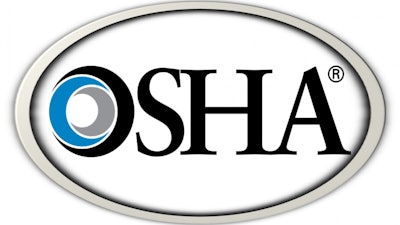
In January the Occupational Safety and Health Administration (OSHA) updated its fine amounts by eight percent, bringing maximum penalty amounts for serious and other-than-serious violations to $15,625. In contrast, fines maxed out at $7,000 in 2015. I recently had a chance to discuss this increase, the potential impact, and the debate over OSHA’s ongoing effectiveness in policing industrial safety with a former OSHA employee.
Jeff Reinke, editorial director: How much of an effect will these 2023 OSHA fine increases have? Will the size of the company play a role?
Drew Youpel, Head of Risk Control for Foresight: These fines will have a tremendous impact on companies that are inspected and fined by OSHA, especially considering OSHA fines are not covered by any insurance product, and are paid directly from the finances of the company.
When considering smaller companies, these increased fines can have an even more serious impact on cash flow. These latest increases make it even more important for companies big and small to carefully review and abide by the latest OSHA policies, and ensure they are conducting the latest OSHA or Cal/OSHA required safety and health standards. And not just from a financial standpoint, but from a moral standpoint.
Even when a company is trying to do all the right things, it’s still sometimes difficult to have all the correct information and comply with all of OSHA’s required actions. So, smaller companies with less staff often have a harder time meeting compliance demands and keeping up with paperwork and protocols. Not to mention, smaller companies also often lack the resources to fight any OSHA citations that may come their way, unlike larger companies.
On the other hand, larger companies have more employees and, in-theory, more risk, but it’s important to note that as companies get larger, and the risk in the field grows, so does a company’s revenue and their ability to hire in-house safety and risk professionals to focus on OSHA-related concerns.
JR: We often see significant fines reduced after an appeal is filed. What can you share about that process and best practices for utilizing it when faced with larger fine amounts?
DY: This process of appealing a fine is called the “informal conference”. The informal conference option is offered to the company that has received citations to come to an agreement with OSHA, as opposed to going to court. There are advantages for both parties in this scenario. The informal conference gives both parties the ability to review the case and the alleged violations and come to an agreement.
My advice to any company that is cited by OSHA, and may have questions about their citation, would be to schedule the informal conference as soon as you can. This gives the company the ability to hear the evidence OSHA is using to draft the alleged violations.
A company has 15 days to set a meeting with OSHA and conduct the Informal conference. If you conduct that meeting within seven days of receiving the citations, you can hear the evidence that exists in the case and think about the decision. If you wait until the end of the 15 days, you are not giving yourself ample time to make an informed decision.
Once in the informal conference, take notes and request any information that you do not have from OSHA. If a company finds themselves in this aforementioned scenario, it also makes sense to discuss your options with an experienced individual.
JR: I’ve personally been critical of OSHA for not having enough teeth in enforcing its standards, as the violators paint the wrong picture of 99 percent of U.S. manufacturing that’s doing things safely. What do you think can be done to help OSHA serve as a greater deterrent, and hopefully help reduce the number of repeat offenses?
DY: For OSHA to be more of an effective deterrent, I firmly believe that the agency needs more funding. For OSHA to have more of an impact, the agency needs to expand their capacity for inspections and enforcement.
More funding would mean OSHA could expand their workforce and increase their bandwidth for enforcement. Companies are aware the agency is short-staffed, so they’re not as concerned about receiving an inspection or citation from OSHA. More funding, be it from the federal government or re-evaluating broad-brush fines for larger employers (for example, increasing fines for larger employers based on financial revenue instead of just number of employees), would be the most effective way, in my opinion, for OSHA to strengthen its enforcement presence as a deterrent.
JR: Has OSHA ever considered scaling fines according to company size? Amazon’s recent $60,000 in OSHA fines doesn’t feel like a deterrent, but that same amount could put a smaller manufacturer in danger of closing the doors.
DY: OSHA uses the size of the company to offer reductions in penalty amounts. For context, the bullets below show what one citation could cost a company based on size:
- 1-10 employees; $4,687.50
- 11-25 employees; $6,250.00
- 26-100 employees; $10,937.50
- 101-250 employees; $14,062.50
- 251 or more employees; $15,625.00
Looking at the Amazon citations and information, it appears the maximum penalty amount was levied against Amazon. It also appears the “General Duty Clause” was used to cite Amazon for Musculoskeletal Exposures. OSHA currently does not have an ergonomic standard to enforce, but in the ergonomic standards FAQ page on their website, OSHA says they will “conduct inspections for ergonomic hazards and issue citations under the General Duty Clause and issue ergonomic hazard alert letters, when appropriate.”
Profitability of an organization has never been a factor for OSHA citation amounts.
JR: How do you feel OSHA has responded to the understandable lapse in inspections that took place during the pandemic?
DY: The first table on this page of the OSHA website shows inspection totals by year, and highlights the impact that the COVID-19 pandemic had on OSHA enforcement during 2020 and 2021. As expected, OSHA’s inspection frequency was most definitely reduced due to the pandemic. From a quantity perspective, I do not expect OSHA to attempt to backfill the delta that exists in the lack of enforcement actions due to COVID.
One of the main challenges I believe is preventing the agency from “catching up” on inspections and enforcement is the limited workforce that exists at OSHA. When individuals hear OSHA, we visualize a government agency that has massive resources, but the Federal umbrella of OSHA is a small agency; with state partners there are approximately 1,850 inspectors responsible for the health and safety of 130 million workers, employed at more than eight million worksites around the nation — which translates to about one compliance officer for every 70,000 workers.
JR: Will some industries be impacted by the fine increases more than others?
DY: OSHA has specific areas of concern based on historical injuries and fatalities. Types of work that have been reviewed and designated by OSHA as having higher than average rates of injuries and fatal accidents are grouped into two categories: National Enforcement Programs (NEPs) and Local Enforcement Programs (LEPs). From an enforcement perspective, any business that falls into either of those categories, or conducts those types of work, has a better chance of receiving a visit from OSHA, and in-turn could be more impacted by the latest fine increases.
OSHA looks to enforce the laws that exist in the Code of Federal Regulations IE. CFR. These laws exist in the OSHA regulatory text and lay out the required minimum safety standards employers must provide to employees to ensure a safe and healthful work environment. In order to deter companies from failing to comply with these regulations, the citations and monetary amounts were raised with reference to the link above.
A great safety and compliance resource, no matter the industry, is a company’s insurance broker, and their workers’ compensation insurance carrier. Most companies have a guaranteed cost or deductible program in which employee injuries are covered, so a company’s brokers and workers’ comp carriers should have resources to guide an employer in the OSHA landscape.
At Foresight and Safesite, guiding our clients through OSHA compliance and the violation process is a big part of what we do.