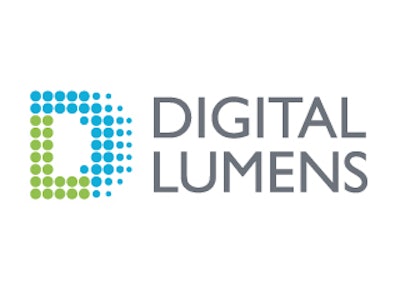
INTRODUCTION
Worldwide, leading facility managers and operations professionals are scrutinizing their energy use and re-evaluating
traditional lighting choices — even high-intensity fluorescent (HIF) — in search of energy savings. In fact, rapidly
escalating energy costs are often the catalyst for considering a lighting upgrade project, and LEDs are now part of the mix
for most facilities.
While up-front costs are incrementally higher, LEDs’ lifetime energy costs are 50 to 90% less than legacy HID, HPS and
even fluorescent alternatives — and there is no maintenance. This means that the frequently held belief that the lowest
cost fixture offering acceptable light levels is the best choice for a facility is no longer valid; total cost of ownership
(TCO) and long-term energy use is where the focus should be.
The next question — after decades of experience with high-intensity discharge (HID), high-pressure sodium (HPS),
and now T5 and T8 fluorescent fixtures — what is the best way to accurately assess the costs and benefits of the
various solutions? This Guide lays out a framework that you can apply, and incorporates lessons learned from more
than 100 million square feet of installed intelligent LED systems across many of the most challenging production
environments worldwide.
STEP-BY-STEP
A lighting retrofit, new build, or a facility expansion, is an unprecedented opportunity to make a lasting impact. And,
if you are considering LEDs, today’s decision will easily last for more than a decade, so it is worth the time and effort
to take a comprehensive approach to the project. Key steps include:
• Establishing stringent light-quality metrics, energy-intensity guidelines, and performance goals;
• Starting the planning process sooner to allow for more rigorous evaluations, partnering with your Finance team, and
taking full advantage of widely available energy efficiency and tax incentives to reduce overall project costs;
• Exploring the additional capabilities and efficiency benefits available from LEDs with fully integrated controls; and
• Assessing lifetime cost of ownership metrics to incorporate year-over-year energy and maintenance savings into
financial models.
If you do not have the skill set or bandwidth on staff to manage the evaluation, consider engaging a qualified energy-
efficiency consultant who can help with key aspects of a project. They have deep subject matter expertise, familiarity
with utility programs and contacts, and can ensure that the project moves forward on schedule and on budget.
CLEAR PROJECT GOALS, LEGWORK, TESTING AND ECONOMIC ANALYSIS = SUCCESSFUL EVALUATION
Rather than just setting out to ‘replace failed lights’ or ‘reduce energy use,’ a lighting project gives you the ability to
improve lighting performance, gain new types of functionality, and to send savings to the bottom line, while providing
a comfortable and safe work environment. Projects that deliver on these promises have four key elements in common:
1. Clearly established evaluation criteria,
2. Early outreach to potential incentive partners and government entities,
3. Accurate facility data and hands-on testing of specific solutions (both fixtures and controls) in your facility, and
4. A comprehensive economic analysis that looks at all aspects of the investment.
Thoughtful project planning and a thorough evaluation enable well-prepared decision makers to confidently identify
the optimal lighting solution that balances performance and value with lifetime costs. Given the 20-plus-year lifespan of
contemporary lighting solutions, it is an investment that delivers significant returns long after installation and even beyond
capital payback.
EVALUATION GUIDE
Four Steps to a Successful Lighting Evaluation
2 Digital Lumens
Four Steps to a Successful Lighting Evaluation
STEP 1: DEVELOP EVALUATION CRITERIA
Concrete performance goals and measurement criteria are critically important to a successful lighting project. Used not
only to guide final decisions, these criteria narrow the field of alternatives to a manageable number. With this approach,
you will spend more time thinking about success factors and potential fit in your facility, and less time considering
unsuitable products that do not meet your criteria.
Is your main goal to improve lighting quality within your facility? Enhance illumination levels
reaching work surfaces? Reduce maintenance costs? Reduce the number of fixtures?
LEDs offer energy savings ranging from 50% for simple fixtures to more than 90% for
intelligent LED lighting solutions, with lifetime ratings in excess of 200,000 hours. Since your
decision is likely to impact the facility for decades, be bold in setting your efficiency goal.
In foot candles or lux, specify desired light levels for all relevant work spaces — production
areas, racked aisles, loading bays. A minimum facility-wide target value can be used, but is a
less precise way of evaluating lighting alternatives.
For facilities where particulate matter (e.g. dust) or water are significant factors, the IP (ingress
protection) rating ensures the lighting fixture is designed to withstand the environment where
it will be used. IP Rating descriptions and codes can be found at www.codecorp.com.
