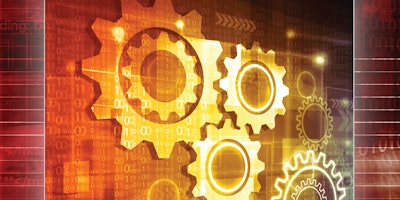
UXC Eclipse
GOING DIGITAL
Presented by:
i-Report
How To Update Operations To Improve Efficiency
Sponsored by:
2
Although technology is enabling manufacturers
and distributors to recognize and implement
more efficient and effective practices throughout
their operations, it could also pose a danger for
companies that are slow to adjust to the new
digital world.
Companies are wary of the often substantial investments needed to make
digital upgrades. In addition, businesses are concerned about the costs to
maintain digital systems and finding sufficient manpower to operate them.
The growing threat of cyberattacks could also affect companies that are putting
more and more of their sensitive data online and in the cloud.
Without digitizing their factories and warehouses, however, businesses run the risk
of falling behind their competitors, particularly as manufacturers embrace connect-
ed technologies and distributors race to keep up with the demands of e-commerce.
In this report, we’ll examine how manufacturers and distributors deploy digital
technologies and the dangers that they could face without them.
In late 2015, Deloitte and the Council on Competitiveness released the results
of a poll of manufacturing executives and research directors.
In one form or another, those in-
dustry leaders identified analytics
as the most important technolog-
ical factor to their future competi-
tiveness. Executives
identified predictive
data analytics -- which
uses massive amounts
of collected information
to identify potential
problems before they
happen -- as the most
critical to growth.
Taking Advantage of Big Data
Going Digital: How To Update Operations To Improve Efficiency
3Going Digital: How To Update Operations To Improve Efficiency
The report estimated that the market for artificial intelligence and machine
learning would climb from less than $1 billion in 2013 to $36 billion amid a
boom in data capture technology, computing power, smart algorithms and
other advanced systems.
Advanced robotics, meanwhile, should grow
from $28 billion to $38 billion between 2013
and 2019.
“The impact of next-generation technologies on advanced industries will be
significantly high,” one executive who participated in the survey said. “From
creating high-value jobs to increasing worker prosperity and productivity, they
will alter the way these industries operate.”
1 • Predictive analytics
2 • Smart, connected products
(Internet-of-Things)
3 • Advanced materials
4 • Smart factories (Internet-of-Things)
5 • Digital design, simulation and integration
6 • High performance computing
7 • Advanced robotics
8 • 3D printing and scanning
9 • Open-source design/
direct customer input
10 • Augmented reality
Council on Competitiveness List of Promising
Advanced Manufacturing Technologies
4Going Digital: How To Update Operations To Improve Efficiency
Another report from business software provider Exact and Pb7 Research found
that the use of cloud computing was crucial to financial performance among
smaller businesses.
Businesses that utilized the cloud, on average,
experienced a 25 percent increase in revenue
growth and profits that more than doubled
compared to counterparts that did not use
the cloud.
The report also said that
more than half of U.S.
businesses participating in
the survey used some form
of cloud software and that
nearly 30 percent used three
or more cloud applications.
Recent surveys, however, also showed hesitancy among many manufacturers
to embrace advanced technology.
Accounting firm Sikich found that the number of companies using technology
to improve production, business intelligence, reporting and customer service
was increasing, but that more than half used spreadsheets and other manual
processes to measure performance instead of software.
The Exact survey, meanwhile, found that only 26 percent of participating
manufacturers always wanted to maintain the latest in technology, and a 2016
survey from Accenture showed that 85 percent of respondents described
themselves as “laggards, rather than leaders” in digital manufacturing trends.
The ongoing digital revolution in manufacturing kicked into high gear with the
proliferation of Internet-connected devices and equipment.
The Deloitte-Council on Competitiveness poll listed those systems − known
as the IoT − second to predictive analytics as the most critical factor for
future growth.
