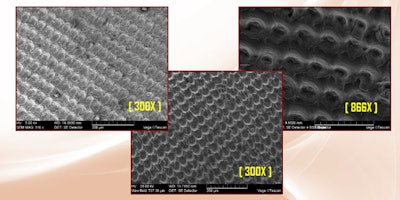
Pulse Technologies
[ Surface Texturing ] OVERVIEW
[ Motivation for Work ] [ Current Art ] [ Test Methodology ]
[ Experimental Data ] [ Results and Discussion ]
Recent regulatory activities within the medical device market have
increased the necessity for processes that yield not only superior
results but more predictable and capable results. One area of
particular concern for device designers has been the strength and
capability of metal to polymer bonds.
Current technologies such as precision blasting were tested
against advanced techniques such as laser texturing.
[ Laser Texturing ]
At Pulse Technologies, we've developed advanced laser texturing techniques to create
controlled surface roughness for improved bonding strength, particularly for bonding
between plastic and metal surfaces of a component or assembly. This process yields a
3X increase in strength on metal to polymer adhesive bonds.
We use this approach for a number of
vascular and cardiac applications,
including precision welded assemblies
and precision machined parts.
Working with customers on specific
component parts, we have mastered
the process such that it's consistently
repeatable and can be offered cost-
effectively.
It takes the right equipment, but beyond that, laser texturing is the result of some imagination among engineers,
a customer wanting something better and different and the general Pulse attitude of, “of course, why not?”
[ Motivation for Work ]
Variability of bonding polymer cannulas to metallic
subcomponents
Trends in requirements for long term fatigue life
Reduction of operator influence on adhesion
strength
Advanced controls for better repeatability
[ Current Art ]
Assemblies utilize UV cure adhesives
Bonding strength effected by surface roughness
Subcomponents mechanically treated to produce
a roughened surface
Typically abrasively blasted to increase adhesion
[ Test Methodology ]
Produce a variety of textured surface utilizing CNC
controlled laser etching
Benchmark laser texture versus abrasive blasting
Optimize laser surface textures for increased
reliability
[ Texture Rig ] [ Test Rig ]
[ Texture Results – Machined ]
[ 500X ]
[ 1000X ]
[ 2000X ]
[ Texture Results – Abrasive Blasting ]
[ 500X ]
[ 1000X ]
[ 2000X ]
[ Texture Results – Machined ]
[ 500X ]
[ 1000X ]
[ 2000X ]
[ Texture Results – Laser Texture #1 ]
[ 160X ] [ 511X ]
[ Texture Results – Laser Texture #2 ]
[ 160X ] [ 511X ]
[ Texture Results – Laser Texture #3 ]
[ 300X ]
[ 300X ]
[ 866X ]
[ Texture Results – Technique Comparisons ]
[ Laser Texturing Advantages]
Various surface features can be produced and
controlled
Laser texturing offers a highly repeatable and
reproducible process
Abrasive blasting debris do not have to be
removed
Validation efforts are reduced as opposed to
abrasive blasting
2000 AM Drive
Quakertown, PA 18951
T: 267-733-0200 / F: 267-733-0201
E: [email protected]