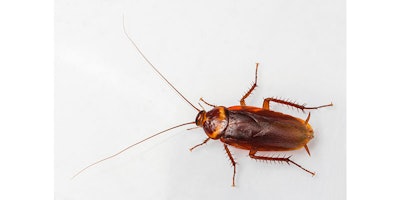
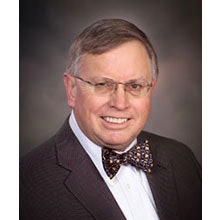
Editor's note: This article originally appeared in the January/February 2016 issue of Food Manufacturing.
Compliance with the Food Safety Modernization Act (FSMA) is on everybody’s mind. To a significant extent, much of the food industry is mostly compliant already, though certain things may be attributed to FSMA that are actually in the aftermath of the law. Some of the main challenges will revolve around new documentation and requirements to make previously confidential records available to regulators. One of the profound conceptual changes resulting from FSMA is a shift from response to prevention.
There are also new concepts of Hazard Analysis Risk-based Preventive Controls (HARPC) inherent in FSMA compliance that will likely change some cultures. FSMA and HARPC are all about assessment of risks and creating preventative systems. Here is where some pest management best practices come in.
1. Involve the entire workforce.
Provide brief training to all plant employees on things they can do to contribute to sanitation and pest management. Explain the value of keeping doors closed or the need to maintain a clean break room area. Explain the different pest management devices being used: rodent traps, bait stations, pheromone monitoring traps, insect light traps, etc. If employees understand these things and the rationale for their placement, they will tend to maintain them in their proper positions and damage will be reduced.
Explain the significance of housekeeping, litter control and spillage in individual work areas, and discourage strays or wildlife near outdoor break areas. Finally, provide pest sighting logs where they are accessible to everybody so the value of every set of eyes can be realized. Your staff is your first line of defense, so make sure they are informed.
2. Involve management from every department in facility inspections periodically.
Integrated pest management (IPM) usually requires a partnership between pest management service providers and sanitation staff, of course, but also the maintenance departments that keep the facility in good repair, production managers that allow some down time, and others. It is best if all departments participate in inspections periodically to foster buy-in and appreciation of each other’s needs. We have seen numerous examples where better participation by maintenance, especially, has yielded big benefits. Relatively small repairs to doors, or easy sealing of harborages go a long way.
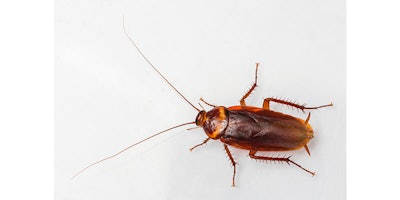
3. Be honest about deficiencies and track corrective actions.
The reality is that no facility is perfect. A state of denial can only make things worse. Don’t be afraid to acknowledge and document deficiencies. Some of the best pest management turnarounds have come when managers thoroughly documented and took pictures of deficiencies. This kind of evidence yields funding to get things fixed.
4. Foster the best possible communications and cooperation with pest management service providers.
Hiring a good service provider goes a long way, but is not the total solution to pest management. Talk with the technician routinely. Encourage recommendations, but explain priorities and constraints to making corrections in a manner that does not discourage future recommendations. Derive maximum benefits from your service provider’s documentation, monitoring data, analysis, root cause determinations and audit preparations.
5. Remember the “Integrated” in IPM.
Go back to the fundamentals of IPM and consider the biology of your main pest threats. What can be done in your sanitation program to deprive your pests of not only food, but also harborage? How well does your master cleaning schedule manage to break life cycles in key habitats? Be systematic about inspections and involve a management team periodically. Inspect not only for pests and evidence, but also for conducive conditions. Remember the essence of monitoring is the analysis: try to get an explanation for trends to determine root causes so some preventative action can be taken. Are there any non-chemical measures you can take for better pest management? Finally, chemical treatments may compensate for some of the things that are not perfect. Remember that the method of application and formulation characteristics can often be even more important than the choice of active ingredient.
Despite preventative efforts, unexpected pests will be inevitable. Every facility is different, even zones within a facility can present different challenges. Along with these tips, you should work with your pest control provider to identify these zones and sensible threshold values for each key pest in those zones. Success in the new age of FSMA will depend upon maintaining quality relationships and cooperation on documentation between pest management professionals and their food processing clients like never before.
About the author
Jerry Heath, Board Certified Entomologist, is a Staff Entomologist serving a broad range of technical service needs for IFC’s food industry clients. With nearly forty years of experience, Jerry’s career has focused exclusively in the fields of entomology and pest management in academic and several industrial settings. Since 1937, IFC is the only national pest management company focused solely on the food industry.