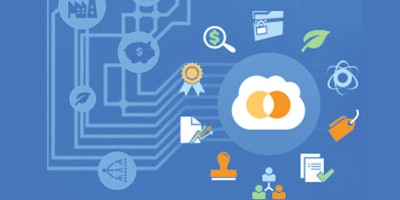
Arena
1 Sponsored by Arena Solutions
How to Turn Your Engineers
Into Product Design Superheroes
PLM Streamlines the
Design Cycle
Product innovation comes in
the early phases of development,
often during requirements analysis
and functional allocation, when
things change quickly. Component
advances can occur almost weekly.
PLM gives systems engineering a
way to incorporate new technolo-
gies as their work progresses before
allocations are made and oftentimes
even after they are made, thus mini-
mizing disruption and confusion.
Hardware and software alloca-
tions have a significant impact on
product design and manufacturing.
PLM provides a platform where
systems engineering can announce
reallocations in a collaborative effort
with input from electrical engineer-
ing and software engineering alike.
In many companies, EE and SE are
often one and the same, at least from
an organizational standpoint.
PLM also gives electrical engineers
and software engineers a chance
to influence the overall design. For
example, let’s say that a specific
functional allocation is better ad-
dressed in hardware rather than
software. This in turn may have an
impact on memory requirements,
power budget, board layout, test, QA
and QC. PLM establishes a nexus for
the presentation and collaboration
on such conditions as they arise. It
also provides a framework where
cost-benefit analysis can take place
with input from manufacturing, test,
and even marketing. Plus, these
changes can be shared project and
enterprise-wide, which enables them
to be integrated with a down-stream
enterprise resource planning system.
Engineering is an iterative pro-
cess. PLM affords access to design
decisions in a variety of formats,
depending on the need. In many
cases, expensive prototypes can be
eliminated or at least minimized,
when data is shared across engineer-
ing functions. These interactions
become a historical record of the
decisions and rationales that drove
them, which can prove particularly
helpful in the next product release
or audit. At design reviews, they
offer clients and management
transparency into the inner work-
ings of the process itself. Changes
or enhancements revealed at each
phase of the design review process
become incorporated more readily
under PLM. With easy to understand
Today’s innovative companies are built on the shoulders of the engineering teams responsi-ble for designing products. Smart companies invest in tools that make their engineers’
lives easier. In turn, that makes engineers happy and
translates into better products. A modern Product
Lifecycle Management (PLM) solution removes tedious
admin responsibilities, streamlines the design environ-
ment, and empowers engineers to collaborate more
efficiently with other cross-functional stakeholders.
Good engineers are hard to find, so once one is
found, a company should do everything within its
power to ensure that they have everything needed to
become productive. PLM maximizes a company’s price-
less human capital and enables engineers to make the
organization more profitable by allowing them to spend
more time focusing on the task they do best: designing
innovative, world-class products.
In this paper we focus on how PLM empowers engi-
neers to spend more time on product design by optimiz-
ing their relationships with the differing departments
across the organization with which they interact.
Topics include:
• PLM Streamlines the
Design Cycle
• Engineers Talking to
Manufacturing
• Engineers and the
Supply Chain
• Engineers Working
with Purchasing
• Engineers Helping
Achieve Compliance
• Real Examples of
Success
2
progress reports and design reviews,
this critical information is available
to all.
What’s more, discoveries and ap-
plications made by EE and SE (and
other functional areas), become
a legacy, a knowledge base that is
current, concise and valid, which
can drive derivative products or
enhancements to existing products.
Engineering can locate and re-use
discoveries and approaches from
previous initiatives with greater
confidence, resulting in less re-work
and earlier problem identification
and avoidance. This is especially
relevant for software/hardware
marriages. What was discovered or
designed in the past may provide
new insight into current and future
engineering efforts.
PLM superintends these intel-
lectual assets, including property
(modeling software, emulation soft-
ware, et al), CAD and 3-D files, as
well as the ideas that emanate from
the engineering process itself. Even
mistakes become part of this knowl-
edge base. These valuable painful
lessons point to approaches to
avoid in the future, blind roads that
simply became cul de sacs as well as
ineffective and costly approaches. A
mature engineering process values
failure—simply fail fast—and learn.
Customer and end-user input is
included in the knowledge base for
updates or modifications for future
products, related to—but not con-
comitant to—the current product.
Under PLM, whatever changes are
made to the physical product are
reflected in the virtual product in a
crowd-sourcing approach.
EEs Talking to
Manufacturing
The manufacturing sector is no
stranger to data organizing software.
Systems of Master Data Manage-
ment (MDM) and Computer-aided
Manufacturing (CAM) assist manu-
facturing companies in keeping
track of a product’s development
across the various departments
responsible for its production. MDM
solutions help manufacturing com-
panies manage product develop-
ment data in-house, while CAM soft-
ware is critical in executing mass
manufacturing. These solutions are
responsible for issuing commands
to manufacturing machines. While
these systems are great for manag-
ing the efficacy of in-house solu-
tions, the overall development of a
product is larger than the manufac-
turing sector alone, which in some
instances trivializes the criticality of
electrical engineers.