As your organization grows and changes, how is this likely to impact your lighting needs?
Will you need to reconfigure your manufacturing operations? Will your lighting settings in
that area or others need to change? Do potential solutions accommodate these changes?
ECONOMIC GOALS
Historically used to evaluate the viability of lighting projects, payback is a useful, if basic,
evaluation metric that massively understates the ongoing impact of energy costs on facility
budgets. Most facilities now analyze payback, total cost of ownership (TCO), and return
on investment (ROI) calculations. This provides a comprehensive view of impact on facility
budgets – in both the short-term and the long-term, where individual analyses such as
payback, alone, may favor one scenario and ignore the longer-term energy-savings and
maintenance costs.
Expressed as a percentage, ROI divides the benefits associated with an investment by the
cost, to determine a project’s effectiveness as compared to other potential investments.
As an “opportunity cost” metric, it falls short of providing a complete picture on the impact
of energy costs on lighting budgets.
TCO considers all of the costs associated with lighting a facility throughout the lifetime
of the installation, or at specific points in time, such as at 5-, 10- or 20-year intervals.
Decision-makers are increasingly using TCO as it provides the best measure of the
enormous impact lighting energy costs have on their budgets over an extended period
of time.
Since every facility is unique, it is important to define your criteria for success and involve all key stakeholders associated
with the lighting decision. The more accurate your goals, the better the outcome. The more data you can gather about
your facility, the better position you will be in when it comes to assessing specific solutions.
Overall Goals
Energy Savings Goal
Target Light Levels
IP Rating Required
Adaptability for
Future Needs
Payback
ROI
TCO
Digital Lumens 3
Four Steps to a Successful Lighting Evaluation
STEP 2: DETERMINE AVAILABILITY OF UTILITY INCENTIVES AND TAX DEDUCTIONS
In North America, utility-based energy efficiency incentives are pervasive — but vary widely. If you are considering
a lighting upgrade, reach out to your utility early in the project evaluation to understand the range of incentives and
eligibility requirements. Incentive savings directly reduce bottom-line costs by up to 50% (and sometimes even more),
making highly efficient lighting that much more compelling and affordable.
When contacting your utility program manager, know that:
1. Most utility companies offer not just one, but two forms of energy efficiency incentives:
a. Prescriptive incentives – a fixed rebate per fixture, usually with add-ons for sensors and controls, or
b. Custom incentives – based on actual energy savings, these typically deliver the highest return, but usually
require lighting solutions that deliver ‘extraordinary’ energy savings, usually defined as 70% reductions in
energy usage or more (easily attainable with today’s intelligent LED lighting).
2. Incentives must be negotiated and approved by the utility company in advance of project start. Utilities will not
award custom incentives once a project is underway.
Since the majority of utility companies now offer some form of energy efficiency incentives, reaching out early will
enable you to refine your lighting search to account for the significant cost savings these incentives provide industrial
energy users. Also, keep in mind that lighting design firms and energy-efficiency consultants are valuable resources
for navigating the incentive landscape. They know what programs are available in a region, understand the criteria, are
familiar with the application process, and are likely to obtain speedier approvals with optimum incentive awards for a
particular project.
FEDERAL TAX INCENTIVES
Since the federal government is also actively involved in promoting energy efficiency, various tax incentives are available
to encourage high efficiency capital equipment upgrades. The most notable federal tax incentive available for industrial
lighting is EPAct, which provides for the accelerated depreciation of an energy efficiency retrofit.
Applying for tax benefits does not impact a facility’s ability to secure utility incentives and the tax savings are usually
worth the effort. We highly recommended that facilities engage an EPAct consultant to navigate the process of applying
for these deductions, as the program criteria are changing. Your energy efficiency partner likely has contacts that
they can recommend. And, in all cases, be sure to include your CFO/Finance team early in the conversation to ensure
eligibility and compliance.
STEP 3: GATHER YOUR FACILITY DATA & TEST POTENTIAL SOLUTIONS
Whether a new build or lighting retrofit, the first step in a thorough lighting evaluation is documenting basic data about
your facility and how lighting will be used. This includes:
Overall square footage for the entire facility and individual spaces.
Primary activity in the facility, and how major spaces are being used? For example, a
contract manufacturing plant with 171,000-square feet of production, 35,000-square feet
of storage and 25,000 square feet of shipping and receiving space will have different lighting
requirements in each space.
What light levels are needed in each of the spaces? Do they vary by space? Are there
ASHRAE, IESNA, or OSHA code-level requirements?
