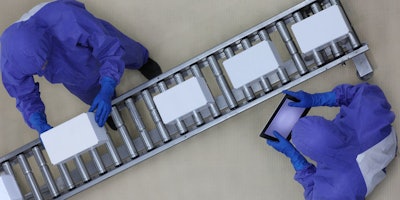
Positioning Your
Order Picking Team For
Success
White Paper
How automated goods‐to‐person storage and retrieval systems deliver ergonomic benefits that
yield higher productivity, better accuracy and reduced operational costs.
2 | P a g e
Introduction
Every sport — from cycling to soccer, golf to ice hockey — requires safety equipment to minimize the
risk of injury to athletes. Whether it’s special shoes with cleats or spikes for better grip on the ground,
pads and helmets that deflect impacts, or guards that shield the face, using the right gear keeps both
amateur and professionals safe. Without it, an injury could result not only in pain for the athlete, but in
the case of professional sports, negatively impact a team’s performance.
Likewise, when it comes to warehouse and distribution employees, more organizations are deploying
ergonomically designed automation systems. These ergonomic solutions help workers complete picking
and order fulfillment tasks while simultaneously eliminating the risk of injury. In addition to enhancing
safety, the devices can boost productivity and reduce a variety of costs — positioning both workers and
companies for operational success.
This white paper reviews the costs of injuries associated with overexertion, and explores three ways
automated storage systems improve worker ergonomics and productivity. It also shares an overview of
two different operations that implemented such a system and their results.
Common Ergonomic Injuries and Their Costs
Serious, non‐fatal workplace injuries cost U.S. businesses nearly $60 billion in direct workers’
compensation claims in 2012, according to a 2014 Workplace Safety Index study compiled by insurer
Liberty Mutual’s Research Institute.1 Within the Index’s top 10 ranking of the most frequent causes of
those injuries, two of the top five are associated with the physical exertion most frequently seen in
retrieval of stored items. They are:
1 Smith, Sandy. “Top 10 Workplace Injuries Cost U.S. Business $1 Billion Per Week.” EHS Today. January 7, 2015.
Accessed September 16, 2015. http://ehstoday.com/safety‐leadership/top‐10‐workplace‐injuries‐cost‐us‐business‐
1‐billion‐week‐photo‐gallery#slide‐9‐field_images‐37621
3 | P a g e
# 1: Overexertion injuries, involving “lifting, pushing, holding, carrying or throwing, cost
businesses $15.1 billion in direct costs and accounted for more than one quarter of the overall
national burden.”2
# 5: Exertion/reaction injuries resulting from “bending, crawling, reaching, twisting, climbing,
stepping, kneeling, sitting, standing or walking,” were responsible for 7.2% of the overall injury
burden, costing U.S. businesses $4.27 billion.3
Workers’ compensation insurance covers the direct costs of occupational injury and illness, such as
medical costs and wage replacement (indemnity). How much might an ergonomic injury cost?
The average cost of a back injury related workers comp claim can be $40,000 ‐ $80,000
per employee. The direct employee costs include musculoskeletal injuries, cost of
turnover (hire and train replacement employees), over‐time and temporary help, days
away from work, transition duty days, sick days used, and administrative costs of
handling compensation claims.4
Employers, however, also experience significant indirect costs associated with a worker injured on the
job — from two to 20 times5 higher than direct costs. That’s because there are so many hidden or
unanticipated expenses resulting from an employee injury. According to Occupational Safety and Health
Administration (OSHA), possible indirect costs can include (but aren’t limited to):
Any wages paid to injured workers for absences not covered by workers'
compensation;
The wage costs related to time lost through work stoppage;
Administrative time spent by supervisors following injuries;
Employee training and replacement costs;
Lost productivity related to new employee learning curves and accommodation
of injured employees; and
Replacement costs of damaged material, machinery and property.6
Clearly, the costs of an ergonomic injury can add up.
