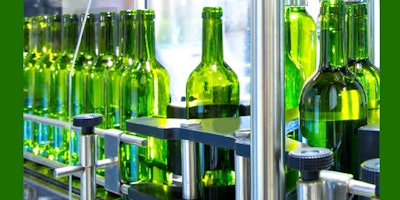
Parsec
180 N Riverview Drive No. 300
Anaheim, CA 92808
United States
+1 714 996 5302
[email protected]
www.parsec-corp.com
TM
Top 10 Proven Tips to
Maximize Uptime and
Boost Performance
If your company is not yet
performing at world-class
levels when it comes to
packaging then you are not
alone—most companies
are not. You are probably
interested in leaning out your
operations, but do not have
the budget or time for a full-
blown lean implementation.
Doing nothing is not a good option, given the
pressures exerted by your own corporate
management team to continue boosting
profits—in spite of volatile energy costs,
higher materials costs, higher labor costs,
and any other challenges posed by your
particular market. Well, there is no reason
you cannot adopt many of the same methods
and techniques that world-class companies
used to become world-class. And because
you aren’t taking early-adopter risks, you can
bring about similar levels of improvement
more quickly and at a much lower cost.
If that sounds too easy, then take a look at
the following top ten proven tips, which distill
what is working today at companies that
are the leaders in terms of Lean Six Sigma
implementations, operational excellence, and
world-class performance.
Tip One:
Set Overall Improvement Goals
that will only provide a
marginal benefit to the
business.
How do you set
appropriate goals?
Measure current
performance — then
get out and benchmark
against best-in-class
and your peers. Many
companies have increased
the productivity of their
lines by 20 percent or
more.
Often, many
manufacturers sell
themselves short on
potential improvement
gains. For example, many
companies that started
their Lean initiatives
several years ago continue
to achieve significant
gains in productivity. Do
not cripple your efforts
before you even get
started by setting less-
than-ambitious goals
Tip Two:
Review Current KPIs
any productivity improvement
initiative are a relatively small
number of Key Performance
Indicators (KPIs) that can be
measured accurately, easily
understood, and directly
aligned with your greater
business objectives.
Has your company clearly
defined these key metrics in
a document so everyone has
a common understanding
of how they should be
measured? How accurate
is the raw data? What is
excluded? Have theoretical
rates been determined
properly? These types of
questions will ensure you are
using metrics that matter.
It is difficult to improve
that which cannot be
measured accurately. Yet
many companies are guilty
of producing charts for
“historical reasons”, where
the data basis is unclear, data
accuracy is questionable,
and data is charted but
not actually used to drive
improvement. How many
times have we seen the
infamous “line efficiency”
metric with calculated values
exceeding 100 percent? Too
many.
This is always a red flag,
and likely indicates target
values are based on average
performance instead of
best demonstrated rate or
theoretical rates. Critical to
Tip Three:
Implement OEE
Overall Equipment Effectiveness (OEE) is a worthy standard
for driving productivity improvement. Defined as the product
of availability, performance, and quality, OEE breaks your
losses into three easily understandable components—each of
which requires different types of solutions to improve. Unlike
the traditional plant efficiency metric which often is designed
around typical output, OEE is designed to show all the key
losses that could be improved upon to boost productivity and
capacity.
Tip Four: Set Line-
Specific Improvement
Objectives
World-Class OEE for discrete operations
such as packaging is defined as:
Key Indicator World Class
Availability 90.00%
Performance 90.00%
Quality 99.90%
OEE 85.00%
Some lines and operations in your
plant might be running at far less
than world-class OEE. Many food and
beverage operations that begin an OEE
initiative are starting in the 40th to 50th
percentile range. No matter what is
your starting point, OEE improvement
targets should be specific by line or
operation, and should include separate
improvement targets for availability,
performance, and quality, as shown in
the following example:
Timeline Availability Performance Quality OEE
Current State 60.00% 75.00% 98.00% 44.00%
75.00% Year-End Target 80.00% 98.10% 59.00%
Gain (Points) 15 5 0.1 15
Many tools from Lean Six Sigma are
being applied successfully to improve
the availability, performance, and
quality of production operations,
including SMED, 5S and Theory of
Constraints.
Tip Five: Gain Managements
Commitment
initiative. Take the example of
a frozen foods company with
net sales of $156 million and
operating at a baseline OEE
of 50 percent. Because OEE is
proportional to output, if the
company increases its OEE
by just 5 points, its net sales
capability will increase by 10
percent, or $15.6 million.
If the company has demand
for the additional product,
based on a 78 percent cost of
products sold, then this will
boost profits by 68 percent.
If the demand isn’t there,
then the plant can cut back
on the amount of overtime or
number of shifts to achieve a
hard dollar savings.
