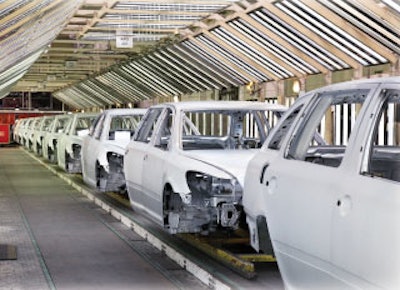
This article first appeared in IMPO's November/December 2012 issue.
According to the United States Department of Labor, slips, trips, and falls constitute the majority of industrial accidents. Additionally, the National Safety Council estimates that these accidents cost employers more than $70 billion per year in workers’ compensation, medical costs, and diminished productivity. Industrial plant managers and operators should remain aware of the devastating impact these accidents can have on the victim and the plant. While not every industrial accident is completely preventable, many of the causes of slip-and-fall accidents can be offset through the implementation of a safe floor matting system.
The Importance of Matting
Frequently, plant safety initiatives will address one cause of accidents by reacting to a specific hazard (e.g. a water leak or stray box), instead of proactively placing focus on more comprehensive prevention methods. Often, this reactive approach does not completely solve safety issues in the plant. To resolve slip-and-fall concerns, plant managers can implement matting systems to limit these largely avoidable accidents. A safe floor matting system works to prevent slip-and-fall accidents by reducing the spread of slippery substances, improving floor traction, and boosting overall plant cleanliness.
As a first step in developing a safe floor matting program, plant operators must first assess the plant layout to determine where matting will be most beneficial. Dividing the facility into zones based on area usage, traffic patterns, and contaminant types will help to create the most effective safety matting program. Consider the following zones:
- High traffic: These are areas in the plant where employees are constantly moving or transporting materials (corridors, restrooms, break areas, etc.) and should always be fully matted to increase safety. The high volume of liquids in these areas requires matting to quickly capture substances and prevent their spread throughout the plant. Frequently, oils and solvents from machinery will fall during production processes and create a slippery environment for employees. Additionally, employees tend to move quickly in these areas, so matting provides added traction to prevent against slip-and-fall accidents.
- Productivity: Productivity zones include plant areas where most manufacturing duties take place. Often, employees will spend most of their time in productivity zones, so this can be a critical opportunity for the role of matting in accident prevention and improving employee comfort. To properly assess matting needs in these areas, plant managers should observe the plant throughout the day to determine employee foot traffic and movement patterns.
- High risk: Areas that serve as transitional walkways from the manufacturing floor into management offices or break rooms are priority matting zones. Frequently, plant managers walk back and forth from the production floor into offices, tracking in liquids, dust, and solvents. Maintaining cleanliness in the plant offices is vital, as this is typically where potential business partners and customers meet.
- Entryways: Delivery entrances, loading docks, back doors, and front entryways are common locations for industrial slip-and-fall accidents. Inclement weather such as rain, sleet, and snow can cause the tracking of water and debris into the plant, and thus contribute to accidents. Matting in these areas effectively prevents the spread of outside water and debris into the facility. Matting at entryways also prevents the spread of hazardous manufacturing soils from the plant floor to outside work areas.
Matting needs will vary widely depending on the types of chemicals and machinery used in the production process. Personnel count will also influence matting selection and cleaning frequencies. After conducting a complete assessment of matting zones throughout the plant, managers must then select matting according to the needs of each area and the facility as a whole.
Types of Industrial Matting
Different matting types can leverage their individual strengths to eliminate accidents. The most common types are:
- Scraper: Scraper matting removes debris from shoes at entrances and transitional walkways. Areas with heavy contaminant levels require heavy-duty scraper mats to effectively capture all debris and liquids. Rough edges and high ridges on scraper mats quickly remove particulates from shoes and effectively contain liquids. Typically, scraper mats are most beneficial for catching and removing contaminants when used in combination with carpet matting.
- Carpet: Carpet matting is an important barrier that prevents the spread of liquids and solvents around the plant. Fibers in carpet matting quickly absorb and contain any liquids that may have leaked or transferred to shoes. Carpet matting also captures common manufacturing debris such as sawdust, dirt, and metal shavings. Carpet matting including suction-cup backing will stay flat in areas with high levels of activity from rollers and vehicles. These mats should be placed at entryways and in transitional walkways and hallways throughout the facility. It is crucial to place 10 foot-long mats at entrances so employees can walk on matting for at least three steps to remove all contaminants and moisture.
- Anti-fatigue: Anti-fatigue matting is important in productivity zones and areas in which employees spend the majority of their workday. Anti-fatigue matting works to reduce bodily strain and discomfort during long shifts. Added comfort from anti-fatigue mats can reduce workers’ compensation claims and increase everyday productivity. Additionally, this type of matting will often feature anti-shock properties to reduce potential electrical current transfer from plant equipment.
- Drainage mats: Drainage matting is highly effective in containing liquids and solvents that may spill from manufacturing equipment. These thick mats with large holes capture liquids and remove moisture contact points between shoes and spilled substances. Another benefit of drainage matting is that it can capture any solid items such as screws, bolts, or knobs that may fall during busy production periods. Large ridges on the mats also provide added traction in productivity and high-traffic areas throughout the plant.
Increasing Matting Effectiveness
While matting type and zone placement is key in the prevention of accidents, there are some additional factors that must be considered. Often, poorly-maintained matting will tear or curl at the edges which can ultimately increase the likelihood of an accident. It is also possible for saturated industrial matting that is not regularly laundered to cause an inkpad effect. The inkpad effect will transfer captured contaminants back onto employee shoes, potentially increasing the likelihood of slip-and-fall accidents. Regularly cleaning and switching out mats ensures their effectiveness in reducing accidents and boosting plant cleanliness.
Additionally, to protect flooring throughout the plant and increase matting effectiveness, plant managers should use matting in conjunction with a general cleaning program. Creating daily cleaning protocols that use industrial strength floor cleaners and ensures that plant flooring contaminants remain at a minimum. By combining these protocols with a comprehensive matting system, plant managers can keep employees safe and operations running smoothly.
Overall plant safety should be a top priority and an ongoing process involving all management and production employees. While the implementation of a safe matting program takes time and energy, it is a critical piece of the safety equation.