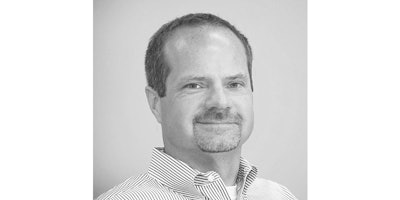
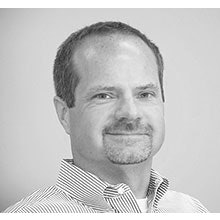
True strict lot control means 100 percent inventory accuracy with perfect record keeping and the ability to instantly report on any aspect of the inventory history. While the FDA may look for lot tracking capabilities during their recall audit, passing an audit does not require this degree of accuracy. Every manufacturer should strive beyond "getting by" with a passing audit grade and aim towards a perfect record when it comes to lot control. Used correctly, this can become a sales tool to show a high level of process control and even help protect against recalls in the first place.
Food Manufacturing recently had the opportunity to correspond with Deacom Founder and CEO Jay Deakins, who answered some questions about the impact strict lot control has on manufacturers managing recall situations.
How can a food manufacturer ensure that they are prepared for a recall?
If your inventory records are 100 percent accurate, well documented and easy to report against, you are already prepared. Any deviation from a perfect accuracy rate — from formulation through shipment — will cause recall problems.
Manufacturers need be able to instantly report on any aspect of the inventory history no matter which sub-system of the ERP software they are pulling the data from — this factor is not heavily considered in an FDA audit. In cases where not all functionalities of the sub-systems are designed for strict lot tracking or not designed exactly the same, workarounds will need to be implemented. This is most prevalent in those ERP systems encompassing bolt-on modules.
The gaps in the connection points of bolt-ons are where most issues reside. Lot tracking is subject to error if any processes are done manually, if sub-systems handle actions differently or if data has to be shared between various modules. The process breaks when workarounds, like Excel spreadsheets, need to be applied to handle required tasks. This makeshift solution opens opportunities for human error like incorrect lot numbers being entered or forgetting to delete a number after a lot was de-issued and re-issued. These cracks in the operational foundation deduct from the 100 percent inventory accuracy necessary for a smooth recall process to limit the impact on the business.
Eliminate the potential for human error and system inconsistencies altogether by finding an industry-specific ERP solution that can handle all business processes from one system.
When a recall is issued, what is the first thing that food manufacturers need to do?
In a perfect world, the company needs to first analyze the perfect documentation created from true strict lot control. With these tracking reports, businesses should be able to identify each raw material, where it came from, and its destination. The source of the recall may originate from a vendor or from the manufacturer’s own processes. Therefore, manufacturers need to quickly identify where the problem started, which lots were impacted downstream of the problem, and notify the customers who received those specific lots. Appropriate actions can then be taken to remove the affected product from further production or from store shelves depending on the timing of learning of the problem.
To the extent that the 100 percent inventory accuracy goal has been violated, further issues may arise and regulators may begin to question the underlying process. As regulators look beyond the surface and into the gory details of exactly how the business is executing its procedures, they may determine that the business was not doing everything it said it was doing during the audit process.
What costs should food manufacturers expect from a recall?
If strict lot control is done properly, the costs of a recall can be minimized. However, if done incorrectly, it can expand well beyond direct monetary impacts. Below are three primary costs for businesses to keep in mind when strategizing their recall processes:
- Labor: The financial expense on labor alone can be quite extensive depending on the number and severity of gaps present within the system. Employees will be called upon to manually gather the required data not fulfilled by accurate reporting.
- Product: Ideally, the recall should be contained to specific lots to minimize the cost. If this cannot be done, the FDA and customers may require broader ranges of products recalled based on production dates or other less desirable criteria. In doing so, unaffected products may be wasted.
- Reputation: Gaps and inaccuracies in the recall process can lead to a large distrust towards the product and brand by commercial customers and the public. This can have far-reaching and potentially devastating implications on the business.
These potential damages to the business can be minimized and better controlled with true strict lot control. Receiving a passing grade from the FDA is not enough to protect a business and its brand from the potential consequences of a recall. Take the time to identify and implement the right technology to strive for as close to 100 percent accurate inventory with as perfect documentation as possible.
Jay Deakins is the Founder and CEO of Deacom, Inc. With over 20 years of ERP experience, the Deacom team created a unique, single-system ERP solution under the guiding principle of “Complexity Made Simple.” Holding true to this concept, the DEACOM ERP solution requires no customization and is built specifically for batch and process manufacturers to achieve business goals as simply as possible. For more information, visit www.deacom.com or call 1-877-4-DEACOM.