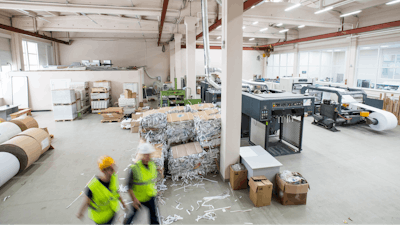
The cost of noncompliance in manufacturing doesn't affect just one performance area. It affects everything. If you're consistently failing inspections, receiving citations, missing deadlines, and dealing with incidents, it's time to consider overhauling your processes.
When you weigh the cost of EHS software, PPE, more staff, etc., against the resources lost to fines and inefficiencies, it's easier to invest in better EHS performance. Here are some of the most common ways noncompliance might increase costs at your facility.
Incidents and Injuries
The most obvious cost of noncompliance is its impact on incident rates. Regulatory standards are there to protect workers from health and safety risks. If you don't follow them, your employees are more likely to get injured, damage property, etc.
A single workplace injury can cost, on average, anywhere between $1,040 and $40,000, depending on whether it requires medical consultation. How many incidents do you have each year? Do you track near misses so you can prevent recordables? Can employees report hazards, and if so, does your team follow up on those reports?
Aside from the tangible costs of safety incidents, consider the cost of noncompliance on your EHS team. Disorganization, poor communication, missed KPIS—all these can decrease motivation and job satisfaction within the safety department. Meeting compliance standards is just a small step towards EHS excellence. If you want to build an effective safety team, you must start with the basics.
Employee Turnover
Another hidden cost of noncompliance is the effect it has on employee turnover. Chances are, if you're struggling with compliance, you don't have much time for employee engagement. You might not realize it, but workforce retention can greatly impact safety.
Think about it. When you hire new employees, your facility's total risk level increases. New workers have a learning curve and are more prone to costly mistakes. Plus, they don't have established safety behaviors yet. This means that keeping the seasoned employees you have is critical for reducing safety risks over time.
Training and Onboarding
Workers are more likely to miss training deadlines if you don't keep detailed training records. This means you spend more time and money doing full process retraining when a simple refresher course would have worked. Failure to comply with recordkeeping standards increases your team's oversights.
To avoid these costs, start by looking at your documentation process. Ask yourself these questions:
- Do we have a standard way of naming documents?
- How easily can I find a report when I need it?
- How long does it take for us to complete a report or investigation?
- Do employees use the same forms, checklists, etc., for each incident?
Often, noncompliance stems from poor records management practices. If you can improve documentation, you'll miss fewer training deadlines and ultimately spend less time and money on this area of compliance.
Quality of Outputs
Don't overlook the connection that exists between safety and quality. Sometimes, the cost of noncompliance is a major quality issue that slips through the cracks, negatively affecting your company's reputation. If you don't have standards in place for health and safety, then your processes are more likely to produce quality errors.
For example, what if your team doesn't inspect heavy equipment before each use? Well, operators have a higher chance of injury. Also, you might miss issues like excessive dirt, misalignments, etc., that affect the quality of the finished product. Quality can cost you a lot when it comes to public and investor relations. Lost revenue, employee strikes, environmental incidents, and more are some major repercussions of poor QA systems.
You'll find that many regulatory requirements align with your facility's quality goals. The better you follow these guidelines, the more proactively you can find and fix quality problems before they affect your downstream stakeholders like distributors or consumers.
Production Delays
When you fail an audit or inspection, the regulatory agency might require you to correct an error before resuming production. This is on top of the potential fines you might receive. The total cost of an unplanned shutdown is dependent on factors such as:
- Time of year: Is it your peak production season or the off season?
- Specific process: Does the issue directly or indirectly affect output?
- Type of issue: How long will the issue take your team to fix?
Don't forget the lasting effects of a production shutdown. Even if it's only for a short time, a stoppage can pull workers out of their flow state and decrease productivity once the system's back up and running. When you're in compliance, you won't worry about potential delays and project setbacks. Instead, you can focus on improving efficiency and perfecting your quality assurance process.
Avoiding Noncompliance Costs
In manufacturing, the cost of noncompliance is hard to quantify. Citations and fines are just the tip of the iceberg. Improving performance and reducing cost begins with the basics.
The most important areas of EHS management to address are:
- Safety communication: How do you notify employees and contractors about new requirements, safety concerns, and regulatory changes?
- Documentation and recordkeeping: What's your standard process for creating and maintaining accurate compliance records?
- Action tracking: How do you ensure that your team stays on top of action items and regulatory deadlines?
- Change management: What's your process for managing operational changes and preventing process safety incidents?
Start improving these processes, and compliance will become more manageable. With the right changes, you can even tackle multiple problems at once. The trick is to follow up on any of the changes you make to see if they're actually effective. Just because you roll out a new safety initiative or require more safety checks doesn't mean they'll happen or work.
Regulations are always changing and so are your team's needs. The more adaptable you are to these circumstances and the more you audit your internal processes, the fewer noncompliance costs you'll suffer in the future.