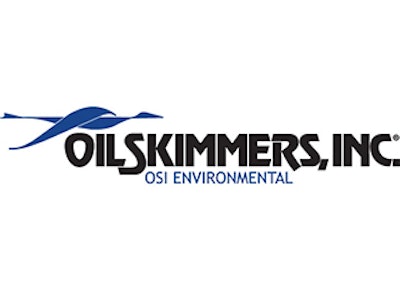
Imagine tackling your greatest production challenge quickly,
easily and inexpensively.
Now imagine tackling your greatest production challenge
quickly, easily and inexpensively – and even generating a profit
while doing so.
For businesses and industries that deal with oil separation and
removal, the solution does not need to be expensive or
inefficient. In fact, the answer may be simpler than you think.
When Oil is a Problem
Industries as diverse as steel, biodiesel, manufacturing, food
processing, trucking service industries, wastewater treatment
and utility – all face a simple, common problem: oily water.
Where water is used extensively at some point along the
production process, either in cooling machinery, washing
down equipment or playing a crucial part in the manufacturing
process, problems occur when water picks up oil. Regardless
of whether the facility reuses the water or sends it to a city
treatment plant, it has to be removed.
Many facilities, however, are not equipped to effectively
remove oil. Plant efficiency suffers.
Even worse, profitability suffers.
Traditional Approaches to Oil/Water Separation
The first step in removing oil is separating it from water.
Stokes’ Law states that, given time and a large enough surface
area, oil and water will eventually separate, giving you two
distinctive layers. A good system of separation will give you
those two layers.
To facilitate this process of separation, many plants use built-
in grease/oil water interceptors, or separators. By using a
combination of flow patterns, baffles, plates or aeration to
increase contact with the oily water, these speed up the
process by maximizing the number of small droplets that will
agglomerate and rise to the surface, resulting in a concentrated
oil layer and a layer of oil-free water ready for secondary
processing or discharge.
While separators themselves are efficient and inexpensive to
use, there is still the problem of removing the separated oil.
When oil is not continuously removed from the surface of the
oil/water separator, several problems can occur:
n Heavy rain or water flow can exceed the design of the
separator and wash out the oil build-up;
n Failure to remove the oil can cause excessive oil build-up,
increasing the chance for the oil to escape and reduce the
area of the separation chamber;
n The oil layer prevents oxygen from reaching the water,
allowing anaerobic bacteria to grow, plugging separator
plates and emitting foul odors;
n During maintenance, or as components are lifted out, the
tank walls and interior components become completely
oil-coated;
n When completely drained, residual oil escapes into the
outlet piping and released downstream once the separator
is refilled; and/or
n The oil layer can make visual inspections of the coalescer
and components very difficult, if not impossible.
Most oil removal solutions and services are effective in
removing the oil, but they can be expensive, with some
requiring additional manpower or expensive parts that require
continuous maintenance.
WHITE PAPER
The Challenge of Removing Surface
(Free-Floating) Oil
WHITE PAPER
Traditional Methods of Oil Removal
Absorbent Pads
Available in different shapes, sizes and materials, pads are
used to absorb excess oils and greases that can result from
accidents or spills during routine machinery operation.
Effective for preventing the spread of source leaks and
efficient in terms of pickup, pads are useful for removing
small amounts of oil.
Using them on large volumes of waste oil, however, makes
them impractical for daily usage due to costs involved with
their purchase, disposal and deployment. In addition, only a
small amount of oil can be squeezed out of the pad for
recycling, while the remaining oil must be disposed of in a
landfill, or burned.
Vacuum Trucks
At first glance, vacuum trucks are the ideal solution for oil
removal, as the oily layer from wastewater is simply vacuumed
up and shipped off to recycling or disposal points.
For large oil spills, vacuum trucks are ideal as they will quickly
pick up large amounts of oil.
And, when waste oil is thoroughly separated, highly
concentrated and stored in appropriate receptacles, then this
method is also quite efficient.
