MRPeasy,” Piper states. “We are now able to fulfill more orders, generate more revenue, and have an accurate overview of everything.”
Although change can be daunting, Piper advises other small manufacturers that have not yet made the leap to MRP software to try out a few products and see for themselves how easy and effective it can actually be.
“We implemented MRPeasy to deal with small inefficiencies but little did we know that it would drastically reduce the time we spend on administrative tasks,” she says.
For more information, visit www.mrpeasy.com.