Regulations and Recommendations
Although the OSHA has not established a maximum limit on how much weight a person may lift or
carry,7 it does offer recommendations for the prevention of musculoskeletal disorders — including
2 Ibid.
3 Ibid.
4 Encompass Group. “The Direct and Indirect Costs of Workplace Injuries.” Accessed October 1, 2015.
http://www.encompassgroup.net/content/pdf/safe_patient_handling/Cost%20of%20Workplace%20Injuries.pdf
5 QBE Holdings Inc. “Direct and Indirect Accidents Costs.” Presentation by QBE Loss Control Services. Accessed
October 1, 2015. http://qbena.com/media/20161/accident%20costs%20qbe.ppt
6 United States Department of Labor. “Injury and Illness Prevention Programs White Paper, January 2012.”
Occupational Safety & Health Administration. Accessed October 1, 2015.
https://www.osha.gov/dsg/InjuryIllnessPreventionProgramsWhitePaper.html
4 | P a g e
muscle strains and lower back injuries. The agency also notes in 2011, the Bureau of Labor Statistics
(BLS) found warehousing to be one of four industries with the highest rate of musculoskeletal disorders
related to lifting heavy items, bending, reaching overhead, or pushing and pulling heavy loads.8
Taking the establishment of guidelines a step further, the National Institute of Occupational Safety and
Health (NIOSH) has developed a mathematical calculation to evaluate risk factors for manual material
handling tasks, such as lifting and lowering. According to NIOSH, the maximum recommended load
weight that a healthy worker can lift under ideal conditions is 51 pounds. When six other variables are
multiplied into the equation (horizontal location of the load; vertical location of the load; distance the
load is moved; degree of twisting required; frequency and length of lifting activity; and the worker’s grip
on the load), that maximum weight decreases.9
Companies that are well‐versed in these ergonomic issues, often having dedicated Health, Safety and
the Environment (HSE) teams to ensure that workers are safe on the job. They have already established
safe handling practices, such as blocking warehouse aisles when forklifts are retrieving or placing items
stored at heights, and using spotters to warn pedestrians and other workers in the area of activity
overhead. Others have begun lowering the maximum load weight they will allow an employee to lift
unassisted to 35 pounds — a full 16 pounds less than the NIOSH recommendations — as an aggressive
measure to further prevent musculoskeletal disorders.
7 United States Department of Labor. “Standard Interpretations.” Occupational Safety & Health Administration.
March 29, 2004. Accessed September 16, 2015.
https://www.osha.gov/pls/oshaweb/owadisp.show_document?p_table=INTERPRETATIONS&p_id=24876
8 United States Department of Labor. “Safety and Health Topics: Ergonomics ‐ Prevention of Musculoskeletal
Disorders in the Workplace.” Occupational Safety & Health Administration. Accessed September 16, 2015.
https://www.osha.gov/SLTC/ergonomics/index.html
9 Centers for Disease Control and Prevention. “Applications Manual for the Revised NIOSH Lifting Equation.” The
National Institute for Occupational Safety and Health (NIOSH). Accessed September 16, 2015.
http://www.cdc.gov/niosh/docs/94‐110/pdfs/94‐110.pdf
5 | P a g e
NIOSH and OSHA recommend that workers use powered equipment — such as automated storage and
retrieval equipment (like horizontal carousels, vertical carousels and vertical lift modules)10 and cranes
outfitted with an electric hoist11 — as an alternative to lifting loads manually. Here, a look at three ways
these automated storage systems improve worker ergonomics and reduce the potential for costly
injuries.
Solution: Automated Storage Systems to Minimize Exertion
To minimize the exertion injuries associated with manual material handling processes (including lifting,
reaching, walking, stretching, bending, stooping, pulling, pushing, twisting, gripping and climbing), a
variety of automated goods‐to‐person storage and retrieval systems exist. These include:
Horizontal Carousels – Bins mounted on an oval track that rotate horizontally to deliver storage
locations to an operator.
Vertical Carousels – Comprised of a series of shelves that rotate around a track—similar to a
Ferris wheel—these systems deliver stored items safely and quickly to an ergonomically
positioned work counter.
Vertical Lift Modules (VLMs) – A vertical lift module (VLM) consists of two columns of trays
holding items. An automatic inserter/extractor device between the columns stores and retrieves
a tray when required by an operator.
Minimize Fatigue, Improve Accuracy
All three of these automated storage and retrieval systems eliminate unproductive and physically tiring
travel and search time by delivering required items directly to the operator on command. Workers in
conventional warehouses spend as much as 60% of their time walking to product,12 searching for it on a
shelf, and climbing on a ladder to reach items stored high, or kneeling down to access items stored low.
With an automated storage system, a worker no longer has to spend as much time on travel or retrieval
of items. Not only does limiting an operator to just a few steps to complete picking tasks dramatically
reduce fatigue, it also boosts picking rates by as much as 600%.
Further, a less‐fatigued worker is a more accurate one. Tired operators are more likely to make
mistakes. In addition to minimizing fatigue caused by exertion, these automated goods‐to‐person
systems can prevent errors when equipped with a variety of supporting technologies. Additions such as
light‐directed picking systems and monitors that display images of the items to be picked further errors,
resulting in up to 99.9%+ picking accuracy.
