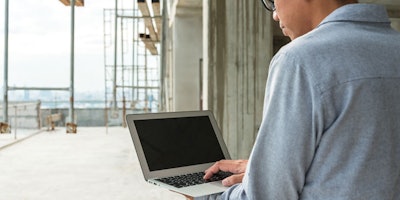
Arena Solutions
Has Your
BOM Solution
Bombed?
Next Generation Bill of
Materials Management
Whitepaper
arenasolutions.com
©2013 Arena Solutions, Inc. Arena and Arena Solutions are trademarks of Arena Solutions, Inc., Reg. U.S. Pat. & Tm. Off.
All rights reserved. Other product and company names are the property of their respective holders.
2
arenasolutions.com
In the world of product development and manufacturing, the bill of materials (BOM)
is a critical product information record for both the engineering and manufacturing
teams. Traditionally, BOMs have been created and updated in spreadsheets, and
communicated to internal teams, outsourced manufacturers and suppliers via
email, phone or fax. Usually, final BOMs are also loaded into the ERP systems.
However, compressed product lifecycles, geographically dispersed project teams,
cost pressures, outsourced partnerships, and stringent regulatory requirements
are challenging the traditional BOM management and communication in a number
of ways:
• Modern BOMs are large, complex and ever changing. It is inefficient and error-prone to manually make
and control changes in their typical spreadsheet format.
• BOMs are highly relational and include various associated data and files. Managing across multiple BOMs
and their associated data with static spreadsheets is nearly impossible.
• ERP systems do not have integral processes for engineering change orders (ECOs) and cannot be used to
control BOM changes or manage associated files.
• Product compliance requirements are managed manually and separately from BOM, even though
compliance status should be an integral part of a product record.
• Throughout the lifecycle of a product, numerous revisions of BOMs are created and communicated to
multiple internal and external teams. Keeping everyone on the same latest revision of a BOM spreadsheet
is an impossible feat.
• As a tool for internal groups, ERP systems cannot be accessed by external partners and suppliers to
obtain product BOM information
Today, new, automated bill of materials (BOM) management solutions are available to help companies effectively
manage and communicate product information and succeed in the competitive environment. Companies are able
to accelerate their new product introductions, improve collaboration with outsourced partners and suppliers, and
achieve compliance with confidence. In a 2007 study, Aberdeen Group, a global research consultancy, reported
that Best In Class companies significantly out-performed laggards in new product development (Figure 1). Best
In Class companies tend to leverage BOM management tools to improve product development performance and
profitabilityprofitability, and are over 50 percent more likely to “leverage centralized
product repositories to better capture, share and reuse core information such as
items and bills of materials.” 1
For over a decade, Arena Solutions has helped innovative manufacturers bring
better products to market faster with cloud BOM and change management
applications that speed prototyping, reduce scrap and help manufacturers
collaborate on product changes with strategic partners across the globe. Arena
understands the obstacles companies face in effectively managing and sharing
their product information, and in this paper we hope to provide insights to these
challenges and innovative solutions that help companies succeed.
Summary
A term used to describe the "parts list" of
components needed to complete a saleable
end-item*
For example the BOM for a personal computer
may list the computer, its major sub-assemblies
(board, chassis, modem, keyboard, display,
etc.) and additional materials needed for a
complete product - shipping box, user manual,
packaging, packaging labels, etc.*
*source: wikipedia.org/wiki/Bill_of_Materials
Bill of Materials (BOM), noun:
Products Meeting Product Cost Targets
LaggardAverageBest in Class
85%
57%
6%
Figure 1: Performance Differences Between Best In Class,
Average & Laggard Companies
©2013 Arena Solutions, Inc. Arena and Arena Solutions are trademarks of Arena Solutions, Inc., Reg. U.S. Pat. & Tm. Off.
All rights reserved. Other product and company names are the property of their respective holders.
3
arenasolutions.com
Makeshift BOM Management Tools
For a new product development project, engineering groups create designs with multiple computer aided design
(CAD) tools, such as electronic design automation (EDA) applications and mechanical CAD. To communicate the
component needs and cost estimates, an engineering project manager often creates an engineering BOM for the
new product in a spreadsheet. As the design progresses toward production, the part-list-like engineering BOM
must transition into a detailed manufacturing BOM that includes all the items required to make sub-assemblies
and the final product. During this process, numerous project teams contribute to the BOM and item changes
(Figure 2). The resulting manufacturing BOM is highly relational and includes various associated data and files,
such as design drawings, software files, item files, costing information, compliance status, specification data and
supplier information.
