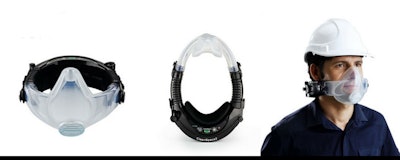
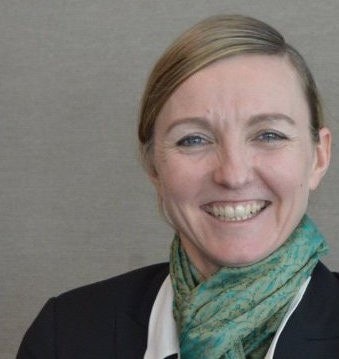
It’s estimated that more than 5 million workers are required to wear respirators in the United States to protect them from harmful dust, smoke, gases, chemicals and more. With so many different respirators out on the market, manufacturers need to consider a variety of factors before selecting the right equipment.
Alex Birrell, CEO of CleanSpace Technology — a global manufacturer of innovative industrial, welding, healthcare, mining, energy and laboratory/research powered respiratory protection — offers insight into how respiratory device technology has changed over the years and key things to keep in mind before selecting your next PPE.
IMPO: Can one type of respirator be used in all situations? What factors should be taken into consideration when deciding on the best respirator for a manufacturing or industrial environment?
Alex Birrell: Work place respiratory protection is the most technically complex of the personal protective equipment (PPE) category. A growing knowledge and awareness of the acute (asthma) and long term (silicosis, asbestos, COPD, cancer) consequences of exposure to common materials (hard rock, asbestos, lead, coal) is driving companies and employees to install and use respiratory equipment.
The difficulty is that there are many elements that affect the correct choice of respiratory equipment: Form (dust or gas), toxicity and concentration of contaminants, exposure times, tasks being undertaken and adjunct risks such as potential for lack of oxygen (confined space) or explosive/flammable agents. And almost every site or operation can vary.
When it comes to respiratory equipment, one device does not fit all. Respiratory devices have to be designed and NIOSH/CDC tested to ensure the device protects the wearer. Below is a summary of the common respirator categories and indicative use.
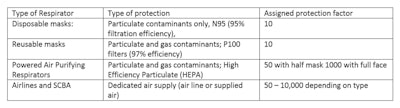
So which respirator do you use and how do you train your team so you can ensure they are protected? It is complex. And your employees’ health, sites’ productivity and business costs are impacted by poor choices in equipment. When considering or re-evaluating respiratory protection, always seek expert advice and recommendations from a safety or respiratory protection specialist. A risk assessment will identify the type and level of protection required. Done well, businesses can be OSHA compliant, improve the efficiency of their operations and save direct and long term costs.
IMPO: What advancements have you seen in respiratory mask designs and/or technologies over the last 5-6 years?
Birrell: There has been little change or innovation in respiratory protection in over 25 years. The costs and risks in developing, testing and approving new respiratory equipment has been a major deterrent for innovation. Despite the advances in medical electronics, materials and power technology, respirator manufacturers have not incorporated these into their designs. You would assume that respiratory protection designs must be pretty good but the fact is that these traditional designs still attract wearer and employer complaints: disposable masks offer the lowest fit factors, are uncomfortable and cause fogging to eyewear; PAPRs can provide higher fit protection factors but are heavy, cumbersome and have high running costs.
These major complaints about the usability have only driven minor incremental improvements to harnesses and exhalation valves. Unsurprisingly these modest changes have not resolved the issues with breathability/heat/fogging, weight and usage complexity remain huge barriers to adoption and compliance for employers. And it is not their fault! As manufacturers have grown to dominate the safety market and expanded globally, their ability to focus on product development and remain ‘specialists’ becomes harder as acquisitions have diluted their focus. Standards bodies such as OSHA and NIOSH remain committed to raising the level of workplace standards (Crystaline Silica regulations Sept 2017). The respiratory protection industry is well over due for new products.
CleanSpace is a game changer in respiratory protection. The proprietary technology AirSensit platform has created the world’s smallest powered respirator. CleanSpace Respirators have no hoses, cables or belt mounted battery packs. The design of our Powered Air-Purifying Respirators (PAPRs) creates a super light, compact system that is compatible with other PPE and provides full mobility and portability for workers. The PAPR provides up to 220L/min of air and 8 hours of operating time. The simple and intuitive CleanSpace respiratory systems deliver worker compliance, productivity and cost management.
IMPO: The Respiratory Protection Standard is often one of the Top 10 violations most frequently cited by OSHA following inspections. What do you see as a common issue for non-compliance by workers or companies (comfort, cost, etc…)?
Birrell: In an ideal working environment, workers would experience high protection and complete comfort when working. Employers would have an OSHA compliant, deployable, low maintenance device that improved productivity. The reality is that traditional respirators do not deliver on many of these. Furthermore, masks compete rather than compliment other work equipment (hard hats, tool belts, safety eye glasses, earmuffs, jackets). The major contributors to non-compliance are:
- Poor choice of respiratory equipment
- Not undertaking a site assessment (workplace hazards and levels, location, storage) and advice from a respiratory specialist (CIH or Safety Engineer, etc.)
- Inadequate training and information on care and storage
- No ongoing support to address compliance issues with fit, comfort, use
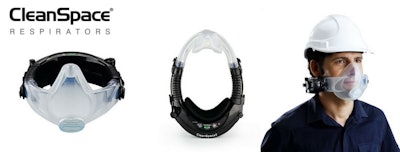
IMPO: What impacts will the stricter laws on asbestos and mining have on the respiratory equipment market?
Birrell: The stricter laws will drive more companies to offer workers respiratory equipment in order to be in compliance. This will create more opportunities for respiratory manufacturers.
IMPO: Of the manufacturing industries that typically use respiratory equipment, around what percentage would you say are using outdated equipment?
Birrell: The percentage is hard to determine but in many cases respiratory products are stored or stockpiled for years and not properly tested on a regular basis. Surprisingly, most manufacturers are still forced to select and use traditional and outdated equipment. Our experience has shown that industries are urgently seeking change and are willing and open to trialing new devices. Until now, that has not been possible.
A wide range of multi-national companies and governments have chosen CleanSpace to protect their people. Our end users have global operations and cover sectors such as manufacturing, infrastructure, resources, water/waste, chemical, energy, engineering transport and healthcare.
Alex Birrell is the CEO at CleanSpace Technology.