FACILITY SIZE
APPLICATIONS
TYPE(S)
REQUIRED
LIGHT LEVELS
4 Digital Lumens
Four Steps to a Successful Lighting Evaluation
How high are the ceilings and do they vary within the facility? Are there any challenges or
impediments to hanging fixtures anywhere in the facility? Mounting height is one of many
factors that determine how many units, and of what type, need to be installed to achieve
desired illumination levels. Accurate height measurements are important.
Skylights, windows and frequently opened bay doors play a significant role in helping facilities to
save energy. It is important to document the number, size and location of these natural sources
of light so that fixtures can be placed in a way that allows incoming light to be used effectively.
For lighting purposes, occupancy refers to how frequently a space is occupied and therefore
requires lighting. While a building can be considered 100% occupied with only 1 person
present, lighting occupancy refers to the percentage of the building that requires lighting
based on where the staff are at any given time. For example, if there are 10 workers in
100,000 square-foot facility, the facility would be considered 10% occupied, although which
10% of the building is occupied at any moment changes as staff move through the space.
Refrigerated and frozen facilities challenge traditional HID and HIF lighting — with restrike
times, shortened ballast life, etc. — so it is important to document temperature ranges for
any chilled spaces.
Does your facility have over-sized machinery that makes reaching fixtures particularly
difficult, hazmat rooms that require specially-rated fixtures, or work zones that require
unusually intense lighting?
For facilities evaluating lighting retrofits (versus new build), it is also important to document:
Be specific and list all combinations of lighting, for example:
(147) 400-watt metal halide and (52) 8-lamp T5 fluorescent fixtures.
Measured in foot candles or Lux, it is important to record existing light levels within all
relevant work zones.
The distance between current fixtures can be maintained with the upgrade, or modified
depending on selected fixtures’ light output and optics.
In some projects, consider whether – based on ceiling height, fixture optics and lumen
output levels – you might be able to reduce the fixture count and still achieve target light
levels. This strategy can optimize project economics by reducing both fixture count and
installation costs.
What is your base cost per kWh? What are your peak demand charges?
What are your lighting energy costs?
If you need help collecting this data, lighting efficiency consultants are a valuable resource for completing in-house
evaluations, and a lighting audit is typically one of the first tasks they will perform when arriving at your facility.
NATURAL LIGHT
OCCUPANCY
CLIMATE ISSUES
UNIQUE
CHALLENGES
EXISTING LIGHT
TYPE(S)
& WATTAGE
EXISTING LIGHT
LEVELS
FIXTURE
SPACING
1-FOR-1, 1-FOR-2
ENERGY
COST
LIGHTING
ENERGY BILLS
HANGING HEIGHT
Digital Lumens 5
Four Steps to a Successful Lighting Evaluation
COMPARING SOLUTIONS: APPLES-TO-APPLES
With a thorough understanding of where you are today, your project goals, and the criteria for taking advantage of any
available utility incentives or tax benefits, evaluating lighting alternatives becomes just that much easier.
Now, it is time to do an ‘apples-to-apples’ comparison of the potential solutions – both on paper and in your facility.
‘Apples to apples’ is the key principle for this stage so that you consider functionally comparable solutions. We strongly
recommend documenting key information on alternatives in a spreadsheet for easy access and review. Make sure to
only include products that meet or exceed minimum light quality, performance and efficiency goals, and meet specific
requirements for:
• IP Rating and UL (or comparable international) listing;
• Incentive and tax benefit;
• Code compliance; and
• Energy-savings goals.
SAMPLE EVALUATION MATRIX
Fixture Details Alternative #1 Alternative #2 Alternative #3
Manufacturer Digital Lumens Name Brand without sensors
Name Brand with
add-on Sensors
Fixture Model DLE f ixtures (12K, 18K, or 24K) T5 8-lamp T5 8-lamp
Lumen Output 18,000
Fixture Wattage 180W
Fixture Optics Narrow or Wide Fixed standard lamping Fixed standard lamping
Color Temperature 5000K
Rewarding Long-Term Thinking
Many forward-thinking organizations are now using total cost of ownership (TCO) as a key measure
of an energy-eff iciency solution’s lifetime impact. In some cases, companies have revised incentive
structures so that project/performances bonuses are being awarded to managers and employees who
make the best long-term decisions for the organization, rather than simply choosing the cheapest
product available. With escalating energy prices, reductions in future energy use promise to deliver
ever-increasing levels of value. Restructuring incentive programs to align with these priorities ensures
long-term success in efforts to reduce overall energy intensity.
-Tom Pincince, President and CEO, Digital Lumens
6 Digital Lumens
Four Steps to a Successful Lighting Evaluation
Energy-Saving Controls Digital Lumens Name Brand without Sensors
Name Brand with
Add-on Sensors
Occupancy Sensors
(if yes, per f ixture or per circuit)?
Yes/Integrated into every
f ixture No Per circuit
Daylight harvesting sensors
(if yes, per f ixture or per circuit)?
