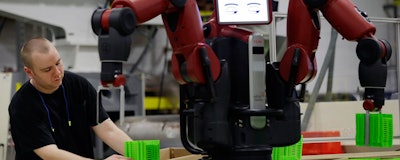

There is a revolution underway in manufacturing today that is ushering in a new era for the industry. If you take a step inside and look around one of today’s most advanced facilities, you’ll see it’s a far cry from the dark, dirty and dangerous rust-belt dungeons of manufacturing days gone by. Instead, these forward-thinking facilities are clean, bright, efficient workplaces that use some of the most cutting-edge technological advances available — robotics, 3D printing, mobile internet, cloud computing, big data and the Internet of Things (IOT) — to gain an edge in the marketplace with greater efficiencies, increased productivity, and other advantages that translate to a significantly healthier bottom line.
While those highly advanced facilities are in the minority in the U.S. today, overall they are at the forefront of an albeit slow industry shift. It is a shift from the past generation of machinery-based facilities into a next generation of information-based facilities. And therein lies the reason why, when you are on your tour around that cutting-edge factory floor, you’ll see something else that’s significantly different from the past: the population of employees that dominate the space.
The Skills Gap
With each passing year, more baby boomers are retiring from the factory floor, and their core mechanical skills are, to some extent, retiring along with them. As the numbers of these traditional workers dwindle down, the numbers of younger workers stepping up with the appropriate skills to fill the vacated positions on the changing factory floor have not kept up. This is what is known as the manufacturing “skills gap.” It is a key challenge to the smooth U.S. transition into that next generation of manufacturing — one that holds so much promise for the industry, and for our country as a whole.
Clearly, those manufacturers who embrace this new era are the ones who will shine as the scenario unfolds in the U.S. But how does an organization begin to make that transition? Certainly, a willingness to adopt new technologies in the first place is an important step. But once those technologies are in place, attacking the skills gap as the opportunity that it truly is — and doing it more quickly and consistently than the competition — is key to getting ahead in the marketplace.
Changing Attitudes Early
Finding potential employees is a facet of the skills gap challenge. High schools have in recent decades largely guided students to 4-year college programs. At the same time, shop classes and facilities have been among the first on the chopping block when it comes to cutting school system costs. As a result, the idea of a factory as an unattractive workplace has been subtly perpetuated in schools, not countered. Manufacturers willing to work with local schools and communities to change those practices and attitudes are doing themselves and the industry a huge favor that will pay off in the long run for everyone involved. Some examples include participation in “Industry Week” facility open houses, representation at local school “Career Week” activities, and developing relationships with school guidance counselors to encourage them to spread the word — early and often with students — about opportunities in manufacturing today.
Tackling Training Challenges
As a new wave of young employees does find its way into manufacturing, the challenge transitions to securing and keeping them. This can be accomplished with a seemingly simple single tactic: training. Smart, strong and consistent training programs accomplish a number of things. They instill proficiency with manufacturing processes that increase efficiency and productivity. They ensure safety and minimize downtime. And they represent something many millennials value highly: a defined career track for development and upward mobility, both vocationally and financially.
For as much as it accomplishes, though, training comes with challenges. Foremost is this: training is expensive, and can be a target for budget cuts when management is seeking to minimize costs. However, short-sighted thinking in reaction to volatile market forces can be disastrous in the long run. A commitment to consistent training must get high-level buy-in, and become foundational to a facility’s journey to next-generation status.
Other training challenges include finding qualified and committed trainers to do the teaching, and creating a realistic hands-on environment in which to do the training. High-quality, third-party consultants can help with both; they can assess your goals and current training environment, and develop a plan to move it all forward.
Finally, managing change within an organization is never easy. Change for change’s sake is never acceptable — today’s workers, more than ever, need to understand why change is taking place and what the benefits might be, before their buy-in is secured. Participants must constantly be reminded to keep their “eyes on the prize.” Embrace of change means individual jobs will become easier and more satisfying. That, in turn, leads to greater productivity. And that, in aggregate, translates to better opportunities for the organization and for everyone who’s a part of it.
No doubt, the next generation of manufacturing will not be realized without its challenges, and those challenges will take time to overcome. But with some commitment, effort and attitude adjustment today, any manufacturing organization can step onto a forward-thinking track that leads to an advanced, more competitive place in the industry tomorrow.
Pat Dean is Director of Recruiting at Advanced Technology Services.