Operations, manufacturing and finance typically use Enterprise Resource Planning (ERP) systems to track
materials planning, sourcing, and other production related information. Engineering groups are often not inclined
to use ERP systems unless absolutely necessary. While a manufacturing BOM and associated item data are
usually loaded into an ERP system to manage production sourcing and costs, ERP systems are not designed to
be change control or file management tools. Consequently, all changes to items and BOMs have to be recorded,
approved and tracked outside the ERP system. Additionally, ERP systems are primarily used by limited groups
within a company and generally are not accessed by outsourced partners or suppliers. They do not provide project
collaboration capabilities that are necessary to successfully manage product development tasks and milestones
across a global supply chain.
Current BOM Management and Its Challenges
Engineering
BOM E.1
Engineering
BOM E.2
Engineering
BOM E.n
Item Master
Manufacturing
BOM M.1
Manufacturing
BOM M.2
Manufacturing
BOM M.n
Item MasterItem Master
Electrical
Engineering Team
Mechanical
Engineering Team
Compliance
Team
Planning
Teams
Suppliers
Sourcing
Team Contract
Manufacturers
Changes &
Revisions
. . .
MCAD
EDA
Other CAD Tools
ERP
System
Emails &
Faxes
Emails &
Faxes
Within a Company External
Figure 2: Multiple teams contribute to BOM creation and changes
©2013 Arena Solutions, Inc. Arena and Arena Solutions are trademarks of Arena Solutions, Inc., Reg. U.S. Pat. & Tm. Off.
All rights reserved. Other product and company names are the property of their respective holders.
4
arenasolutions.com
To update and change product information between electrical and mechanical CAD tools and ERP systems, many
companies employ spreadsheet software, such as Microsoft® Excel, to manage BOMs and to communicate them
to projects teams. Unfortunately spreadsheets are not particularly well suited for the job. Using spreadsheets
for BOM management falls short in several areas—change and revision control processes, communication with
project teams, compliance management and managing beyond a single BOM.
Manual Change and Revision Control
A modern BOM often includes a complex set of hundreds to thousands of structured items. It is not surprising
that over thousands of rows and columns in a spreadsheet to modify data leads to errors. Rapid changes
during the design and prototype phases result in a higher probability of making mistakes. Even after the first
product is built, the BOM will continue to evolve—whether due to potential bug fixes, design improvements, part
substitutes, or supplier switches—until the product reaches its end of life. The time spent to manually make
changes and fix mistakes throughout the lifecycle of a product may amount to a substantial delay in its shipment.
With multiple teams inputting frequent changes, manual revision control processes can easily become
overwhelming and chaotic. It is difficult to track which changes have been made to which revisions. There is a
lack of “a single version of truth” — the latest product information including BOM—that all project teams can
consistently and confidently rely on throughout the lifecycle of a product.
Furthermore, during the product development and manufacturing process, it is often useful to trace back the
changes to specific revisions of the BOM and make design or part comparisons. It is nearly impossible to do so
with a collection of BOM revisions in different spreadsheets.
Communication with External Project Teams
The breadth of uses of BOM related information has expanded dramatically. However, companies typically do
not want to share the entire BOM with design partners or suppliers. As a result several versions of a BOM, or a
partial BOM, have to be created for different audiences. Controlling access to ensure that the right audiences
receive only the needed information becomes difficult as the supply chain expands in depth and complexity.
Email or fax is often used to share spreadsheet-based BOMs with project teams in diverse geographic locations.
Over time, different revisions of spreadsheets may scatter on various desktops in different organizations.
Engineering teams may have a different revision from the operations teams. The contract manufacturer may have
yet another revision. The sourcing team may order incorrect parts. The contract manufacturer may execute
a wrong build. These mistakes lead to excess or obsolete inventory, as well as significant recall or rework, all of
which directly impacts the bottom line.
