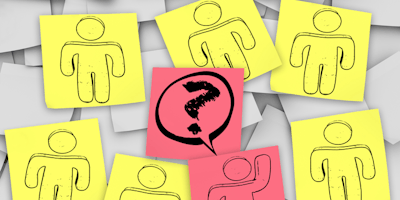
What Is Your ERP Solution NOT
Doing for Your Organization?
A new breed of business management solutions unifies people, processes
and information more effectively than traditional ERP
An Exact Whitepaper
What is your ERP NOT doing?
Many organizations have implemented a form of Enterprise Resource Planning (ERP) to
streamline manufacturing, distribution and financial processes. However, existing ERP
technology has left some yearning for the same level of efficiency throughout the entire
organization.
Valuable information about customers,
employees, vendor relationships and more is
typically locked within silos—from individual
databases to file cabinets to employees’
desktops. Moreover, traditional ERP systems
don’t encompass interactions with outside
parties such as customers, suppliers and
business partners. While ERP does a fine job
of tracking manufacturing, distribution and
accounting processes, businesses must under-
stand the context behind these transactions to
truly maximize efficiency and effectiveness.
Those organizations that have implemented
their ERP software three to five years ago or
more are likely currently evaluating upgrades
with the belief that the latest version and
functionality will enable them to drive further
improvements to performance. In reality,
rather than upgrading their existing packages,
these businesses stand to benefit most from
analyzing the areas of the business which
their ERP system isn’t currently tracking, and
what can be done to better integrate these
areas.
A new breed of business management solu-
tions has emerged to unify all of these critical
areas—an organization’s people, processes
and information—within one comprehensive
solution.
History of ERP
ERP was developed to integrate all of the data
and processes of a manufacturing/distribution
organization into one, unified system. It came
about from the evolution of manufacturing
resource planning (MRP-II) that followed the
development of material requirements plan-
ning (MRP).
ERP initially caused a reduction in the soft-
ware applications that ran on the operational
side of an organization (financials, manufac-
turing, distribution, warehousing), but such
functionality only addressed the needs of a
limited portion of the enterprise (15 to 25
percent of total employees).
Through market consolidation and continued
development throughout the late 1990s and
into the 2000s, ERP continued to evolve and
add functionality that addressed the needs of
more and more of the organization.
Many organizations still think of ERP as a
“back-office” system that requires them to
operate database silos that house information
that first generation ERP systems did not
address (i.e.: HRM, CRM, and document
management).
With a large number of first-generation ERP
systems still operating today, organizations
are not realizing the full capabilities and
advantages that today’s ERP systems can
deliver. This paper will address what first-
generation ERP systems are not doing for
organizations and how recent developments
can help deliver greater efficiencies that have
substantial benefits and return on investment
for their businesses.
What is your ERP NOT doing?
ERP integrates a range of back-office func-
tions, such as materials planning, manufactur-
ing, distribution, shipping and accounting, to
help optimize performance within those areas.
Originally, ERP systems were designed to
bring automation that improved manufactur-
ing processes.
This included tracking issues such as raw
materials, work in process, inventory, order
entry and cost accounting. However, these
traditional systems are missing a tremendous
opportunity for improvement by leaving
front-office activities such as sales, marketing,
documentation and support out of the equa-
tion. Moreover, interactions with external
partners and vendors are not managed within
ERP systems.
What is your ERP NOT doing?
Mounting competitive pressures necessitate
that organizations achieve greater visibility
and cooperation across the entire enterprise.
Otherwise, they are lacking in their ability to
manage people, workflow and supply chain
issues to maximize efficiency in providing full
service to their customers. Typically, those
using ERP systems had little knowledge of
sales and service interactions beyond the
order transaction and shipment. Likewise,
sales and support teams could only tap into
ERP systems to see order status, inventory
levels, accounting issues and the like, but
they were not supported in their need for
customer requirements, contact management,
complex sale process and knowledge manage-
ment.
Today, savvy business leaders recognize the
pressing need for real-time views across front
and back-office operations so they can gauge
and continually improve the health of their
business as a whole. They are faced with
increased pressure to monitor key drivers of
internal performance, yet they are also tasked
with accomplishing more with fewer
resources.
