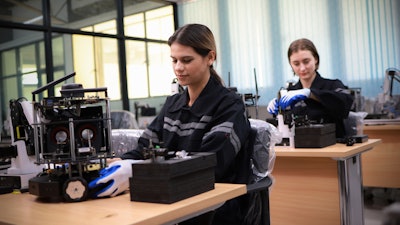
The rapidly evolving manufacturing landscape has companies grappling with a significant challenge - severe workforce shortages. According to the National Association of Manufacturing (NAM), 2.1 million U.S. manufacturing jobs could go unfilled by 2030, leading to a total cost of more than $1 trillion in 2030 alone.
WATCH: Gen Z in Manufacturing - Gen Z Just Wants to Work Differently
Manufacturing facilities are struggling to hire individuals capable of handling mission-critical tasks required for their business. In fact Deloitte found that “many of these jobs are taking longer to fill, stretching out to months of time where a company is missing key workforce to deliver open orders, expand production, or respond to customer needs.”
The root cause of this issue lies partly in the misalignment between traditional manufacturing processes and the technology literacy of the younger generations, such as millennials and Gen Z, who now form a substantial part of the workforce.
According to Jake Hall, these digital natives have grown up in a technology-based world, where smartphones, social media, and automation are the norm. However, when they enter manufacturing environments, they often encounter antiquated paper-logging processes and outdated methods of work. As a result, many young workers feel disoriented and disconnected, leading to lower job satisfaction and retention rates.
Growing Together with a New Generation
The disconnect between younger generations' tech literacy and the manual processes in manufacturing is glaring. For these new workers entering manufacturing, using inefficient, redundant and time-consuming manual tracking systems is not desirable. Younger generations expect automation, real-time data, and connectivity, yet they find themselves bogged down by manual tasks and disconnected systems.
To attract and retain the future workforce, manufacturers must recognize the need to embrace technology-based automation and align their operations with the expectations of younger workers. During our Do More With Data Summit, Jake Hall shared his perspectives on the younger generation workforce and reiterated that changing the mechanisms by which we work can benefit both the facility and the workers.
The takeaway is that now is the time to modernize systems. By doing so, manufacturers can create a more engaging, efficient, and appealing work environment.
Here are six key ways manufacturers can accommodate younger generations' tech literacy and harness the power of technology-based automation:
- Implement Smart Manufacturing Technologies: Smart manufacturing technologies, such as edge computing, Industrial Internet of Things (IIoT) and automation, can bridge the gap between antiquated processes and the tech-savvy expectations of young workers. Deploying sensors, IoT devices, and real-time data analytics, manufacturers can optimize production processes, reduce downtime, and enhance overall efficiency.
- Digitize Manual Processes: Replace paper-based logs and manual data entry with digital solutions. Digital tools such as mobile apps, tablets, and cloud-based platforms streamline data collection and management, empowering workers with instant access to critical information. This not only improves efficiency but also eliminates human errors often associated with manual data handling. Reduced errors and a faster work pace is attractive to younger workforces who are used to quick exchanges and rapid interactions.
- Provide Training and Upskilling Opportunities: Younger workers are eager to learn and grow in their careers. Manufacturers can tap into this enthusiasm by offering comprehensive training and upskilling programs on technology-based tools and automation. By investing in their workforce's development, manufacturers can create a more knowledgeable and adaptable team.
- Create a Connected Work Environment: Ensure seamless communication and collaboration among team members through cloud-based systems and digital platforms. A connected work environment allows employees to access data, share insights, and work together efficiently, fostering a sense of camaraderie and productivity.
- Prioritize User-Friendly Interfaces: User experience matters. Intuitive and user-friendly interfaces for digital tools and automation systems enable faster adoption and ensure younger workers can quickly adapt to the technology-driven work environment.
- Foster a Culture of Innovation: Encourage a culture of innovation and openness to new technologies within the organization. Involve employees in discussions about adopting technology-based solutions, and seek their input on how to improve operations through digital transformation.
The manufacturing industry is at a pivotal moment where technology and the expectations of younger generations intersect. Manufacturers must adapt to the tech literacy of millennials and Gen Z, leveraging technology-based automation to attract and retain the future workforce.
By embracing smart manufacturing technologies, digitizing manual processes, providing training opportunities, creating connected work environments, and prioritizing user-friendly interfaces, manufacturers can forge a path toward a thriving workforce, increased productivity, and long-term success. Not only does automation technology in manufacturing help speed efficiency and reduce error, but it will also help usher in new employees as opposed to replacing human jobs.
As the industry adapts to a challenging new era in manufacturing, adopting the solutions and norms of younger generations will be critical to building the products of the future.