However, vacuum trucks can become expensive, depending
on the frequency of their use. If used more than once a
quarter, costs begin to rise.
Even more, due to the nature of the process, large amounts
of water are also taken with the oil, resulting in higher volume
costs.
Finally, when the oil is removed infrequently, it begins to build
up again on the surface, leading to problems including the
potential for bacteria growth.
Manually Operated “Slotted Pipes”
A great many plants have an oil separator consisting of a large
tank or basin containing a series of baffles and weirs over
which oil and water pass.
With a “slotted pipe” system, the oil is removed using a pipe
with a horizontal opening located near the top of the container.
An operator removes the oil by turning the horizontal opening
downward until it meets the floating oil layer. The oil then
flows through the pipe to a collection receptacle.
While these pipes work well on thick layers of oil, they have
the same drawback as vacuum trucks: They remove large
amounts of water.
When the oil and water mixture overflows, it is difficult for
the slot skimmer to remove only the oil. A large percentage of
water enters the pipe, requiring a second oil separation and
possibly a third or fourth try, increasing its expense.
Overflow Weir
A large percentage of oil separation devices currently in use
today are some variation of the overflow weir, where oil is
floated over a lip into a trough or pipe.
However, like vacuums and slotted pipes, the problem is
taking on water and other fluids along with the oil.
An operator is responsible for avoiding excessive loss of water
or coolant, avoid overflowing the skimmed oil storage tank,
prevent the lip from being blocked by floating debris, and to
perform any secondary decanting operations necessary to
eliminate excess water in the oil for disposal or to avoid loss
of coolant. Neglect of duty by an operator can result in gross
escapes of tramp oil.
Because overflow weirs require constant supervision, they are
not an efficient separation method. The operator must
carefully calibrate the weir at all times; too low, then you run
the risk of taking on too much water. Too high, and the weir
will fail to remove the oil.
Troughs are also difficult to adequately separate the oil. The
surface to be skimmed is usually down in a hole so the
skimmed material must be pumped out. Because the oil is
usually sticky and loaded with grit and debris, pumping it is
costly. Adding to costs, the tank must be drained and dug out
periodically.
Oil Skimmers
With so many variables at play, it makes sense to choose a
solution that is simple, dependable, easy to use and is
extremely cost effective: oil skimmers.
Which to choose? Oil skimmers come in a variety of types,
including tube skimmers, drum skimmers, belt skimmers and
disk skimmers, all designed with one idea in mind: Oil sticks
to a surface; the skimmer scrapes it off.
But not all skimmer types are created equal.
Drum and Disc Type Skimmers
Drum and disc type skimmers are fairly simple in execution:
The lower edge of a revolving drum or a disc submerges and
collects oil on the surface, carried up to a scraper, where the
oil is then scraped off into a trough or tank.
Unfortunately, the drawbacks to using this type of skimmer
are many.
First, with both of these types the disc or drum must contact
the surface. This means that either the water level must be
rigidly controlled or the whole machine put on a raft.
In addition, floating the machine often interferes with the
other equipment in the reservoir and runs the risk of sinking
due to solids building up, or an accident.
Finally, these machines cannot elevate the skimmed oil very
high so pumping is often necessary. The heavy, gritty oil
skimmed sometimes requires the addition of water so that it
can be pumped, requiring secondary decanting.
Belt Skimmers
Belt type skimmers look like belt conveyors standing on end
with the idler pulley under water and the drive pulley above
the skimmed oil storage tank. Floating oil clings to the belt
surface and is conveyed to a scraper, where the oil is scraped
off into a trough and flows to the storage tank.
The Challenge of Removing Surface (Free-Floating) Oil
WHITE PAPER
However, in order to compensate for level fluctuation, belts
are used to reach the low levels. When the liquid level is above
this low level, the bottom of the belt hangs down into the
solution. Thus the oil that had previously settled on the
surface is now picked up and carried into the liquid, defeating
the entire skimming process and exacerbating typical oil in
water problems: clogged lines and filters, less efficient
cleaning, etc.