The report also estimated that the number of IoT-connected machines and devices
would jump from nearly 5 billion to 25 billion over the next decade, and that the
global IoT market would increase from $1.9 trillion in 2013 to $5.6 trillion in 2019.
Deploying Industrial IoT
5Going Digital: How To Update Operations To Improve Efficiency
Fellow consulting firm McKinsey found that under a best-case scenario − in
which businesses and policymakers facilitate linking the physical to the digital −
IoT could generate more than $11 trillion in economic impact, or more than
10 percent of the world economy, by 2025.
Analysts said that the IoT is altering every aspect of commerce, from
production to distribution to aftermarket service.
“This is not a trend that’s overhyped,” said McKinsey report author Michael Chui.
Manufacturers generally recognize the benefits of connected industrial
equipment, but a recent survey found that they also broadly lack the confidence
needed to successfully implement such systems.
The Accenture poll of more than 500 senior executives found that 85 percent
expected the Connected Industrial Workforce -- which links smart machines and
human workers -- to be commonplace in their factories by 2020.
Analysts said those systems could translate to hundreds of millions in additional
profits while enhancing productivity and safety and mitigating rising labor costs.
Just 22 percent of participants, however, signaled that they would take full
advantage, with most worried about their technical challenges, the availability
of skilled workers and the vulnerability of both the system and company data.
The poll came on the heels of a warning from Department of Homeland
Security officials about the increasing online exposure of industrial facilities.
Experts said that
although no single
fool-proof method
exists to prevent
cyberattacks,
companies that
keep track of
their data, detect
problems early
and train workers
appropriately can
significantly curb
their risk.
6Going Digital: How To Update Operations To Improve Efficiency
One report last year suggested that increased investment in employee training
alone can reduce the risk of a company’s cyber security attack by up to 70 percent.
If new technology is disrupting manufacturing, it is completely revolutionizing
distribution networks.
Advanced connected systems and analytics can provide solutions for
warehouses that need to become more efficient at a time when online
commerce is flooding them with heightened demands.
In 2014, retail e-commerce sales amounted to roughly $298 billion; in 2018,
that number is expected to climb to $482 billion.
A recent report by tracking and labeling firm Zebra Technologies found that
76 percent of warehouse professionals expected rising consumer demand to
bolster both the number of warehouse locations and the volume of their
shipments by 2020.
Three-quarters of those respondents planned to accommodate those changes
by transitioning to modern warehouse management systems within five years.
Roughly the same percentage are expected to invest in real-time inventory
tracking systems and equip warehouse staff with technology over that span.
Digitizing the Warehouse
Retail e-commerce sales in the United States from 2013 to 2019
(in billion U.S. dollars)
600
500
400
300
200
100
0
260.67
298.26
340.61
384.89
431.84
481.94
534.95
2013 2014 2015 2016 2017 2018 2019
7Going Digital: How To Update Operations To Improve Efficiency
Nearly 70 percent expected to add barcode scanning capabilities by 2020, with
tablets and IoT also targeted by more than 60 percent of those participants.
Zebra officials said that those investments could help shorten delivery times,
curb stock shortages and improve fulfillment accuracy as manufacturers and
distributors increasingly deliver products directly to customers.
“Nearly half of respondents in the survey indicated a concern about labor
performance in the order, pick and fulfillment process,” said Zebra’s Mark
Wheeler. “We see this as an enormous area of opportunity.”
The upgrades, meanwhile, are arriving not a moment too soon: the Exact-Pb7
report suggested that less than half of wholesalers reported knowing the loca-
tion of every item in their warehouses. Less than 30 percent received real-time
updates on supplies and deliveries, while just 17 percent were automatically
alerted when stocks are low.
One key component in both inventory tracking and data collection is likely to be
radio frequency identification.
Finnish researchers expect the global market for RFID tags to nearly double
from $11 billion last year to $22 billion in 2020. And although high-profile tech
startups -- such as Tile -- are utilizing RFID for consumer applications, manufac-
turers and distributors will do their part as well.