In a 2007 study with 150 mid-market manufacturing companies, almost half of the respondents said that including
partners and suppliers in project planning and execution was difficult 2. With inefficient manual communication,
partners and suppliers do not have consistent visibility into the latest BOM and associated data, and therefore
they are not able to make parts trade-off suggestions early in the design cycle. As a result, companies may miss
the opportunity to reduce overall product cost and optimize design for manufacturability.
©2013 Arena Solutions, Inc. Arena and Arena Solutions are trademarks of Arena Solutions, Inc., Reg. U.S. Pat. & Tm. Off.
All rights reserved. Other product and company names are the property of their respective holders.
5
arenasolutions.com
Real-time access to accurate product information is a key success factor in product development and
manufacturing. Companies must ensure that engineering and operations teams, design partners, outsourced
manufacturers, and suppliers all have secure access to a single version of a product BOM. Spreadsheets and
manual communication tools do not lend themselves well in providing and sharing such a single version of
product truth.
Compliance Management
Under increasing environmental and regulatory pressure, companies must seek cost effective solutions to comply
with FDA, RoHS, FCC and other requirements. Manually working with a large volume of data to track compliance
status for each revision of each part and its supplier items is difficult and costly, especially across a company’s
entire product portfolio and global supply chain. Tracing an audit trail and creating required reports through
multiple revisions of large spreadsheets amount to a daunting challenge. Additionally, compliance evidence files
cannot be attached to a spreadsheet and therefore need to be tracked down separately at an audit. Best In Class
companies manage compliance at the part level, including components from suppliers. The compliance status
should become a part of the BOM and should be tracked and managed with change control processes.
Managing Beyond a Single BOM
A BOM has layers of data that are interrelated, such as items, Approved Vendor List (AVL), and costing data. In
a manual spreadsheet environment, the associated data are updated and communicated separately, yet have to
be kept in synch with the BOM. For instance, BOMs and an Item Master are created and updated separately. The
inability for a company to manage across multiple BOMs limits its opportunities for categorization and part re-use.
Also when a supplier obsoletes an item, it is a tremendous undertaking to find and change the item across multiple
large product BOMs that may contain that item. Another example is that engineering often leverages a BOM from a
similar previous design as a starting point at the beginning of a new product development. As a result of the lack of
visibility into supplier parts, the BOM may include a number of obsolete parts. The issue will only be identified later
in the design phase, resulting in a potentially costly redesign.
With a spreadsheet based BOM, files and documentation directly related to an item cannot be attached easily
and shared with project teams. Communicating updates and changes to the files or documentation is even more
cumbersome. Inadequate in managing a single BOM, a spreadsheet fares even worse when it comes to managing
multiple BOMs and related data, files and documentation.
Next Generation BOM Management
New Automated Tool to Manage BOM
Many seasoned product development and manufacturing teams recognize the significant scope of today’s BOM
management and the severe limitations of spreadsheets in meeting their objectives. They fully recognize the need
for a next generation BOM management solution to replace the inadequate manual spreadsheet tools.
©2013 Arena Solutions, Inc. Arena and Arena Solutions are trademarks of Arena Solutions, Inc., Reg. U.S. Pat. & Tm. Off.
All rights reserved. Other product and company names are the property of their respective holders.
6
arenasolutions.com
BOMControl, a cloud-based solution for bill of materials (BOM) and change management, bridges the gap
between design, engineering and manufacturing with a controlled, centralized way to manage changes to product
data. (Figure 3). With up-to-the-minute accurate product information that can be accessed anytime, and from
anywhere in the world, BOMControl reduces scrap, speeds time to market and addresses the challenges resulting
from spreadsheet-based manual BOM management and inadequate communication channels (Table 1).
Electrical
Engineering Team
Mechanical
Engineering Team
Compliance
Team
Planning
Teams
Suppliers
Sourcing
Team Contract
Manufacturers. . .
MCAD
EDA
Other CAD Tools
ERP
System
A single version of BOM, item master,
AVL, AML, costing, compliance, and
other product info.
Acc
ess
any
tim
e, a
ny w
her
e
Access any time, any where
Within a Company External
Figure 3: Arena is an effective tool for managing next-generation BOMs
Typical BOM Challenges Arena Benefits
BOM changes are managed manually resulting in
errors and delay.
Changes to product information are controlled and the change process is automated and auditable.