Belt skimmers also only offer a small strip to the surface to
which the oil can adhere. In addition, belt skimmers create no
movement to draw the oil.
The support or bridging needed to mount belt skimmers can
often exceed the cost of the unit. Further, belt skimmers
require a bottom pulley to keep tension on the belt, trapping
debris and oil and throwing the skimmer off track.
Oil and debris can also create problems with a belt skimmer’s
drive mechanism and wiper blades, requiring constant
adjustment and/or corrective maintenance.
Tube Skimmers
Tube skimmers are designed to ensure consistent, even
operation, regardless of the application. And when it comes
to performance, tube skimmers consistently outperform any
other types of skimmers.
Tube skimmers run on a simple concept: continuously
remove oil from the surface of the water using a closed-loop
tube that attracts the floating oil or grease.
Oil adheres to the outside of the closed looped tube, which is
continuously driven across the separator’s surface and
through a set of scrapers that remove the oil, which is then
drained into a collection tank.
Tube skimmers can efficiently remove all petroleum-based oil,
fats, greases and oily wastes as well as animal and vegetable
oils that float on the surface of water. And unlike other
skimmers, which can get clogged by floating debris, tube
skimmers have the ability to snake over, under and through
debris to constantly pick up oil.
Tube skimmers are a practical solution, with benefits that
include:
Availability in a variety of configurations. Skimmers are
capable of removing oils, great and floating sludge from a
variety of containment systems, including in-plan open or
closed tanks and vats.
Flexibility and versatility. When equipped with a balanced
boom system Tube Skimmers can extend as far as 16 feet and,
can move around as desired for maximum portability,
eliminating the need for expensive bridging or foundations.
In addition, the free floating collector tube floats up and
down with the liquid level, keeping the machinery up and out
of danger.
Easy to install. Tube Skimmers are operationally efficient.
Tube skimmers provide pre-fabricated mounting systems that
provide easy, economical installation.
Low maintenance. Due to simplicity of design, tube
skimmers are not susceptible to clogging and parts
maintenance problems of other types of systems.
Less costly to use. Tube Skimmers can be unattended and
left to run 24 hours a day, seven days a week. No operators or
additional manpower is required to attend to a tube skimmer.
Tube Skimmers from Oil Skimmers, Inc.
A longtime leader in the automatic oil skimming field, Oil
Skimmers, Inc. has been providing simple, effective and cost-
saving solutions to business and industry for over 35 years.
Headquartered in Cleveland, Ohio, the company has 26 sales/
services offices in the United States and 48 overseas dealers.
Ninety percent of the employees at Oil Skimmers Inc. have
worked for the company for over 25 years.
The company’s focus is on the production of reliable
equipment that gives years of trouble-free operation, and
friendly, customer-oriented service.
Dedication to quality. Skimmers are made with high-abrasion-
resistant ceramics and high-strength steel and bronze. Quality
parts means fewer service calls, for less downtime and fewer
maintenance costs.
Using high-quality parts, our systems are designed to be your
valuable “silent employee,” by doing their job of picking up
oil day after day, year after year with virtually no supervision
or maintenance.
When problems arise concerning oil removal from wastewater,
it is nice to know you are dealing with a company whose
personnel have seen and solved thousands of applications
across all industries.
The Challenge of Removing Surface (Free-Floating) Oil
WHITE PAPER
CAsE studiEs
Not only do tube skimmers from Oil Skimmers, Inc., make
sense for the environment, they make sense for the bottom
line, as well. Consider:
Case Study #1: A Steel Manufacturer
A floating tube system from Oil Skimmers helps a steel
manufacturer with a 148” plate mill and 86” hot strip mill save
approximately $400,000 per year.
By recovering the high-grade lubrication oil that leaks into the
cooling water, the company not only saves money but recovers
an average of 15,000 gallons of oil each month, as well.