10 Ibid. 47.
11 National Institute for Occupational Safety and Health (NIOSH). “Ergonomic Guidelines for Manual Material
Handling.” DHHS (NIOSH) Publication No. 2007‐131. 45. Accessed September 16, 2015.
http://www.cdc.gov/niosh/docs/2007‐131/pdfs/2007‐131.pdf
12 Ruriani, Deborah Catalano. “Improving Picking Practices.” Inbound Logistics. September 2006. Accessed October
1, 2015. http://www.inboundlogistics.com/cms/article/improving‐picking‐practices/
6 | P a g e
Go for the Gold(en Zone)
Every item stored in a vertical carousel and VLM is delivered to the operator at the optimal ergonomic
work height, called the “Golden Zone,” or waist‐high. (In the case of a horizontal carousel, the addition
of a lift table — coupled with proper slotting to ensure the most‐frequently‐picked items are at waist
height — achieves the same ergonomic benefit.) Shelves, trays or bins of products presented in easy
reach eliminates bending down to retrieve an item stored low, or stretching up to grab an item stored
high.
The machines also minimize unnecessary or excessive motions required for retrieval of items from
drawers or shelves, such as reaching, stretching, bending, pushing, pulling, or stooping. Likewise,
ladders, climbing and forklifts are not needed to place or retrieve items.
Further, VLMs can be equipped with a manual or automatic tray extractor for even easier load handling.
With a manual extraction device, the operator can easily glide the tray completely out of the VLM and
onto a cart or trolley. The tray of items can then be rolled to any destination within the facility, such as a
workstation for parts kitting or a work cell that requires tooling stored within the VLM. Upon its return,
the extraction device accepts the tray with minimal operator effort. Ideal for heavier loads (such as
dense, heavy parts, tooling, dies, molds and other components used in manufacturing or field service
and support operations), the automatic tray extractor mechanically slides the tray out of the machine.
This ergonomic assist function prevents a worker from having to reach inside the system to pull the tray
or item out.
7 | P a g e
Manual Tray Extraction
Automatic Tray Extraction
Need a Lift? Add a Hoist
As the most rugged of the three automated storage and retrieval systems, VLMs can be engineered to
hold a range of different load capacities per tray, including 4‐foot‐wide goods weighing more than 2,200
pounds up to 13‐foot‐wide items weighing in excess of 1,700 pounds. Loads that heavy are impossible
for an operator to lift. For such situations, a VLM can be equipped with an integrated, overhead crane
and electric hoist to provide further ergonomic handling assistance.
With a hoist rated for loads in excess of the 2,200‐pound VLM tray limit, an operator using a hand held,
wired control pendant can safely and confidently direct the lifting of the load from the tray, then
position it as needed. To accommodate different load types, the hoist can be outfitted with a variety of
customized below‐the‐hook attachments, end effectors or specialized tooling. For safety and control,
the hoist maneuvers the load to its destination precisely, at a fraction of the rated speed.
The hoist takes the strain of lifting the load off the worker, further reducing fatigue and lowering injury
risk. It also handles products gently to minimize damage and waste. Unlike forklifts, which are involved
8 | P a g e
in 20,000 serious injury accidents and 100 deaths annually13 and can be costly to own and maintain, the
integrated crane and hoist operate only with the VLM. This ensures the device is always readily available
when needed to transfer a heavy item into or out of the storage machine, unlike overhead warehouse
cranes engineered to maneuver large loads throughout a facility.
Shuttle VLM Fitted with Crane Handling Shuttle VLM with Crane Handling in Action
Working together, a VLM with an integrated crane and hoist ensures safe, ergonomic handling of heavy
loads by a single operator — no spotter required. Whether deployed as a stand‐alone solution or in
combination with other machinery, the system can be used as a production buffer, to supply assembly
lines, as a tool store or to distribute spare parts.
Other Benefits
Not only do horizontal carousels, vertical carousels and VLMs eliminate the fatigue and errors associated
with walk and search time and substantially decrease the risk of worker injury, adding these ergonomic
systems positions an operation to significantly reduce absenteeism, insurance premiums and claims for
worker’s compensation. Additional benefits include highly dense storage, reducing floor space
requirements by as much as 80%; fast access times; computerized inventory control for simplified
warehouse management; and interface modules that communicate with other warehouse management
systems (WMS) and enterprise resource planning (ERP) systems.