Multiple BOM revisions exist on various desktops,
resulting in design, sourcing and manufacturing
errors.
Provides a single version of truth - the latest product information, including the BOM and changes to the
BOM. Tremendously improves the accuracy and efficiency of product record management.
BOMs are sent to internal and external teams via
email or fax, causing delays and prevents effective
collaboration.
The latest product information and changes are selectively accessible by project teams, internal or ex-
ternal, anytime and anywhere. The real time access to information encourages and enables participation
from partners and suppliers and improves collaboration across global supply chain.
Compliance requirements are managed manually
working through a large volume of data.
To confidently achieve compliance, regulatory, environmental and industrial requirements are managed
early at the part level, with associated evidence files. Audit trails are automatically established with item
record and change record.
Inability to manage across multiple BOMs limits
categorization capabilities and part re-use op-
portunities.
BOMs are managed in a relational database – BOM items are associated with Item master, costs, AVL, etc.
It is easy to access, change, and manage common elements across multiple BOMs, including items, cost-
ing data, supplier information, and other product information.
Attaching files and documentation is cumber-
some.
Any files or documentation can be attached to any items within a BOM. Changes to these files and docu-
mentations are tracked and controlled.
Table 1: BOM Challenges and Arena Benefits
©2013 Arena Solutions, Inc. Arena and Arena Solutions are trademarks of Arena Solutions, Inc., Reg. U.S. Pat. & Tm. Off.
All rights reserved. Other product and company names are the property of their respective holders.
7
arenasolutions.com
To quickly realize potential benefits, a bill of materials management solution must be built for ease of use by globally
distributed teams and their extended supply chain network. In an outsourced environment, it must provide design
and manufacturing partners and suppliers selective and secure access to a single version of a product record,
any time and anywhere. To maximize return on investment, it must bridge design tools and ERP systems without
adding significant IT complexity and cost. BOMControl has been created with these objectives in mind.
About BOMControl
Over 500 companies from diverse industries have been using BOMControl to revolutionize the way they manage
their product information, including bills of materials. Customers include Invisalign, GoPro, Digital Lumens, Speck,
Cisco, Sonos, Yakima and Square. These companies have been able to:
• Significantly accelerate product time to market.
• Greatly improve collaborative outsourced partnerships.
• Confidently meet compliance requirements.
Thousands of users from these companies as well as their partners and suppliers have used BOMControl to
access a “single version of truth” of product information and project details—including design files, BOMs, items,
costs, vendor information, ECOs, compliance status, schedules and tasks—anytime and anywhere.
The benefits they have experienced include:
• BOMs and associated data are more accurate.
• ECO cycle time and overall product ramp time are reduced.
• The ability to manage across multiple BOMs and their associated data helps increase part re-use and
reduce cost.
• Companies and supply chain partners are able to collaborate earlier in the design process.
• Product cost visibility in the design phase, when at least 70% of a product’s cost is built in, enables the
management to make trade-off decisions and reduce overall product cost.
• Contract manufacturers are able to eliminate incorrect builds and obsolete and excess inventory.
• Companies are able to streamline product compliance management from initial BOM throughout the
product lifecycle, with instant compliance reporting capability and audit trails.
Because BOMControl is a cloud product, companies as well as their outsourcing partners and suppliers can
access the solution and work collaboratively with just a web browser and Internet connection. BOMControl
eliminates the need for companies to acquire new hardware, software, or additional IT staff. Moreover, customers
can add unlimited number of users across their supply chains and selectively allow them to access product
information and project details.
©2013 Arena Solutions, Inc. Arena and Arena Solutions are trademarks of Arena Solutions, Inc., Reg. U.S. Pat. & Tm. Off.
All rights reserved. Other product and company names are the property of their respective holders.
8
arenasolutions.com
About Arena
For over a decade, Arena has been redefining PLM with a suite
of cloud applications that enable engineering, manufacturing
and their extended supply chains to work better together—from
first prototype to full-scale production. Arena helps innovative
manufacturers bring better products to market faster with cloud
PLM offerings that speed prototyping, reduce scrap and help
manufacturers collaborate on product changes with strategic
partners worldwide.
Contact
Arena Solutions
4100 East Third Avenue
Suite 300
Foster City, CA 94404
P. 650.513.3500
F. 650.513.3511