Case Study #2: A Producer of Canned Meats
An Oil Skimmers system helps a producer of canned foods
including turkey, chicken, ham and beef not only save money
– but make money.
By using a skimmer on its treatment lagoon to draw off the
fat generated in the cooking process, the company
recovers approximately 10,000 pounds of fat or waste oil
per week. Further, by selling it to a reclaimer at the going
market price, the company earns anywhere from $2,500 to
$5,000 a month.
Case Study #3: A Grinder Coolant Pit
A company extends the life of its coolant using an Oil
Skimmers floating tube system – and saves $12,000.
With a coolant pit capacity of 14,880 gallons that uses 295
gallons of coolant concentrate at $1,500 per charge, the
company was able to save money by using the system to extract
the waste oil as it passed by in the normal circulation of coolant,
extending the length of time before the coolant was dumped.
Environmental Considerations
Since 1974, the Environmental Protection Agency has
issued guidelines and standards regarding effluent
limitations for more than 50 industrial categories. These
rules are aimed at reducing the discharge of conventional
pollutants by at least 115 million pounds per year at an
annualized cost of $1.9 billion.
In a review of manufacturing facilities that produce oily wastes,
the EPA found oil skimming to be an effective and
environmentally friendly option. As noted by the EPA, skimmers
are cost-effective and efficient at removing waste from water.
According to the agency, skimming, along with water
conservation, leads to generating less pollution and leads to
more effective treatment of wastewater. Skimming is also
more effective in removing effluents, saving industry over $40
million in annualized costs.
Because skimmers assist in helping companies reuse water,
this in turn helps businesses save money by reducing water
consumption bills.
Again, the oil and grease collected by a skimmer can be
valuable to other industries. For example, industries with
vegetable oils or animals fats as by-products can be provided
to industries that make products ranging from biodiesel to
soap to animal food. Waste petroleum oil can be reused to
make new petroleum products.
The “Green” Alternative
As stricter environmental standards take hold, businesses
continue to face the challenge of meeting regulatory
standards yet maintain profitability.
In demanding economic times, that challenge is even greater.
Case Study #4: Oil Services Industry
A petroleum specialty products distributor reduces the
amount of oil in its wastewater by about 99%, meeting state
guidelines and avoiding costly penalties.
With the installation of a Model 6 V Brill™ oil-recovery system,
the company was able to hit state compliance thresholds each
month, beginning with its very first test. Failure to comply
would have meant the loss of its operating permits, forcing
the company to shut down.
The Bottom Line
With a tube skimmer from Oil Skimmers, the positive ceramic
drive and wiper system maintenance is kept to a minimum,
for a reliable, low-cost method of constant oil removal.
Oil skimmers are:
n Efficient
n Durable
n Cost-efficient
n Environmentally-
friendly
n Require no human
supervision
n Can run 24 hours a day,
7 days a week, 365 days
a year.
Even more, oil skimmers can help you make money, by turning
excess oil and grease into a source of additional revenue.
Using an oil skimmer assures that the oil will be easily
removed, with minimal effort. With the right oil skimmer, a
facility can effectively manage the oil, save time, and even
help a plant make money.
Contact Oil Skimmers Inc.
Is a skimmer right for you? Talk to us. Find out for yourself
how simple, easy and effective an Oil Skimmers tube
skimmer can be.
Oil Skimmers, Inc. 12800 York Road
Cleveland, OH 44133 USA
USA Toll Free: 800-200-4603 | Ph: 440-237-4600
Fax: 440-582-2759 E-mail: [email protected]
www.oilskim.com
1 Environmental Protection Agency, 40 CFR Parts 413, 433, 438, 463, 464, 467, and 471, Effluent
Limitations Guidelines, Pretreatment Standards, and New Source Performance Standards for
the Metal Products and Machinery Point Source Category; Proposed Rule, January 2001
2 Ibid.
The Challenge of Removing Surface (Free-Floating) Oil