Another important challenge with traditional
ERP systems is the lack of integration
between real workflow processes and associ-
ated documentation. Surprisingly, most
employees still rely on email for their “to do”
lists. However, this means important informa-
tion and supporting materials are often hidden
on individuals’ desktops instead of being
shared as knowledge across internal teams
and throughout the organization.
Businesses require a system which eliminates
these informal communication traps; they
must integrate information assets, track
interactions and share knowledge and docu-
mentation internally as well as with key
customers, partners and vendors.
The lack of broader systems can also nega-
tively impact accountability practices.
This issue has become pressing as businesses
face more stringent federal regulations and
industrial certifications, such as ISO, that
require a considerable level of traceability.
Companies across a range of industries—from
pharmaceutical to financial markets—need a
framework to ensure compliance with relevant
regulations.
An enterprise-wide solution
Progressive-minded businesses are moving
away from this dated model toward compre-
hensive business management solutions that
facilitate the free flow of people,
process and information. Today’s enterprise-
wide systems connect ERP systems with
customer relationship management (CRM),
human resources management (HRM),
document/knowledge management, financial
and workflow management systems.
By seamlessly integrating every facet of the
value chain, organizations not only have a
record of what is happening within the busi-
ness, but the added context of understanding
the implications of these interactions—greatly
enhancing decision-making.
Most importantly, an enterprise-wide system
shows the interrelationship among various
facets of the business. For example, a sales
rep now has insight into the billing status of
an account before visiting that customer; a
marketing manager is able to see what excess
inventory is still available before choosing
which product to promote in a direct mail
campaign; a shop floor manager can see
which products cost the most to produce.
These open processes foster greater collabo-
ration both inside and outside of the organiza-
tion, leading to improved performance and
increased profitability.
In addition, by bringing together multiple
disciplines and knowledge bases, organiza-
tions can identify the direct and indirect
influences upon their operations. For example,
customers are empowered to access their
account information and easily place orders,
greatly enhancing their relationship and
satisfaction with the business, while suppliers
can interact with the organization more read-
ily with the ability to check inventory on hand.
This type of all-encompassing system has
proven beneficial for strengthening an
organization’s ability to capture and retain its
intellectual capital while controlling access to
sensitive information. Instead of information
sitting in a file cabinet or on an individual’s
laptop, access is controlled via rules- and
role-based guidelines. This opens lines of
communication with outside partners, suppli-
ers and customers while providing greater
controls over, and visibility into, who has
access to what information.
Mounting competitive pressures necessitate that organizations achieve
greater visibility and cooperation across the entire enterprise.
What is your ERP NOT doing?
Another commonly overlooked area of impor-
tance to achieving maximum efficiency is
proper workflow. Correctly designed, workflow
systems can unify people, processes and
knowledge in the most economical and appro-
priate manner. Workflow does not depend on
a crude “send only” model such as email, but
on a process-centric view in which the system
ensures that all assigned tasks are completed
or elevated if the appropriate resolution has
not been attained. Certain actions can trigger
events, resulting in a chain of activities across
the enterprise, so that nothing falls through
the cracks and proper authorities are notified
of any potential issues in the production chain
before they become a larger problem.
Benefits of an enterprise-wide solution
With visibility across the front-office and
back-office within the context of ERP, organi-
zations are able to quickly uncover hidden
costs, inefficiencies and redundancies. What
if, for example, the business could access an
accurate, up-to-the-moment view of its
personnel, finance, workflow, documents and
asset information? This would give all mem-
bers of the value chain meaningful data for
making smarter decisions. The enterprise-
wide solution could encompass any number of
applications previously isolated from view-
from CRM to HRM to document and project
management. Moreover, it could incorporate
key functions such as workflows to increase
operational efficiency.
However, simply sharing information internally
may not be enough. Many organizations are
extending this collaborative model, providing
staff, customers, suppliers, business partners
and investors with access to a single database
of knowledge. The benefits of this are numer-
ous.
• Reduction in the cost of data capture,
management and maintenance. Data of all
kinds, including purchase orders, delivery
notes, etc. could be stored and classified
electronically, connecting both transactions
and participants in a single location.