Yes/Integrated into every
f ixture No
Must choose either
occupancy or daylight
sensors, not both.
Integrated controls for centrally changing
fixture settings and behaviors?
Yes. Controllable at the
individual fixture/zone/room
and/or facility level.
No
Manually pre-set at site.
Scissor lift required to
re-set for each circuit.
Range for timeout settings User-specified – from 30 seconds to hours Not applicable 15-minute minimum
Dimming control f lexibility? Between 0% and 100%, in 1% increments No
Step-level in
coarse increments
Ability to monitor/control
lighting by f ixture?
By zone?
Facility-wide?
Yes, monitor and control
Yes, monitor and control
Yes, monitor and control
No
No
No
No
Ratings & Certifications Digital Lumens Name Brand without Sensors
Name Brand with
Add-on Sensors
IP Rating IP52
Certif ications
UL for components,
as well as entire f ixture, CE,
UL-NOM
UL for
components only
UL for
components only
Design Light Consortium Qualif ied? 1 Yes No No
Lifetime Maintenance Rating2 200,000 hours
Lumen Maintenance Rating3 [TBD]
LM-79 Rating (for LEDs only)4 [TBD]
Digital Lumens 7
Four Steps to a Successful Lighting Evaluation
1
The “Energy Star” of industrial lighting, this listing is frequently required by utilities to grant highly valuable custom incentives.
2
For LEDs, this is the TM-21 value, the IEEE-approved standard for rating the lifetimes of LEDs.
3
For LEDs, this is the LM-80 value, the IEEE-approved standard for lumen maintenance ratings.
4
The IEEE-approved standard for evaluating thermal management, drive current and optical system eff icacy for LEDs. For more information, visit the
Illuminating Engineering Society www.ies.org or, if a member, the Institute of Electrical and Electronics Engineers (IEEE) at www.ieee.org.
IN-HOUSE EVALUATION: A CRITICAL STEP
In-house evaluations provide a valuable opportunity to experience potential lighting solutions in action, as well as
to validate key quality and energy savings metrics. Be sure to handle all fixtures before installation to assess their
construction. Then hang and compare fixtures, sensors and controls systems for the most accurate understanding
of exactly how a solution performs in your facility. A spec sheet cannot provide this facility-specific insight.
In-House Comparison Digital Lumens Name Brand without Sensors
Name Brand with
Add-on Sensors
Quantity of Fixtures
Ease of Installation
Ease of Commissioning
Ability to Change Settings
Fixture Construction Rugged with fully integrated sensors
Optics (narrow/aisle/wide)
Target/Actual Light Levels
Light Quality Clean, evenly distributed light output
System-generated data, reporting
Actual, metered data on
kWh use, occupancy
patterns…
Suitability to Purpose Excellent!
STEP 4: PERFORM A DETAILED FINANCIAL ANALYSIS
Now, it is time to sharpen the pencils and compare the solutions on paper. As outlined previously, it is critical to
evaluate the solutions along multiple dimensions because some solutions may have a faster payback, but markedly higher
lifetime costs, so it is worth the modest investment in spreadsheet time for the longer-term financial benefits.
Financial Analysis Digital Lumens Name Brand without Sensors
Name Brand with
Add-on Sensors
Proposed Quantity of Fixtures
Estimated Occupancy Rate6
Annual Refrigeration Savings7
Annual Maintenance Savings
Annual Energy Use8
Average kWh Rate
Annual Energy Cost9
Annual Maintenance Costs
Total Annual Cost10
Utility Incentives
Tax Deductions
TCO 5-Years
TCO 10-Years
Simple Payback (in years)
Warranty
Support
6
Using extensive data from customer installations, average occupancy rates by application are: 15% for cold storage; 41% for dock areas; 29% for
dry storage; and, 41% for manufacturing.
7
To be conservative, we use a 25% savings rate for planning purposes, although the average rate observed within our customer base is 45%.
8
(Number of f ixtures x Wattage x Occupancy Rate) + Refrigeration Savings.
9
Annual Energy Use x kWh Rate.
10
Annual Energy + Maintenance Costs.
REVIEWING THE FINDINGS
You have done the work — established evaluation criteria, gathered detailed operational data, tested various systems
in your facility, and run the numbers (payback, ROI and TCO). You now have a thorough, well-researched foundation
for choosing your lighting system. The question now is what your decision will be? Will you take advantage of the
opportunity to reduce lighting energy use, while improving performance and gaining new levels of operational insight?
We certainly hope so. s
All Rights Reserved © 2013-2014
Digital Lumens Incorporated
Subject to change without notice.
DOC-000229-00 Rev A 02-14
[email protected]
374 Congress Street, Suite 600
Boston, MA USA 02210
+1 (617) 723-1200