While electrical engineers are
commonly responsible for working
with manufacturers on compre-
hensive CAM coordinates, CAM soft-
ware rarely includes platforms for
communication or error reports. It
makes quality assurance and prod-
uct management difficult for the EE,
and correspondingly increasing the
likelihood of error. This is where
PLM software fits in. Outside of data
collection, PLM may also serve as
a platform through which EEs and
manufacturers can communicate
promptly, with relevant product
record information readily available.
PLM software not only enhances the
EE’s productivity with manufactur-
ers, it also improves communication
efficiency between EE and supply
chains alike.
EEs and the
Supply Chain
The supply chain is another im-
portant aspect of product develop-
ment that can benefit from collab-
orative PLM. While the supply chain
often incorporates SCM (Supply
Chain Management) to ensure the
efficient execution of processes to-
wards the production of a particular
product, SCM may not incorporate
the collection of all relevant data. It
may also be difficult to successfully
implement an SCM across an entire
supply chain, as each organization
has its own functional and software-
related preferences.
ERP solutions are great organi-
zational tools that enable supply
chains to increase profits and opti-
mize time. The downside of an ERP;
however, is that it leaves certain
stakeholders out of the information
loop, notably electrical engineers.
EEs play a very important role in
the supply chain and are instru-
mental to the functional develop-
ment and design of a product. Using
PLM software to open the lines of
communication between EEs and
the supply chain results in produc-
tion risk mitigation and increased
profits. An EE can more easily
oversee the production of a product
to monitor potential risks and its
adherence to the original concept
using this inclusive platform. In this
way, transitioning from an ERP to
PLM is relatively simple.
Many PLM software applications
enable data transfer from ERP pro-
grams, enabling a smooth transition
for supply chains and facilitating
enhanced communication across
the entire product development and
business cycle. The transition from
ERP to PLM software enhances the
productivity of purchasing firms
as well as it allows them to bring
their microscopes down yet another
power so as to forecast demand,
predict EOLs, select more intelli-
gent ‘cross’ buys and better discover
Sponsored by Arena Solutions
their portfolio wide adoption of
high runners as well as inexpensive
components.
PLM can greatly improve the ef-
fectiveness of supply chain manage-
ment by allowing managers and
employees to stay abreast of every
project detail, which makes commu-
nication more crisp. This high level
of communication and document
management allows managers to
codify and easily verify the change
process to reduce the number of
errors.
EEs with Purchasing
Many software solutions exist to
take data from the supply chain to
the purchaser, such as Supplier In-
tegration and ERP solutions. These
resolutions are extremely important
in enhancing the successful transi-
tion of a product from supply chain
to the purchaser.
Where these products fall short,
however, is in neglecting com-
munication between the EEs who
designed the product and the
purchasing sector who buys it out.
This can put the purchasing agents
at a disadvantage, as they may not
fully understand the breadth of a
particular product. If purchasing
can communicate with the EE who
designed a product, they can bet-
ter understand the optimal target
market and may discover other
features of the product that became
lost in translation through previous
modes of indirect communication.
Likewise, using collaborative PLM
software can also improve EEs
understanding of the end user’s
needs, so they can translate them
into the design. Using PLM software
decreases costs for the purchasing
agent and reduces the chance for
miscommunication and error.
While the product development
chain has functioned independently
of PLM software for decades, its
joint implementation can make a
considerable difference in the pro-
ductivity of product development.
EEs are responsible for creating a
product that meets the needs of
its end-user as well as comports to
product safety requirements. Absent
Turn Your Engineers
Into Product Design
Superheroes
PLM Primer for Every Engineer
3
that marriage, current methods of
production usually leave EEs with-
out means to efficiently monitor the
proper product development in a
holistic fashion.
Depending on the product, an
error in data has the potential to
harm members of the manufactur-
ing sector or the end-user. For ex-
ample, an error in the data transfer
and manufacturing of an electrical
product has the potential to harm
the production team or end user.
Since many ERP and MDM software
solutions can neglect engineers, or
innovation teams, the likelihood of
an oversight is greatly increased,
compared to incorporating PLM
software in parallel. Incorporat-
ing inclusive software, like PLM,
can have significant impact on the
efficiency of product development
because stakeholders can commu-
nicate with one another throughout
the product’s ideation, development,
production and retirement. This
can eliminate differences between
product concept and end product,
minimize production risk, and
increase profit margins across the
enterprise.
EE and Compliance
PLM software minimizes the
time it takes to file certification
paperwork and check compliance
standards. EEs have to carefully
plan and approve changes in design,
as well as be ever vigilant before
they are tendered to hardware test.