• Immediately speeds the retrieval and
audit processes across the organization and
organizes the documents needed to address
financial, industry or quality certifications.
• Optimization of process flows reduces
the number of actions required to process a
transaction.
• Interactive planning provides the
organization with a complete picture of
current activities and investment effects in
addition to the typical data of orders and
margins. Thus it is not only possible to control
the company on the basis of the traditional
profit and loss accounting, but also to identify
and measure the return on investment on
complex process investments such as
marketing-through-sales close and multi-
department customer service.
Branching out beyond manufacturing and
distribution
Today’s ERP applications are no longer just for
manufacturing or distribution organizations.
All organizations must track the costs of doing
business and gauge performance toward goals
and forecasts. Advanced ERP solutions even
allow for establishing and tracking project,
grant or retainer-based billing and revenue,
and thus are a perfect fit for professional
services, research or venture-backed busi-
nesses.
Most service organizations face significant
challenges related to accurately and efficiently
capturing time and expenses, managing
work-in-progress, generating and approving
invoices or reporting on project and client
status. ERP has traditionally handled such
tasks for manufacturers, but has recently
branched out into solving such tasks for
services-based firms.
Complementary applications
With a wealth of information at the ready, it
makes sense to find better ways to analyze
and respond to this data, transforming it into
actionable information that impacts decision-
making and performance. To that end, many
organizations integrate business analytics and
exception management applications into their
enterprise-wide ERP systems.
Business analytics is not just a modernized
reporting mechanism; it also affords manag-
ers a way to identify and take advantage of
trends. It offers the power to quickly and
easily build information views while dynami-
cally combining and comparing data from
multiple sources or different business func-
tions. Business analytics applications are
attractive because they give busy
Today’s ERP applications are no longer just for manufacturing or
distribution organizations.
What is your ERP NOT doing?
professionals a way to quickly interpret busi-
ness metrics and key performance indicators.
Through business analytics, users can also
access vital business information with greater
consistency, perform in-depth analysis and
share the results throughout the organization.
They may choose to create personalized
information views that are distributed based
on a pre-defined schedule, or produce ad-hoc
reports as needed.
Of additional value are applications that allow
the user to define specific events, or excep-
tion events, that require monitoring. This is
useful in the case where you want to auto-
matically trigger certain steps or actions in
response to a data or transaction condition –
for example, initiating a specified workflow
within the system when inventory levels fall
below a set level, sending an email or pager
message to management, or generating a
report. This is an ideal way to initiate early
awareness and detection of problems (such as
a customer whose purchasing has fallen off in
the past three months, or a customer who
exceeded a credit limit) and then obtain the
proper resolution before they become serious
issues.
Summary
ERP systems that are extended with inte-
grated front-office systems have matured to
the point where they are finally beginning to
deliver on the promises of the past-
extending efficiencies across the entire orga-
nization instead of merely to discrete areas or
departments. This continued growth and
evolution of the technology is particularly
beneficial to small and mid-sized businesses,
which are under intense pressure to operate
in a much leaner mode than their counter-
parts at larger organizations.
Through greater centralization of critical
business information for real-time decision
making, companies put themselves in a better
position to boost profitability and reduce
operational costs, increase accuracy and
timeliness of cost allocations and ultimately
maximize financial decisions that shape the
future of the company.
Exact. And it all comes together.
Exact is a leading global supplier of business
software. Since we began in 1984, our focus
has shifted from supporting financial
processes to providing a complete ERP offer-
ing for small and medium-sized businesses.
Innovative solutions such as Exact Globe,
Exact Synergy and Exact Online support over
100,000 customers – local and international
companies – in the daily management of their
business.
Exact develops industry-specific on-premise
and cloud solutions for manufacturing, whole-
sale and distribution, professional services
and accountancy. Exact is headquartered in
Delft, the Netherlands, and has been listed on
the NYSE Euronext Amsterdam since June
1999. The company booked revenue of €
217.1 million in 2012.
For further information about Exact, visit
www.exact.com and
http://macola.exactamerica.com
© Exact Group B.V., 2013. All rights reserved. All trademarks mentioned herein belong to their respective owners.