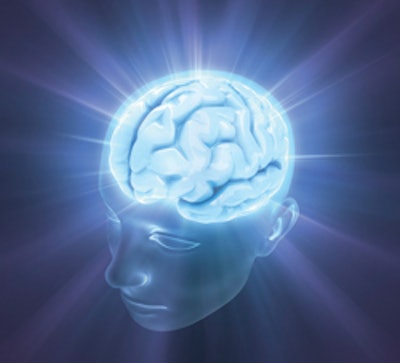
This article originally ran in the January/February 2012 issue of Food Manufacturing.
The Food Manufacturing Brainstorm features industry experts sharing their perspectives on issues critical to the overall food industry marketplace. In the January/February 2012 issue, we ask: What factors should food manufacturers consider when developing a pest control plan?
Chrissy Hansen, Media Coordinator, Bird-X
When developing a pest control plan, food manufacturers and facility managers should start by looking at the overall construction of the building. It is important to evaluate entryways including doorways, roofing, windows, vents, plumbing and cracks in flooring and walls. Where potential threats are identified, openings should be sealed tight or filled with grout or other materials. Inaccessible voids should be eliminated if possible.
It is also a good idea to make the facility exterior and surrounding areas undesirable to pests. Landscaping alterations, efficient drainage and proper disposal of food waste can help keep pests away from the property. Pest bird infestation can be prevented by blocking off areas where birds may nest and by bird-proofing convenient roosting surfaces such as ledges, beams and rooftops.
Don’t underestimate the dangers of pest birds. They are known to carry over sixty transmissible diseases — including Salmonellosis. One of the largest food recalls in FDA history (2007 Peanut Butter Recall) was eventually blamed on a sanitation breach that involved pest pigeon droppings and a leaky roof.
This kind of disaster can be prevented with the right bird control program. Pest birds are stubborn and territorial, especially once they’ve established an area as their nesting site. Facility managers should watch for pest birds and put deterrents in place before infestation occurs.
When choosing pest control products, food manufacturers should avoid chemical pesticides if possible. The last thing any consumer wants is a food product from a facility where poisons have been used. Preventative measures and ‘green’ solutions are the recommended alternative. Companies such as Bird-X offer a variety of humane and non-toxic repellent products such as bird netting, bird spikes, sonic and ultrasonic deterrent devices, and scent/taste aversions.
Pat Copps, Technical Services Manager, Orkin
For a food manufacturer, pests are simply unacceptable. They can compromise your product, pose food safety threats and jeopardize your facility’s reputation. To protect your bottom line, having an Integrated Pest Management (IPM) program in place is of the utmost importance. A well-developed IPM program provides an ongoing pest prevention cycle by removing conditions that attract pests — namely food, water and shelter — through non-chemical techniques.
The two most important factors that food manufacturers should consider when developing a pest management plan are prevention and education:
Prevention
The ultimate goal of your pest management plan should be to prevent pest problems before they start. Your pest management professional should start with a risk analysis of the areas surrounding the facility, building construction and layout, and the type of products stored or manufactured at your facility.
Work with your staff to establish an ongoing process to identify and monitor for specific pests and determine activity levels. Your pest management provider can help establish thresholds for specific pests inside and outside the facility, and determine what interventions are required when these “trigger points” are reached. Of course, the goal is to have appropriate preventive actions in place to reduce the need for corrective actions.
Ongoing sanitation and facility maintenance can also make a huge impact. Work with your pest management professional to identify potential conditions that are conducive to pests, such as exposed cracks and crevices that could lead to pest entry.
Education
It’s important to stay educated about legislation and regulations affecting the food industry. Your pest management professional can help develop procedures that address the new requirements and help with your third-party audits. The Food Safety Modernization Act (FSMA) and standards such as the Global Food Safety Initiative (GFSI), Safe Quality Food (SQF) and the British Retail Consortium (BRC) are placing a heavier emphasis on food safety, so make sure you understand the changes and plan accordingly.
Your provider should also provide staff training sessions to increase awareness, help employees identify pest signs and report pest activity. Working as a team to stay educated about pests and their impact is one of the best ways you can help prevent pests to begin with.
Michael Brittingham, Marketing Communications Manager, 4Front Engineered Solutions
In the fight against the invading army of insects, rodents and other pests into food processing facilities, the front line for this battlefield is the loading dock. Though many food-handling operations are vigilant in controlling the pest population by hiring contract pest management companies to keep their facility compliant, another strategy is to prevent the intruders from getting into the building to begin with by sealing off all points of entry.
The typical dock doorway, however, presents unique challenges to preventing pest infiltration due to the sheer size of the opening and the amount of traffic surrounding it. The good news is that efforts to better seal the building and prevent energy loss as part of an operation’s sustainability program can also help eliminate pest invasion. Here are the basics:
Dock levelers — The pit cut into the warehouse floor for this common leveler design creates passageways for pests into the building. Perimeter weatherseal kits, both retrofit and for existing levelers, seal off the gaps along the sides and rear hinge of the leveler using a combination of brush seal and heavy-duty vinyl. Without an effective perimeter seal, pests tend to exploit these gaps and make their way into the interior of a building.
Dock doors — A closed door may not necessarily be a sealed doorway. To ensure a consistently secured doorway, consider doors that can withstand impacts from material handling equipment such as forklifts. Any impact from a forklift or pallet jack can cause door misalignment and gaps between the panels and the track, which can be an open invitation to pests. Another feature to look for is panel-mounted weatherseal. The gasket or seal around the edges of the door is critical, so installing a door that has an effective compression weatherseal that rolls up with the door rather than being exposed on the doorframe offers better protection. And of course keeping the doors closed between truckloads is a good defensive approach as well.
Seals — Dock seals are essentially the large gasket that envelopes the truck trailer when its parked at the dock. Be sure to select a dock seal design that matches the style, variety and frequency trailers that may pull up to the facility. A dock seal needs to withstand the force of trailers repeatedly backing into it and regular inspection will ensure a long life for your seals. The more you do to seal off your facility, the less risk you have to pest infiltration.
Housekeeping — Don’t advertise. Position dumpsters and materials that can attract pests far away from the dock doorways.
Food-processing operations can maintain operational efficiency while eliminating exposure to pests by applying equipment specifically designed to provide a better seal around the loading dock perimeter. This approach has added benefit of preventing energy loss which supports companies’ sustainability programs.