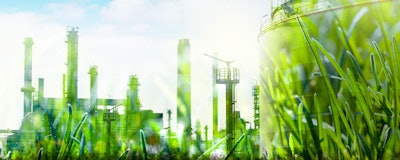

Over the past decade, the word “sustainability” has crept into our everyday vocabulary to the point of being used as a descriptor in almost every corporate mission statement, construction project, and new eco-friendly product. While the concept of sustainability becoming mainstream is certainly important, overuse of the term can cause us to lose sight of exactly what it means and why it became a popular trend in the first place.
Sustainability refers to efficiency and the way we interface with nature. Often, manufacturers and other enterprises use this term to describe the environmental impact of a specific product. However, truly embracing sustainability is about more than just the product itself; it’s about the entire manufacturing process. To successfully implement a sustainable way of working, companies must focus on streamlining the entire process, not just producing a greener product.
My company views sustainability not as a program, but as a way of doing business — it's engrained in our culture. The responsibility that we all have as part of the supply chain is to support moving in a direction that has less impact on the environment wherever possible, and this means that sustainability is not just about the finished product provided to customers, but rather reducing waste and conserving natural resources throughout the entire process to become more holistically sustainable.
Getting Lean: More than thinner materials
According to research conducted by the Lean Enterprise Research Centre (LERC), approximately 60 percnet of production activities in a typical manufacturing operation are waste — they add no value at all for the customer. One method of reducing this waste is by implementing Lean Manufacturing techniques. Lean allows for more efficient manufacturing, shipping and delivery of products to meet the demands of customers and also helps increase productivity, responsiveness, and sales.
While waste is normal for all manufacturers, we do have the ability to decrease any unnecessary overrun, thereby increasing efficiency in the process. To achieve this, it requires an initial shift in mindset and a commitment to company-wide adoption. At my company, we began embracing Lean techniques in 2003, and now focus on creating a higher quality, smarter and more efficient process through every stage of the manufacturing cycle. In order to achieve this, we utilize efficiency concepts, such as Cellular Manufacturing, Kaizens, Kanbans and Value Stream Mapping.
- Cellular Manufacturing – This concept, which involves moving related activities and equipment closer together to enhance workflow, allows manufacturers to reorganize their plant layout to be more efficient. By altering the design and layout to take advantage of related tasks, manufacturers can create a seamless process in which products exiting the slitter can be ready for shipping in minutes.
- Kaizens – When a problem needs to be analyzed and carefully mapped out before recommending a solution, kaizens can be extremely helpful. Looking at how products were prepared for shipment to customers, our packaging kaizen concluded that the purchase of a powered conveyer to transport rolls from the slitting machines, directly to the packaging area where they are automatically wrapped and packaged, would save the company time and effort, as well as reduce manual labor efforts.
- Kanbans – Visual records or signals add precision to the work process and help identify specific operations. Some companies adopt this by introducing a system of color-coded labels to identify each operation in the plant, and others use things like specific label markers or storage bins. This cuts down the possibility of errors on the plant floor. We’ve recently incorporated Kanbans in our scheduling system as well.
- Value Stream Mapping – When a kaizen team creates a map showing the step-by-step process by which a product is manufactured, finished and shipped, bottlenecks often become apparent. A careful and thorough mapping process helps identify, reduce or eliminate tasks that do not add value.
After integrating these tactics into our culture, we have seen a 90 percent improvement in on-time deliveries, 20 percent reduction in waste and a 35 percent increase in total productivity. Dollar savings are more than 10 times what was invested to roll the practice out and educate and train 1,000 employees. And, we’re helping keep our environment clean in the process.
Other Sustainable Trends
Lean Manufacturing isn’t the only way to become sustainable. There are several other trends that demonstrate the steps being taken to incorporate eco-friendly materials into labels and packaging.
For brands that are looking to reduce their overall packaging, thinner gauged label materials can help reduce waste, freight and lower carbon footprint. To aid in the container washing and recycling process, the use of washable inks and washable adhesives that dissolve cleanly is increasing, as is the use of like films and liners.
Additionally, postconsumer waste content liners offer the same performance as traditional liners, but with an added value of being part of a sustainable forestry system. Even trim excess in the manufacturing and printing processes is being collected, recycled and repurposed into plastic pellets that can be used for totes and other items.
Consider using more eco-friendly solutions, such as non-pvc products, thinner gauged films and release liners and liners made partially from post-consumer waste. Many printers are also working to implement packaging recycling programs, which include recyclable elements like plastic pallets, cores and other packaging materials.
Relationships Matter: Working Together to Reduce Waste
The environment is a resource shared by all, and, as such, it’s critical that manufacturers take the lead in adopting tactics to protect it. This includes examining the use of limited resources like electricity and water, enacting robust recycling programs, and starting other initiatives to ensure sustainable practices are a top priority for the organization.
Updated certification and training with local and national industry groups like MassMEP and the Tag & Label Manufacturers Institute (TLMI) can help support sustainable initiatives by unifying this message across the company. It is crucial for manufacturers to seek out these groups and develop strong relationships for future collaboration and shared success.
Howard Letendre is Director of Manufacturing at FLEXcon Spencer.