To reap big benefits—and
most plants should be aiming
for a multimillion dollar
gain—you will need to get the
management team on board.
Their help will be needed to
support organizational culture
changes, to provide funding,
to provide reward systems,
and to keep the organization
focused on the effort in spite
of all the other priorities
competing for their time.
Management also must
accept the notion of exposing
the plant’s weaknesses so
those weaknesses can be
understood and improvements
can be made.
Once management sees
how OEE improvement
relates directly to the overall
business objectives and what
a significant financial impact it
can have, they will sponsor the
If you don’t know about it, you can’t fix it. Many plants
are stymied by a lack of accurate information that
would allow them to understand why they are stuck
at current productivity levels. Or there are so many
opportunities it is difficult to know what problems to
attack first.
Fortunately, real-time performance management
software is now available that allows companies to
automatically collect accurate, real-time performance
data from various sources. This allows complete
characterization of line performance through
continuous tracking of OEE and other KPIs in real-time,
and the relation of these to every equipment failure—
including frustrating short stops that might just be a
few seconds in duration.
Tip Six: Automate KPI Data
Collection
Once you have automated data collection, you need
a simple real-time method to share that information
with everyone in the plant who is involved in the
improvement effort. Look for RPM systems, such as
TrakSYS™ from Parsec Automation Corp., that provide
a role-based Web dashboard as seen in Figure 1, which
offers extraordinarily quick and easy access to reports
relating to each person’s specific job function.
Reports should provide one-click drill down so users
can intuitively dig more deeply into an area of interest
without having to navigate through a complex menu
structure.
Tip 7: Implement a Role-
Based Web Dashboard
Figure 1 — TrakSYS™ Web Reporting Portal Allows Role-Based Reports of Key
Performance Indicators
Tip Eight: Perform Ongoing
Analysis
Imagine playing a soccer game, but in this variant of
soccer, scoring is so complex the referees do not announce
the score until the game is over. This is the way many
manufacturing plants operate today.
It is critical to get the plant floor associates and technicians
directly involved in the productivity improvement efforts.
One way to do this is with a plant floor client application
that provides the operators with the real-time “score” as
they are running. This application also can be used to
collect additional information from operators related to
running the lines; for example, when operators stop the
line for a changeover or sanitation.
Tip Nine: Identify
Champions and
Key Improvement
Techniques
How many times does an
initiative fizzle because the
company cannot maintain
focus? It is recommended
that companies give one
or more champions the
responsibility for running the
improvement program, and
educating the plant team so
that everyone understands
the objectives and the tools
provided to reach the goals.
Many tools from Lean Six
Sigma are being applied
successfully to improve the
availability, performance,
and quality of production
operations. Examples include
SMED and 5S for changeover
time reduction, Theory of
Constraints to ensure a focus
on improving operations
that will generate a positive
impact, and processes
such as DMAIC and 5 Why
to analyze problems and
develop solutions.
Creating a complete solution
for maintenance should include
a technology platform that can
automate order generation, display
SOP documents, and provide web-
based visualization.
Tip Ten: Share
Success
The most successful
improvement initiatives
have a broad foundation.
Involve the entire plant
team by soliciting ideas for
process and procedural
improvements (in some
plants, “waiting” is the
number one cause of
downtime) and have a multi-
disciplinary team review and
respond to every suggestion
from the plant floor.
Implement the best ideas
and publicize the successes.
Provide a rewards system
that acknowledges the
contributions of individuals,
as well as line teams
that succeed in reaching
their improvement goals.
Recognition and rewards
can help transform the plant
floor culture to one that is
truly high performing.
These 10 tips have all been successfully applied in many
manufacturing plants and work best when they are all used as
part of a comprehensive improvement program.
Do not be one of the many manufacturing operations teams that
are “too busy” to achieve real improvement. It takes a significant
effort to break out of the “postmortem data analysis” mode of
operation and begin a journey toward continuous structured
improvement. This journey will provide many rewards—financial
and personal—for those who choose to follow this path.
Going Forward
Figure 2 — TrakSYS™ Provides Analytics and Tools That Enable Champions to
Drive Continuous Improvement
TM
About Parsec
Parsec is the developer of TrakSYS™, a proven operations management
software application and solution platform designed to significantly improve
manufacturing processes. Parsec is committed to providing best-in-class
products and solutions to our worldwide community of clients to assist them in
optimizing their manufacturing operations. There are thousands of TrakSYS™
licenses in use around the globe in a wide variety of Industries.
TrakSYS™ helps manufacturers to maximize asset utilization and efficiency,
increase capacity with no new capital equipment, reduce production costs,
decrease lead time, and improve profitability. For more information about Parsec
and TrakSYS™ please visit the corporate website at www.parsec-corp.com.
Copyright Parsec Automation Corp. 2016
All trademarks are the property of their respective owners