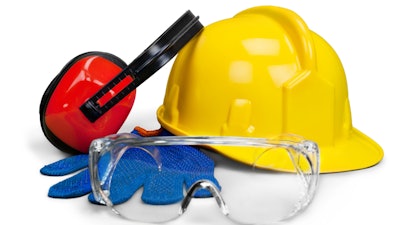
Safety culture, for many safety professionals, is a system.
The system consists of attitudes, beliefs, values and principles that encourage safe behavior in the workplace. All the moving parts need to come together to upkeep this system. The pieces of safety culture include management and employee involvement, hazard analysis, control and abatement, communication and training, and evaluation. Each of these steps is necessary and needed to create and upkeep a safe work environment.
The first element of safety culture is management involvement. This includes practicing safe behaviors and demonstrating involvement. Management can demonstrate involvement by doing things like spending time in teams and empowering workers to create safety procedures and policies for the organization. Management can also be a role model in a safety system by allocating resources, such as personnel and money, to improve the safety of employees in the construction site.
Another element of safety culture is employee involvement. There is no safety culture in an organization without the participation of its employees. Employees become owners of the safety culture when they participate in the occupational safety and health initiatives of their organization. Safety and health initiatives are pivotal in establishing a culture.
The objectives of these initiatives are to raise the employees’ awareness on existing hazards, promote employee engagement, make the work processes more efficient and reduce the number of incidents in the workplace. There are several ways to engage employees with a safety culture. One way to encourage employee involvement would be to involve employees in the development of a new training course on the use of respirators.
Before instigating any safety initiative, worksite hazard analysis is essential. Management must identify current and future threats in the workplace, such as fall, fire, electrical, and chemical hazards. Analysis takes place at the largest and smallest of levels. The work hazard analysis breaks every process down into specific components. It then identifies the health and safety hazards of each component. If health and safety hazards are not identified and analyzed, there is no way to protect employees or create a secure worksite.
The next step in maintaining a safe culture is hazard control and abatement. This takes place after the work hazard analysis. Management, with the assistance of safety professionals, will attempt to eliminate hazards. They will use methods such as substitution, in which one hazardous material is replaced with another safer material (ex: paint with lead is now substituted with paint without lead).
Methods could also include engineering controls, such as enclosing or isolating a hazardous process (ex: x-ray machine), or changing the initial design of a machine. If management fails to eliminate the hazards, the next step would be to use work practice controls to reduce the hazards. These controls could include strategies such as the wet method (water to suppress the dust in demolitions), job rotation (every six months a different task for the worker), good personal hygiene, proper housekeeping or machine maintenance.
The last step of the hazard control and abatement process is the use of personal protective equipment such as safety glasses, respirators and gloves.
An important part of the safety system is communication and training. An employer must provide employees information about the existing and anticipated hazards in the workplace. This should be accompanied by the organization’s policies and procedures, regulations and safety objectives. Examples of effective communication methods are orientation manuals, task and procedure instructions, general safety courses, equipment manuals, signage and safety meetings.
Communication with the employees is vital; it creates safety awareness while reinforcing safe behaviors and demonstrating that management is committed to the wellbeing of its employees. Additionally, employers must provide employees with the appropriate training before they assign them a certain task. This specific training will enable workers to recognize hazards, and teach them ways to eliminate or abate these threats.
There are several methods for delivering this safety training: lecture method in a classroom environment, e-learning, hands-on training, safety meetings, or equipment simulators. Training should be provided every time an employee is introduced to a new task, or any time the employee is working in an unsafe manner.
The last element in a safety culture is the evaluation of performance, along with a reward system. An organization first should identify the minimum requirements for a safe and healthy workplace. Subsequently, an organization must measure its performance -- usually every year -- at the beginning of a period and at the end of the period. Doing this measures the actual performance of the organization against the minimum required targets.
The objective of this step is to identify weaknesses within an organization. It is also used to evaluate the effectiveness of previously implemented policies and procedures. As with any evaluation, the goal is that there is change and improvement to the organization’s safety culture. This performance evaluation method should be complemented with a reward system that provides employees feedback regarding their performance. The reward system should recognize those who practice and promote safe behavior in their workplace.
To conclude, safety culture is something that evolves. The safety culture of an organization will be influenced and altered by the beliefs of new management, implementation of new safety regulations, introduction of innovative materials and equipment, and medical findings that identify previously unknown hazards. However, following these steps in maintaining a safety culture can keep a workplace free of hazards, and create a safe and secure environment for all employers and employees.
Harry Xanthakos holds an MBA, is a Certified Safety Professional, is an OSHA outreach trainer for construction and general industry, as well as the founder of Atlas Safety & Health.