RFID picked up steam as a replacement for the barcode to track machinery,
tools and other industrial equipment in recent years, according to analysts at
supply chain company Barcoding Inc.
Continued Growth in RFID
Zebra Technologies Report on Warehouse Tech
76% implement real-time inventory tracking
75% transition to modern warehouse management systems
73% equip warehouse staff with technology
68% add bar-code scanning capabilities
66% invest in tablets
62% add Internet of Things capabilities
According to poll of warehouse professionals, by 2020:
8Going Digital: How To Update Operations To Improve Efficiency
Adoption of the technology, however, is likely to quicken as it becomes more
reliable and more cost-effective.
Just like other connected technologies, RFID could allow for greater data
collection and better analyses of those numbers, which translates to improved
accuracy and efficiency.
Barcoding RFID Director Tom O’Boyle, in particular, singled out several
emerging technologies likely to impact manufacturers, from passive,
ultra-high frequency RFID to low-energy Bluetooth tags to hybrids of both.
“In 2014 alone, retail companies were responsible for the use of 3 billion RFID
labels, mostly used for apparel tagging,” O’Boyle wrote. “Now, as did barcodes,
RFID technology is ready to take other industries by storm.”
Despite business leaders’ hesitancy over costs, manpower and data security,
investment in digital technology is expected to be a primary factor in the
growth of the manufacturing sector.
From cloud computing to the IoT to advanced analytics, digitizing the factory
can bolster productivity, planning, safety and even profits.
Distributors, in particular, can use connected systems to dramatically enhance the
accuracy and efficiency of their operations and keep up with the e-commerce boom.
Moreover, investments in technology will be key to developed nations sustaining
a manufacturing advantage in an increasingly interconnected global marketplace.
A recent Deloitte report suggested that investments in both talent and
technology are helping the U.S. surpass other nations in manufacturing
competitiveness. By 2020, the analysis expects advanced manufacturing
technologies to push the U.S. to the top of the rankings.
Those optimistic projections, however, are far from a sure thing. Manufacturers
will need to maintain their emphasis on innovation in order to make it happen.
“Though the U.S. remains a global advanced technology leader, retaining our
leadership depends in large part on how successfully and holistically our innova-
tion ecosystem operates moving forward,” said Deloitte vice chairman Craig Giffi.
Conclusion
9Going Digital: How To Update Operations To Improve Efficiency
About i-Reports
About Advantage Business Media
About the Author
Advantage Business i-Reports present fresh research and analysis on
compelling and timely industry topics. “Going Digital: How To Update
Operations To Improve Efficiency” was prepared by ABM’s Manufacturing
Group (MFG) Reporter, Andy Szal.
Andy Szal writes about manufacturing, technology, energy, food, labor and
regulatory issues for Advantage Business Media’s Manufacturing group. He
previously spent nearly 10 years covering politics and business issues in
Madison, Wisconsin.
UXC Eclipse, a CSC Company is the Microsoft Dynamics Gold Partner delivering
unified, end-to-end manufacturing solutions that help companies optimize
operations and improve agility to better engage with customers and drive
business growth. We recognize that long-term success is about more than
software and technology – it’s about understanding our customers. Guiding
organizations through their digital transformation, we combine deep indus-
try knowledge \with consulting expertise. We offer methodologies to support
project implementations, business process management to define and map
requirements, and business analytics to make sense of valuable data – all with
a customer retention rate above 99% and delivered to the highest levels of
customer service.
Contact UXC Eclipse today to start your digital transformation!
Advantage Business Media (www.advantagemedia.com) is a data-driven
marketing solutions company leveraging content, technology, and business
intelligence to match its audience’s job performance needs with its clients’
solutions. With a diversified portfolio of highly focused websites, e-newslet-
ters, print publications, specialized directories, vertical search databases,
conferences, ancillary media vehicles, and associated web-based services,
ABM serves more than one million industry professionals in the manufactur-
ing, science, and design engineering markets.
About UXC Eclipse