13 National Institute for Occupational Safety and Health (NIOSH). “Preventing Injuries and Deaths of Workers Who
Operate or Work Near Forklifts.” DHHS (NIOSH) Publication No. 2001‐109. Accessed September 16, 2015.
http://www.cdc.gov/niosh/docs/2001‐109/
9 | P a g e
Automated Storage Systems with Integrated Lift‐Assist in Action…
Zimbrick European Consolidates Parts into VLM, Eliminating Employee Travel Up
and Down Stairs
When Zimbrick European — an automotive dealer serving Mercedes‐Benz, Porche and Audi vehicle
owners with parts and service — moved into a new facility, the service parts department area dropped
from 2,300 square feet to 400 square feet. Further, the majority of the parts storage was located
upstairs, on a second floor mezzanine area.
"We [had no] means to move parts between the first floor and the second floor, short of running up and
down the stairs every time we needed to store a part or remove a part from inventory in order to sell
it," says Steve Stepnock, Zimbrick European’s
Parts and Service Director.
To solve both the space and ergonomic
problems, the business implemented a dual‐
access Shuttle VLM from Kardex Remstar. The
dual access model is equipped for access to
parts at both the first and second floor work
areas. The VLM access opening on the first
floor is located in the parts department,
directly behind the retail customer counter.
The opening on the second floor is located
near the freight elevator for convenient
receiving and storage operations.
"The Shuttle VLM reduced labor costs, increased productivity and reduced the risk of potential injury
from using the staircase," Stepnock explains. In addition to reducing parts employee fatigue, the VLM
accommodated the 84% reduction in storage space while still supporting 23 service technicians servicing
three different car lines within the facility. Productivity has increased by 70% without adding more staff.
Further, the fast‐moving, smaller parts stored in the VLM can be quickly and easily accessed
automatically. “It's absolutely seamless. With just a push of a button, the part is delivered to the first
floor," says Stepnock. “We also use the VLM to transfer [larger and slower‐moving] parts from second
floor bin storage to the first floor. We've saved ourselves two full‐time positions that would have
otherwise been required, simply to have people moving those parts between the floors manually."
Christie’s VLMs Help Employees Handle, Pick Heavy Projector Components
Projection technology manufacturer Christie custom‐builds systems for cinemas, education, media,
government and more. When the company sought to double its inventory of sub‐assembled projectors,
it switched from a cart‐based storage system to two Shuttle VLMs from Kardex Remstar.
10 | P a g e
The VLMs each hold 100 sub‐assembled projectors with room for more. Each VLM occupies only 180
square feet, compared to the 600 square feet occupied by the previous cart system, providing 70% floor
space savings. In addition to these benefits, the company has improved both ergonomics and safety —
thanks to the VLMs’ integrated, ergonomic
tray extractor and lift‐assist hoist.
With each projector weighing approximately
52 pounds, “the projectors are very heavy and
lifting them puts the employee at risk of
injury and the projector at risk of damage,”
explains Philip Hibberd, Senior Manufacturing
Engineer at Christie.
When the projectors were stored on carts,
employees had to push and pull them around,
contributing to fatigue. Once a cart reached
its designated production station, hoists were
available to transfer the projector — but not all employees utilized the hoists, putting some at risk for
back injuries.
Alternately, the new Shuttle VLMs are equipped with automatic tray extraction and a hoist mounted at
the operator access point. The operator processes the order with the click of a button, and the VLM
retrieves the tray with the required projector. Once the tray arrives at the opening, it is automatically
pushed out onto an extraction table for easy access. A software screen identifies the projector’s storage
position in the tray.
Because up to five sub‐assembled projectors rest closely together on the trays for maximum storage
density, workers must use the ergonomic hoist to easily access them. To pick, the operator uses hand
held controls to position the hoist over the item, hooks the two together, and again uses the controls to
lift the load. With the controls the operator guides the hoist to move and lower the projector onto a
transfer cart, where the two are disconnected. After pushing a button to confirm the pick, the tray
automatically retracts into the VLM.
In addition to introducing a safer, more ergonomic process by deploying the hoist‐supported VLMs,
projectors are retrieved 90% faster with half the number of employees previously required.
# # #
To learn more about how automated, goods‐to‐person storage and retrieval systems can improve your
operation’s safety and ergonomics — as well as space utilization and efficiency — contact your Kardex
Remstar representative today.
About Kardex Remstar
Kardex Remstar, LLC, a company of the Kardex Group, is a leading provider of automated storage and
retrieval systems for manufacturing, distribution, warehousing, offices and institutions. For information
about the company’s dynamic storage solutions, call 800‐639‐5805 or visit www.KardexRemstar.com.