PLM allows them to keep track of
the process and approve changes,
to ensure other employees are
using the most up-to-date product
plans. It also enables them to stay
informed on electrical compliance
standards and regulations like UL
for the United States, and CE (Con-
formité Européenne) for Europe.
Since many manufacturers create
products for delivery in multiple
countries, the EEs are responsible
for compliance with standards for
each respective country. PLM allows
organizations to avoid potential
compliance errors by giving every
employee access to current order
information, standards, and ap-
plications. EEs can also keep track
at what stage each project is in and
which change orders are still pend-
ing or have been approved. This
makes it easier for them to approve
products for further compliance
testing. While PLM cannot cur-
rently track testing, having a more
rigorous supply chain management
can prevent the likelihood of testing
failures later. Additionally, PLM can
track a product through a closed
loop, which enables product man-
agement of all iterations throughout
its lifespan. This accelerates time to
market launch through repurposed
designs and tribal knowledge.
As demonstrated above, there are
a number of benefits that EEs can
gain from using PLM. The benefits,
concerns and considerations of PLM
by EEs will be illustrated below
using case studies and academic
journals.
Real examples of success
Ruckus Wireless is a manufac-
turer of WiFi routers and modems.
They use Arena PLM software to
increase the level of efficacy in their
manufacturing process from start to
finish. Ruckus Wireless was having
issues with quality control because
items were being damaged due
to manual errors. Because Arena
PLM BOMControl is cloud-based
and provides a centralized loca-
tion for all product information, it
is particularly useful for EEs. The
software makes all information
easily accessible and ensures that it
is current, which minimizes errors
from engineers who are otherwise
acting upon outdated data. This
allowed the company to cut costs by
minimizing errors.
PLM software also proved ben-
eficial for EEs when compliance
standards changed in the European
Union. Restriction of Hazardous
Substances Directive (RoHS) and
Waste Electrical and Electronic
Equipment Directive (WEEE) stan-
dards vary greatly from country to
country. EEs have to keep track of a
high volume of compliance and ever
changing standards to ensure each
product will meet the legal require-
ments of each country. PLM allows
for easy access to this updated
information. Companies can also
print off certification reports at the
click of a button, which reduces
compliance reporting. Providing cer-
tification reports is also crucial to
ensure merchandise arrives quickly
to retailers by shortening the time
merchandise is stopped for border
inspections and quality assurance.
Yukon Medical is another compa-
ny that benefited from using Arena
PLM, but they used it for slightly
different reasons than Ruckus Wire-
less. Yukon Medical is a manufac-
turer of pharmaceutical preparation
and delivery devices. As such, it is
not only important for their devices
to comply with electrical compli-
ance standards, but their products
must also comply with strict FDA
regulations.
Considering the stakes – medi-
cal devices are often the difference
between life and death. Engineer-
ing and design time was becoming
lengthier and lengthier, but PLM fa-
cilitated collaboration, which helped
Yukon speed up its processes. With
particular respect to engineers and
specifically EEs, the instant creation
of Engineering Change Requests
(ECRs) and ECOs significantly sped
Sponsored by Arena Solutions4
Sponsored by Arena Solutions
up the communication processes,
diminished time spent waiting for
approval, and reduced the possibil-
ity for errors. All employees can
request changes for approval, see
when/if a change is approved, and
act on the most current engineering
and design data.
Zeelander Yachts benefited by
using PLM to establish a closed
knowledge loop system that enabled
them to optimize product control
and improve relationships with all
stakeholders. As one can imag-
ine, many components come into
play when building a yacht. Many
departments must work together to
innovate, engineer, and construct
the vessel. PLM allowed Zeelander
Yachts to keep track of every single
component, design, costs, and all
other considerations every step
of the way. This not only allowed
Zeelander to create and deliver a
perfect product, but the company
also communicated this information
more easily to stakeholders, includ-
ing manufacturers and investors, by
broadcasting timely, comprehensive
product launch reports.
While Zeelander Yachts made use
of the ECR, ECO, and BOMControl
features of PLM, they also made use
of the customer relationship man-
agement system (CRM) to strength-
en communication between their
varied stakeholders. Better CRM can
lead to lower manufacturing costs
and satisfied investors.
Conclusion
PLM is a tool engineers can wield
that makes their job easier. They
can collaborate to button down
every facet, for each department
to strengthen their capabilities to
Black Belt status.
It is the interconnectedness of
PLM that gives engineers these
“capabilities.” Being able to reach
around the globe and collaborate
across departments on a whim. And
it’s easy. n
Resources:
1. http://www.arenasolutions.com/arena-
case-studies/
2. http://www.arenasolutions.com/about/
testimonials/
3. http://www.product-lifecycle-manage-
ment.info/
4. http://www.arenasolutions.com/pdfs/
resources/Top_10_PLM_Report.pdf
5. http://www.ibm.com/solutions/3ds/us/
en/index/electronics_hightech.html
6. EVGA recall http://www.evga.com/
5